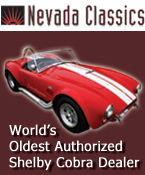 
Main Menu
|
Nevada Classics
|
Advertise at CC
|
S |
M |
T |
W |
T |
F |
S |
|
|
|
1 |
2 |
3 |
4 |
5 |
6 |
7 |
8 |
9 |
10 |
11 |
12 |
13 |
14 |
15 |
16 |
17 |
18 |
19 |
20 |
21 |
22 |
23 |
24 |
25 |
26 |
27 |
28 |
29 |
30 |
31 |
|
|
CC Advertisers
|
|

10-27-2008, 02:47 PM
|
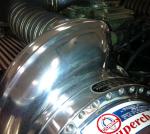 |
Full Blown Member
|
|
|
Join Date: Sep 2008
Cobra Make, Engine: KMP 427 S/C, Twin Paxton 511 FE
Posts: 2,594
|
|
Not Ranked
Drilling fiberglass
I have an SPF windshield mounted mirror that I want to change out for a cowl mounted mirror (the windshield mirror is just as useless, I just want accuracy).
I spoke to a guy at Hillbank and he says it's just as simple as drilling wood, you just use a metal type screw (that comes with the mirror, of course) instead of a wood screw. My concern is tightening the screw and having a chunk of the dash come off. Are these concerns valid?
Any tips or tricks?
Thanks
|

10-27-2008, 02:50 PM
|
CC Member
|
|
|
Join Date: Jan 2008
Cobra Make, Engine: Venom 427sc
Posts: 212
|
|
Not Ranked
First you want to use some masking tape where you drill and start off with a smaller size bit and work up to the size you want. glass tends to splinter so you must go slow.
joeg
|

10-27-2008, 03:07 PM
|
 |
Senior Club Cobra Member
|
|
|
Join Date: Mar 2002
Location: God's country,
ME
Cobra Make, Engine: Original ERA 427sc, Powered by Gessford
Posts: 2,678
|
|
Not Ranked
in addition to the above, get yourself a new (or at least very sharp) bit.
__________________
Replica is not a dirty word.
"If you can't be a good example, then you'll just have to be a horrible warning."
|

10-27-2008, 03:22 PM
|
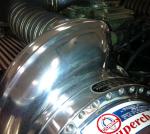 |
Full Blown Member
|
|
|
Join Date: Sep 2008
Cobra Make, Engine: KMP 427 S/C, Twin Paxton 511 FE
Posts: 2,594
|
|
Not Ranked
bit size?
Any idea on what the size bit should be?
|

10-27-2008, 06:00 PM
|
 |
CC Member
|
|
|
Join Date: Feb 2004
Location: Milford,
CT
Cobra Make, Engine: BRG ERA street car w/428 PI, Sunburst wheels, undercar exhaust, original interior, no philips head screws!
Posts: 650
|
|
Not Ranked
I had the same question and if you search the threads you'll see the answers. In general..it's all been said...mask the area, start with a small diameter hole, work up to the size you need, drill slow...some one even recommend drilling backwords...it's more scary then anything but if you take your time it will cut through like "buttah" as Linda Richmond says (from SNL). I got a scrap piece of glass from Peter at ERA and practiced on that to get my confidence up. It is really simple and easy. I also took it a step further and reamed the hole with a reaming bit.
As for starting sizee you can go either by sight or the best is to use a micrometer to see you ending circumfrence then work down from there.
Hope this helps.
|

10-27-2008, 06:58 PM
|
 |
CC Member
|
|
|
Join Date: Jan 2002
Location: Bridgewater,
NJ
Cobra Make, Engine: B & B
Posts: 1,323
|
|
Not Ranked
Also,
I don't know if it makes a big difference but after drilling the hole to the final size, I like to use a countersink bit to just ease the top of the hole a bit. This way you have a small bevel around the drill hole. I find you don't get as much splintering and it allows for the screw to go right in. I believe it also stops the paint from chipping beyond the drilled hole.
__________________
Just enough knowledge to build a cobra and be dangerous...
You can observe a lot from just watching.
|

10-27-2008, 07:10 PM
|
CC Member
|
|
|
Join Date: Feb 2008
Location: Jacksonville,
FL
Cobra Make, Engine: Kirkham #570 w Shelby FE
Posts: 1,009
|
|
Not Ranked
Best practice is to not rely on the fibergass to hold the screw. Use a backing plate of sheet metal and thread the screws into this, not the fiberglass itself.
I've yet to see fiberglass not form stress cracks over time from the weight of items screwed to it, especially on boats that take a lot of pounding.
I'd also recommend fabricating a rubber gasket under the base of the mirror.
|

