The two best welders I've seen for automotive art were sharing and comparing their styles a couple of years back on this thread
http://www.yellowbullet.com/forum/sh...ad.php?t=97936 I've copied and pasted bits from their posts.
Aaron from
6061 6061.com Intake elbows (site currently down): I usually use 5052 sheet because it is strong and it can be bent/formed without it wanting to crack like 6061. 3003 sheet is soft and easier to form into shapes, but not as rigid.
I use 5356 filler rod despite what some articles say. Most say the 4043 gives a better weld appearance. For me, 5356 seems to shine better. 4043 seems to work better (for me) when welding on cast intakes. I also noticed that hammer-forming a part after welding with 4043, it seemed to want to crack easier.
On my welder, I keep the balance in the 65-68% area, and adjust the positive amperage about 25% lower than the negative. On most welders, adjusting the positive and negative amperage independently isn't an option.
There are also waveform adjustments on the dynasty 350... I leave mine on soft squarewave.
Hertz anywhere above 300. When welding most of my parts, I can get the tip to stay sharp and not ball up with the ceriated tungsten. The high hertz adjustment and adjusting the positive/negative amperage values independently keeps the heat off the tungsten.
Here's an example of his work
John Marcella
Marcella Manifolds Home Page : The newer style machines w/ an inverter have a hertz adjustment and with running more hertz it has a tendency to narrow the arc. If all your doing is looking to minimize the white fuzz on the side of the weld you can achieve it by running more negative balance and a higher hertz adjustment. However this is not of any importance when dialing in the correct settings. As far as machine settings it is very difficult to give advise because even though material thickness may be the same the size of the panel and even the thickness of the medal on the table you are welding on all greatly effect how fast the heat is dissipated. I almost never use the pulser, but lately I have been playing around with it and have had pretty good results. (the pulser does not change the look of the weld it just limits the amount of heat that gets put into the part). I personally rarely use 5052, I usually use 4043.
I prefer a different tungsten on different machines because the machine basically preferred different tungsten. On the sincrowaves the green was ok, but if I could get away with it I would use the red. I tried the ceriated that Aaron says he uses but I didn't like it, I ground the rest of the box and used them as scribs. On the aerowave it really likes the lanthenaited, however my dynasty hates it. What I use on my dynasty is the 2% thoraited (red). All the different types of machines will react differently. I use ceriated (orange or grey band) or thoriated (red). I don't really prefer one over the other. I never use green anymore... it seems to get contaminated too easy and the tip doesn't stay as sharp.
John's LS manifold
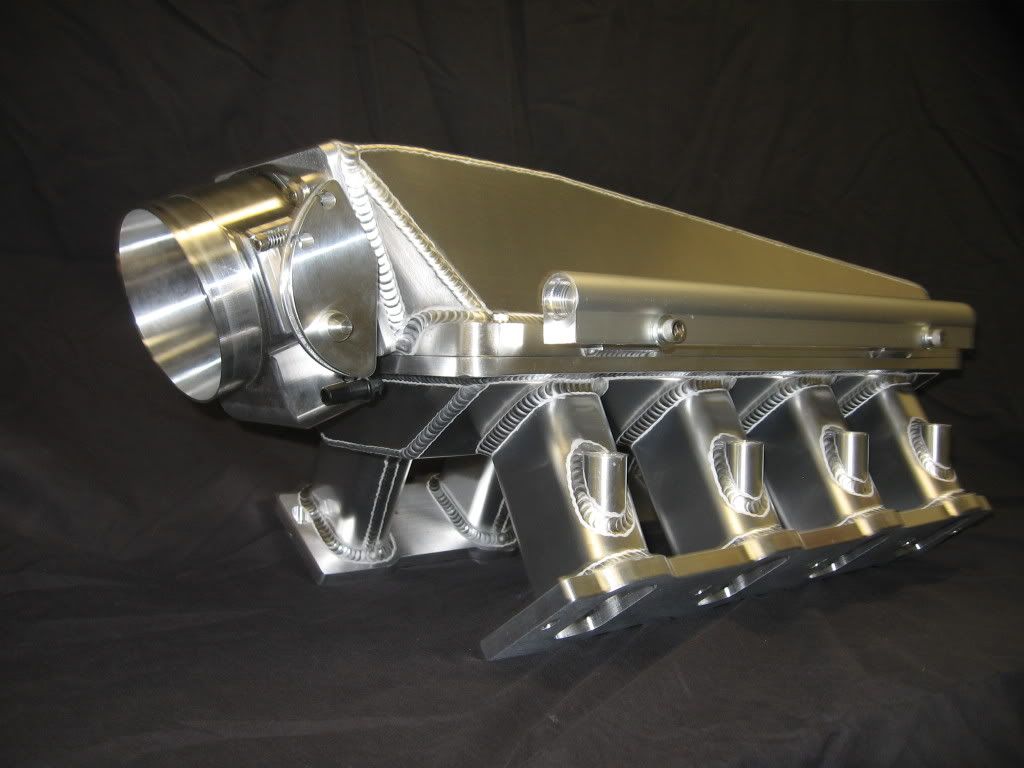