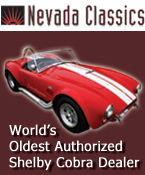 
Main Menu
|
Nevada Classics
|
Advertise at CC
|
S |
M |
T |
W |
T |
F |
S |
|
|
|
|
|
|
1 |
2 |
3 |
4 |
5 |
6 |
7 |
8 |
9 |
10 |
11 |
12 |
13 |
14 |
15 |
16 |
17 |
18 |
19 |
20 |
21 |
22 |
23 |
24 |
25 |
26 |
27 |
28 |
|
|
CC Advertisers
|
|
10Likes

03-28-2022, 10:10 PM
|
CC Member
|
|
|
Join Date: Sep 2020
Posts: 84
|
|
Not Ranked
Bolt Pitch
I'm ready to reinstall my rear differential after I sheared the front differential bolt. I replaced the front and rear differential bushings, resealed the differential cover, polished (sort of) the scratched up output spacers, ordered new bolts and washers for anything I had to remove. The sheared bolt was 14mm. I assumed backdraft replaced the bolt?? Regardless, when I ordered the new front bushing it came with a 10.9 14mm 150 pitch bolt (Condor). The new bolt was about 1/2' longer than the sheared bolt and threads were different. The new bolt would not screw in the differential. I took the sheared bolt to Fastenal. They measured the bolt pitch and it was 200 not 150. I ordered two 12.9 14mm x 80mm 200 pitch allen head bolts. These bolts fit the differential. Everything I've read said I needed a 150 pitch bolt. Does anyone else use 200 pitch bolt. Is this going to be an issue? I was told not re-tap the differential from a 200 to 150 pitch (need to go up a size). Thanks for the help.
Mike
https://www.condorspeedshop.com/prod...30980504289326
|

03-29-2022, 01:33 AM
|
 |
CC Member
|
|
|
Join Date: Aug 2009
Location: Adelaide,
SA
Cobra Make, Engine: AP 289FIA 'English' spec.
Posts: 13,152
|
|
Not Ranked
When you say 200 pitch of 150 pitch, you are referring to 2.0mm and 1.5mm, I assume?
Do not re-tap the thread in the diff. under any circumstances. edit: reason for not re-tapping with a different pitch thread - you would be completely destroying some of the threads in the tapped hole in your diff. housing
Cheers,
Glen
Last edited by xb-60; 03-29-2022 at 06:00 PM..
Reason: edit
|

03-29-2022, 09:24 AM
|
 |
CC Member
|
|
|
Join Date: Jun 2000
Location: Cape Town, South Africa/Mainz, Germany,
Posts: 1,601
|
|
Not Ranked
M14 x 1.5 mm or M14 x 2.0 mm. There is no 150 or 200 pitch.
The pitch (distance from one root, or tip) between treads is 1.5 mm or 2.0 mm.
The diameter of the bolt is 14 mm.
Note: The 1.5 mm pitch has a root diameter of 12.5 mm. If you ever like to tap a M14 x 1.5 into a hole, drill 12.5 mm. And, who guessed it: The 2.0 mm pitch has a 12 mm root diameter.
You cannot tap the one into the other. That's like tapping a 3/8 UNF into a 3/8 x 13 UNC bore.
Interesting trivia:
A M12 x 1.25 mm bolt fits into a 1/2" x 20 UNF (or 1/2" x 20 UNF nut onto a M12 x 1.25 mm stud). BUT will NOT give a tight fit - obviously. Happens with wheel or cylinder head fasteners.
Last one:
3/8" x 24 UNF brake line fitting screws down M10 x 1 mm metric equivalent. Will never seal!
__________________
If I don't respond anymore, that's because I can't log in
|

03-29-2022, 10:13 AM
|
CC Member
|
|
|
Join Date: Sep 2020
Posts: 84
|
|
Not Ranked
Sorry guys I’m not expert. In fact I had no idea what bolt pitch meant until a couple of weeks go. Yes, i meant 1.5 vs 2.0. I’m worried about retap differential. I could that going bad for a number of reasons. After reading a little more about bolt pitch I feel like the 1.5 would be preferable but the the 12.9 14mm 2.00 bolt would work fine. I think I’m talking myself into going with the 12.9. 14mm 2.00 bolt. I haven’t driven the car in over a month. Is this a mistake ands it’s going to bite me done the road? I appreciate the feed back. Thanks, Mike
|