10-27-2008, 08:37 PM
|
 |
CC Member
|
|
|
Join Date: May 2001
Location: California,
Ca
Cobra Make, Engine: NAF 289 Slabside Early Comp Car with 289 Webers and all the goodies. Cancelling the efforts of several Priuses
Posts: 6,592
|
|
Not Ranked
Use 10-32 machine screws with oversize (fender ?) washers with nylock nuts. Ronbo's suggestion of a rubber gasket is on target.
The drill bits for use on FRP have a sharper point than those normally used for metal and drill easier.
__________________
Rick
As you slide down the Banister of Life, may the splinters never be pointing the wrong way
Last edited by Rick Parker; 10-27-2008 at 09:07 PM..
|

10-27-2008, 09:10 PM
|
 |
Senior Club Cobra Member
|
|
|
Join Date: Jan 2001
Location: Santa Barbara, Ca.,
ca
Cobra Make, Engine: R.U.C.C. with a 427FE, toploader
Posts: 1,435
|
|
Not Ranked
"some one even recommend drilling backwords"...Do it!
__________________
Mike Z
Nothing sucks more than that moment during an argument when you realize you’re wrong.
|

10-28-2008, 08:37 AM
|
 |
CC Member
|
|
|
Join Date: Dec 2000
Location: Livermore,
CA
Cobra Make, Engine: ERA #629, BBM Side Oiler Block, 482ci, Richmond 5 speed
Posts: 852
|
|
Not Ranked
Drilling in fiberglass is amazingly easy. I'm not saying don't be careful but it's not at all difficult to do. What's more important is to make sure you get the hole the right size. That is, don't undersize the hole and then "force" the screw in. You can easily break the head off of screws when screwing them into fiberglass if the screw is of the cheap "chinese" variety. I speak from experience. I had to move my cowl mounted mirror over 1/2 inch to cover up a screw that I broke off in the cowl. I'd even suggest replacing the screw that comes with your mirror with a stainless steel one if you can find one at your local hardware store.
Chris
|

10-28-2008, 11:43 AM
|
CC Member
|
|
|
Join Date: Mar 2005
Location: Chardon, Ohio,
OH
Cobra Make, Engine: Classic Roadster II, 351 windsor, Tremmec T-5
Posts: 98
|
|
Not Ranked
Another option
I wasn't fond of like the idea of a sheet metal screw in fiberglass, so I epoxied stainless steel T-nuts to the underside of the holes, with the sleeve of the T-nut inside the hole. T-nuts can be purchased with holes punched in the T-nut flange and that permits the epoxy to "ooze" up through the holes and,I believe, give it could make a stronger bond.
I have also had good success using sheet metal step drills for making holes in fiberglass. Beats step drilling with individual drill bits.
Oh,... yeah. I forgot to mention, that the reason I liked using T-nuts is that the sheet metal screws can then replaced with machine screws. Then they can be removed and reinstalled al much as you wish and not eventually produce "a loose screw in a sloppy hole" situation.
Last edited by TWOOD; 10-28-2008 at 12:05 PM..
Reason: Added comment
|

10-28-2008, 11:45 AM
|
 |
CC Member
|
|
|
Join Date: Apr 2008
Location: Mechanicsburg,
PA
Cobra Make, Engine: Everett-Morrison, 429CI
Posts: 98
|
|
Not Ranked
When determining what size drill to use if you use a drill bit that is the same or a few thousands larger than the minor diameter of the thread you will be good to go.
|

10-28-2008, 01:06 PM
|
 |
CC Member
|
|
|
Join Date: Aug 2006
Location: San Diego,
CA
Cobra Make, Engine: SPF1715, Roush Built 434 ci Stroker, Dart Block, Ported AFR 205 Heads... 561 hp / 547 tq, Former Roush Show Car, Completed and Prepped By Olthoff Racing.
Posts: 1,066
|
|
Not Ranked
Quote:
Originally Posted by Ibr8k4vetts
"some one even recommend drilling backwords"...Do it!
|
You can also use a countersink bit to cut the glass before drilling the hole. This will keep the drill bit from lifting the finished surface off the glass. I learned this from a boat rigger.
|

10-28-2008, 03:19 PM
|
CC Member
|
|
|
Join Date: Mar 2006
Cobra Make, Engine:
Posts: 277
|
|
Not Ranked
Plug in "plastic stress cracking". It explains the whole thing. In boat work we often drill the hole slightly oversize, wrap the machine screw with 1 or 2 wraps of teflon tape, and set the screw in thickened epoxy. When the epoxy sets the stress is allowed for, and the teflon allows you to back the screw out to install the fitting. Do it all the time in big ocean racers.
|

10-28-2008, 03:41 PM
|
 |
CC Member
|
|
|
Join Date: Feb 2004
Cobra Make, Engine: FFR 390 toploader IRS
Posts: 258
|
|
Not Ranked
use a uni-bit. Thru bolt using machine screw and nylocks. anything mounted to a painted surface should have rubber under it.
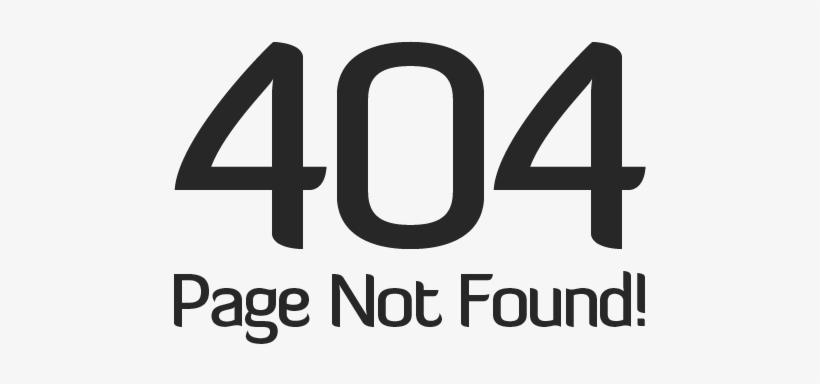
__________________
FFR MarkIII,FE,toploader,IRS,3.27,Vintage pin's SOLD!
68 F100 Custom Cab 418 cube FE/auto
99 SuperDuty Tuner/chipped/4" Banks TOTALED!!
02 Super Duty 7.3L
|

10-28-2008, 04:04 PM
|
CC Member
|
|
|
Join Date: Sep 2007
Location: Marlboro,
NJ
Cobra Make, Engine: Contemporary Cobra
Posts: 923
|
|
Not Ranked
tapping
all of my boats were repainted with awcraft. We always taped the holes, most places on a sailboat (the deck) can't be reached for a washer and nut.
NEVER had on pull on me, always countersunk the hole and always tryed to do this before painting...paint never cracked..good luck
|

10-28-2008, 08:04 PM
|
CC Member
|
|
|
Join Date: Feb 2008
Location: Jacksonville,
FL
Cobra Make, Engine: Kirkham #570 w Shelby FE
Posts: 1,009
|
|
Not Ranked
Although it's not relevent to this application, in a blind hole situation use well nuts if possible. Always isolate with rubber to prevent vibration shock being transferred to the fiberglass substrate.
Big problem with fiberglass is the gelcoat / paint surface is far more rigid than the fiberglass underlayment.
BTW carbide burrs are the best thing I've ever used to drill into glass, the more cutting edges the better.
|

10-28-2008, 09:46 PM
|
CC Member
|
|
|
Join Date: Aug 2004
Location: Tarpon Springs,
fl
Cobra Make, Engine: scratch building
Posts: 182
|
|
Not Ranked
Nuts
Take a look at the large flange rivnut, they come in fractional and metric, steel and aluminum. May be good for other uses too.All my aluminum panels will be held on with rivnuts instead of regular rivets.
Al
|

10-29-2008, 12:44 AM
|
CC Member
|
|
|
Join Date: Jan 1999
Location: Bakersfield,
CA
Cobra Make, Engine: HI-TECH 289 FIA
Posts: 363
|
|
Not Ranked
Best solution I have found for fiberglass threading and occasionally in aluminun are slotted body rivet nuts. Very secure and easy to use, either in a blind situation or exposed. See page 3214 at http://www.mcmaster.com/.
Same type of fastener as used in dry wall. Unit mushrooms on the backside for a large surface area. Any Good nut shop should have them.
__________________
fiaroadster
|

10-29-2008, 01:04 AM
|
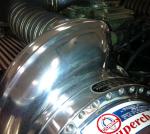 |
Full Blown Member
|
|
|
Join Date: Sep 2008
Cobra Make, Engine: KMP 427 S/C, Twin Paxton 511 FE
Posts: 2,594
|
|
Not Ranked
Thanks for all the help. Lots of handy folks here.
I never expected this response!
|
Posting Rules
|
You may not post new threads
You may not post replies
You may not post attachments
You may not edit your posts
HTML code is Off
|
|
|
All times are GMT -7. The time now is 06:39 AM.
Links monetized by VigLink
|