03-29-2022, 12:03 PM
|
 |
CC Member
|
|
|
Join Date: Feb 2006
Location: Gilroy,
CA
Cobra Make, Engine: SPF 2291, Whipple Blown & Injected 4V ModMotor
Posts: 2,738
|
|
Not Ranked
169mph, look at where you original fastener broke. It broke at the root of a thread. Thread roots are high stress locations on fasteners. Threads are not meant to be placed in shear (side) load, they are meant to apply a tensile loading to tighten the fastener. If you side load a torqued fastener at the root of a thread it will break — maybe not today and maybe not tomorrow but it will break.
The load bearing area / surface of a fastener is the unthreaded shank of the fastener. This is where the load should be applied. The fastener you have sourced is a replica of the fastener that broke. Both require a longer shank to protect the threaded portion of the fastener from a shear load (side load).
If you replace the original with a duplicate you will duplicate the failure you have already experienced. Buy the proper fastener to prevent a repeat performance.
__________________
Help them do what they would have done if they had known what they could do.
Last edited by eschaider; 03-29-2022 at 12:05 PM..
Reason: Spelling & Grammar
|

03-29-2022, 08:42 PM
|
 |
CC Member
|
|
|
Join Date: Jun 2020
Location: SoCal,
CA
Cobra Make, Engine: BDR build #983, FRM 392
Posts: 380
|
|
Not Ranked
Does the different appearance between broken bolt and the replacement allan head bolt indicate a difference in strength between these two bolts? Specifically referring to the color difference between the bolts.
Last edited by SBSerpent; 03-29-2022 at 08:45 PM..
|

03-29-2022, 09:33 PM
|
 |
CC Member
|
|
|
Join Date: Feb 2014
Location: White City,
SK
Cobra Make, Engine: West Coast, 460 CID
Posts: 2,915
|
|
Not Ranked
Quote:
Originally Posted by 169mph
Sorry guys I’m not expert. In fact I had no idea what bolt pitch meant until a couple of weeks go. Yes, i meant 1.5 vs 2.0. I’m worried about retap differential. I could that going bad for a number of reasons. After reading a little more about bolt pitch I feel like the 1.5 would be preferable but the the 12.9 14mm 2.00 bolt would work fine. I think I’m talking myself into going with the 12.9. 14mm 2.00 bolt. I haven’t driven the car in over a month. Is this a mistake ands it’s going to bite me done the road? I appreciate the feed back. Thanks, Mike
|
If the differential is tapped M14 x 2.00, the only way to tap it to 1.50 mm pitch is to go larger (e.g. M16 x 1.50). As noted by Dominik, the 2.00 mm pitch has a smaller thread root diameter than the 1.50 mm, so you'd end up with partial threads that wouldn't hold. You'd have to go larger in order to have enough metal for the threads to hold.
You should probably stick with the M14 x 2.0 but, as eschaider wrote, find a bolt with a longer shank. I had to do that last year with a smaller bolt, and ended up buying a longer bolt to get the proper shank length, then cutting off the excess threads to get the length I needed. Not the easy route, but the proper way to do it.
__________________
Brian
|

03-30-2022, 10:06 AM
|
 |
CC Member
|
|
|
Join Date: Feb 2014
Location: White City,
SK
Cobra Make, Engine: West Coast, 460 CID
Posts: 2,915
|
|
Not Ranked
Quote:
Originally Posted by spdbrake
|
Yes, that's an excellent alternative. Helicoil or similar inserts are often stronger than equivalent threading - particularly in aluminum. Galling due to dissimilar metals is also eliminated. I've used Recoil inserts, though none that large.
I will note the M14x1.5 bolt supplied in the kit is almost fully-threaded, however, so perhaps not the best fastener for the application.
__________________
Brian
|

03-30-2022, 10:46 AM
|
CC Member
|
|
|
Join Date: Dec 2015
Posts: 1,442
|
|
Not Ranked
Good point Brian. Regardless the weak point on a all-thread and partial thread still will be the threads as they are exposed at the diff bolt hole entry point.
Another alternative is: Since the bolt hole on the Diff is a through and through a nut and washer can be placed on the back side.
Chase the hole to allow a 14mm bolt to be a slip fit.
Sold here in 14x1.5 and 14X2.0 (the 220mm is 8.6" long for example, plenty long enough)
https://belmetric.com/m14x1-5-fine-d...H14X1.5X220YLW
Have to measure what you need once the diff is remounted.
|

03-30-2022, 12:28 PM
|
 |
CC Member
|
|
|
Join Date: Nov 2009
Location: Edmond,
Ok
Cobra Make, Engine: Classic Roadsters
Posts: 628
|
|
Not Ranked
The black nitride is a thermal process that does increase bolt strength and resistance to fatigue.
The cadmium is just an electroplating.
The bolt that failed was maybe not up to specs.
Run the bolts that fit and check them after use, along with your other suspension bolts.
__________________
 Chaney Shores Studio
Last edited by sunman; 03-30-2022 at 01:00 PM..
|

03-31-2022, 05:51 AM
|
 |
CC Member
|
|
|
Join Date: Sep 2002
Cobra Make, Engine: SPF#0760
Posts: 3,406
|
|
Not Ranked
Aircraft Spruce is an excellent source for extremely high quality and specific requirement bolts, etc. such as specific bolt shank “grip” lengths.
Blas
__________________
Wiring Diagrams: SPF MKII, MKIII, GT40, CSX7000, CSX8000, Corvette Grand Sport, and Shelby Sebring, Bondurant & Cinema Tribute Cars.
Owner’s Manuals: SPF MKII, CSX7000, CSX8000, Sebring, Bondurant, Cinema Tribute Cars $ GT40’s..
Large, easy to read and trace schematics with part numbers, wire colors, wire gauge, fuses, and electrical upgrade information. Trouble-shooting and replacement part numbers for those roadside repair adventures.
SPFWiringDiagrams@Comcast.net
Last edited by Blas; 03-31-2022 at 05:56 AM..
|

03-31-2022, 06:52 AM
|
CC Member
|
|
|
Join Date: Dec 2015
Posts: 1,442
|
|
Not Ranked
Quote:
Originally Posted by sunman
The black nitride is a thermal process that does increase bolt strength and resistance to fatigue.
The cadmium is just an electroplating.
The bolt that failed was maybe not up to specs.
Run the bolts that fit and check them after use, along with your other suspension bolts.
|
The Black Oxide coating you see on hardware including ARP is a cheap quick corrosion resistance coating and does nothing for the strength of the hardware. Not as durable as Cad or Zinc plating.
Nitriding does give a hard durable finish (a few thousandths of and inch) to the item for wear properties. Typically used on Cylinder walls of Hyd actuators and engines, crank journals, axles, bolt and slide areas of
weapons.
|

03-31-2022, 07:14 AM
|
 |
CC Member
|
|
|
Join Date: Nov 2009
Location: Edmond,
Ok
Cobra Make, Engine: Classic Roadsters
Posts: 628
|
|
Not Ranked
Good point on no strength increase, hot plating just more durable finish.
Your broken plated bolt looks inferior judging by the knurling.
Cadmium plating doesn’t do good in a fatigue cycle situation.
See if you just have a bad bolt first, upgrade while replacing them.
I try to use stainless when I can and zinc, which does better in high stress, for hardened nuts and bolts.
__________________
 Chaney Shores Studio
Last edited by sunman; 03-31-2022 at 08:50 AM..
|

03-31-2022, 11:52 PM
|
CC Member
|
|
|
Join Date: Sep 2020
Posts: 84
|
|
Not Ranked
I appreciate all replies. I have another issue that’s making me hit the reset button. I was trying set my differential on a transmission lift and long story short I dropped the differential. It landed on the differential cover bushing hole. Not sure what you call it but it cracked. The differential moves freely with no obvious signs of damage. At a minimum I need a new differential cover. I would love a good excuse to replace the E36 with something that I dont have to worry about a $10 bolt shearing every time I go for a cruise or it limits how hard I drive my car. Just a little frustrated. Thanks again for the responses.
Last edited by 169mph; 03-31-2022 at 11:57 PM..
Reason: Grammar
|

04-01-2022, 09:54 AM
|
 |
CC Member
|
|
|
Join Date: Feb 2006
Location: Gilroy,
CA
Cobra Make, Engine: SPF 2291, Whipple Blown & Injected 4V ModMotor
Posts: 2,738
|
|
Not Ranked
Use one of the Ford 8.8" aluminum IRS center sections out of an Explorer or a T-Bird, an 03/04 SVT Cobra or a MK VIII. Have your local fab shop build the bracketry to mount it. The one on the left is the Explorer and the one on the right is the T-Bird / SVT Cobra / MK VII unit. The Explorer is beefier in the front mount area.
Ford no longer makes the nice FRPP HD cover for their 8.8" IRS that looks like this;
Although they can be found used, you can also have a nice billet piece like this made;
The 8.8 IRS is extremely strong, light, small and fits in our chassis nicely. They have gear sets from 2.73 up to 5.71 available in both the aftermarket and OEM channels. The rear end has been used by various replica manufacturers over the years and provides very good service life. Parts are readily available and reasonably priced in large part because of the widespread adoption.
Almost forgot, here is a pic of the OEM Explorer rear cover. It is also quite robust.
__________________
Help them do what they would have done if they had known what they could do.
Last edited by eschaider; 04-01-2022 at 07:16 PM..
Reason: Fixed broken pic links
|

04-01-2022, 06:37 PM
|
 |
CC Member
|
|
|
Join Date: Feb 2014
Location: White City,
SK
Cobra Make, Engine: West Coast, 460 CID
Posts: 2,915
|
|
Not Ranked
Quote:
Originally Posted by 169mph
I appreciate all replies. I have another issue that’s making me hit the reset button. I was trying set my differential on a transmission lift and long story short I dropped the differential. It landed on the differential cover bushing hole. Not sure what you call it but it cracked. The differential moves freely with no obvious signs of damage. At a minimum I need a new differential cover. I would love a good excuse to replace the E36 with something that I dont have to worry about a $10 bolt shearing every time I go for a cruise or it limits how hard I drive my car. Just a little frustrated. Thanks again for the responses.
|
If that case is aluminum can you not get it welded and machined?
__________________
Brian
|

04-02-2022, 08:59 AM
|
CC Member
|
|
|
Join Date: Sep 2020
Posts: 84
|
|
Not Ranked
I ordered a new cover for now but I’m still exploring other options. What do y’all think I can get for my e36 rear differential? I know this is a very difficult question to answer but What should I expect to pay to have a shop do the fabrication and install one the options Eschadier was cool enough to post? I saw the new RT4 rear differential on Iconics website. Does that differential mount to the carrier / subframe the same way as the E36…single bolt to carrier?
Thanks
|

04-02-2022, 10:49 AM
|
CC Member
|
|
|
Join Date: Oct 2020
Location: New Haven,
ct
Cobra Make, Engine: Factory Five
Posts: 26
|
|
Not Ranked
new poster here but I have been a mechanic all my life and I am over 70 years old. The most common reason for a bolt to fail like yours is it was over tightened. This is especially true on suspensions parts many give it a little extra. Before you redesign and sped lots of money just put it together carefully making sure the torque is right and it does not bottom in the threads. It is my understanding that these were modified by drilling and retapping which would be another reason it might have been over torqued. respectfully
|
Posting Rules
|
You may not post new threads
You may not post replies
You may not post attachments
You may not edit your posts
HTML code is Off
|
|
|
All times are GMT -7. The time now is 03:23 AM.
Links monetized by VigLink
|