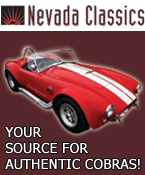 
Main Menu
|
Nevada Classics
|
Advertise at CC
|
S |
M |
T |
W |
T |
F |
S |
1 |
2 |
3 |
4 |
5 |
6 |
7 |
8 |
9 |
10 |
11 |
12 |
13 |
14 |
15 |
16 |
17 |
18 |
19 |
20 |
21 |
22 |
23 |
24 |
25 |
26 |
27 |
28 |
29 |
30 |
31 |
|
|
|
|
|
CC Advertisers
|
|
41Likes

11-28-2020, 06:27 PM
|
 |
Senior CC Premier Member
|
|
|
Join Date: Nov 2015
Location: Bellevue,
WA
Cobra Make, Engine: Everett-Morrison 514, Toploader 4 sp, Jag IRS
Posts: 278
|
|
Not Ranked
Trailer Project
Serpent Express Retro Kit (1 of 3 posts)
Goals included:
● Small size o Fit the side yard Serpent Den created for it
● Low height o Sit at or below fence line
o Fit in garage
● Lightweight, sturdy flatbed o Capable of long trips safely
● Quality top installation o Maximize weather seal (given top style)
o Smooth/flat vinyl fit
Trailer Base & Serpent Express Top
I bought a flatbed car hauler to install a Serpent Express Retro Kit on top. Larry Johnson of Serpent Express was a ‘champ’ to work with! He fielded many questions, provided a customized kit with diagrams and perspective. He was very responsive throughout.
The flatbed is a 2016 16’ Aluma aluminum trailer with extruded aluminum floor, 2 - 3,500 lb. rubber torsion axles, electric brakes, breakaway kit, reinforced A-framed aluminum tongue, fold down rear stabilizer jacks, and pull out 6’ ramps.
Prep was needed to fit the Serpent top. The front corners were 45 degrees with a deck rail. To use the full 16’ for the top, the corners were filled in. A welder scavenged the deck rail to create corner frames and filled with flat aluminum. He also welded in a battery holder and winch mounting frame.
Starting Aluma flatbed trailer
Measured the deck, Cobra, and garage height. Got the dual rib frame for stability and extra doors (5 total) for easy access. Larry provided custom CAD drawings, frame cut sheets, frame & deck fitting plans, and detailed instructions with photos, all customized. He lowered the peak & rear frame heights for my specific max height.
I used weld-on aluminum upright deck fittings. Bought 1.75” OD / 1.25” ID 6061 bare aluminum tube. The welder cut 10 each 6” fittings, welding them perpendicular, located per the deck plan. They’re inset from the frame edge to allow 3/4” wide foam tape to run outside.
After welding, cleaned trailer before adding the top. Wand wash employees were testing a new pressure washer Suds Cannon. I asked how much to do my trailer…$5. They did a great job, I gave them $10, all were happy.
Suds canon
Removed manufacturer and dealer stickers and polished the outer deck frame and fenders, for a unique and clean look.
Before polishing
Polished with Blue Magic polishing cream, blue paper towels, and ample elbow grease.
After polishing
Restored rusted fender hold down bolts. Cut and added rubber fender mount gaskets to avoid metal-to-metal scuffing.
Fender bolts and rubber gaskets
Frame Structure
Assembled the frame structure. Got 10’ lengths of 1” EMT steel conduit from HD. Measured and cut lengths per cut sheet, marking for reference. Tried a miter box and hacksaw, assessed situation after one cut, bought a cut-off saw.
Got a 3.5 HP cut-off saw at HF, handled the task well, quite enjoyable. Neighbors confirmed I’m crazy, in the backyard after dark, shooting sparks across the yard. That was my cutting station, dutifully carried downstairs and out back nightly after work, generally raining, with a full complement of cords, lighting, safety equipment, leveling boards, etc. Then let the sparks fly.
Prepped cut ends with deburring tool, files, and steel wool. As overkill, I cleaned and coated each cut end with metal primer and Rust-Oleum to protect from corrosion.
Cutting, tools, coated ends, markings
Loose assembled the frame, front to back, with cut conduit sections & the kit’s connectors. Went together well, challenging getting the rear cross pieces in with the rest of the frame in place, with hard limits, like a Rubik’s cube.
Solution was family lifting rear frame off deck fittings to widen out at the connectors, w/o any piece exiting its connector and crashing down. Trust me, ‘crash’ is the correct term there. Idiot proofed (against myself) by tightening the connector set bolts most likely to crash outside of hand control. Success.
The 2nd iteration of that process actually did it. The 1st identified cross pieces requiring trimming to fit. Larry’s cut sheet wasn’t off, I’d assessed excess free room in each connector and added length to each piece for max extension if needed (mainly for uprights), made a couple too long initially.
The connector set-bolts were kept loose to allow flexibility when later fitting the top, at minimum extension, then tensioned from there.
Frame assembly
Pipe Insulation
Pipe insulation was added to protect the vinyl top, particularly at corners. Measured and created a cut sheet for tube counts bought at HD. Opted to insulate the entire frame for a smooth surface & transitions.
Planned the insulation layout to ensure smooth corners, junctions and transitions. Cut to avoid junctions on connector pieces. Taped around each connector and at each cut end junction. Carefully trimmed each piece, particularly around corners.
Per Larry, used 3M Metalized Flexible Duct Tape 3350 UL181B-FX. Designed for flexible HVAC ducting, with wide heat range, durability, workability, and strong bond. Pulls off easily w/o disfiguring to rework rotations for overlap alignment. 3 tape rotations on each. Result is a clean look, full adhesion, hopefully long lasting.
Pipe insulation and 3M taping
Fitting Top
Prepped for fitting/fastening the vinyl top. Goals were a good weather seal, a clean outer frame edge, and a smooth top.
Weather seal is by self-adhesive foam tape around the deck frame just outside the upright fittings. Measured upright placement tight for the ¾” wide foam tape. Foam tape spec is ½” thick, I opted for lower-compression, higher density foam, at 7/16” thick, which seemed durable for that environment.
The top has side pouches sewn in the lower edge. Cut ½” EMT steel conduit ‘base bars’ and slid into those pouches. These set on the foam with inboard conduit clamps (via inside razor cuts) snapped over the conduit and bolted to the deck frame, creating a press down weather seal.
The side base bars are inserted into rear side openings. The front base bars are inserted via inboard razor slits made near the front corners, with the front flipped up for insertion from outside the trailer, then flipped back down.
Decided to cut base bar ends at front corners at angles where front and side bars met. The front and side pouches each ended at a 45 degree corner seam. The angle cut bars maximized filling that space for corner support and weather seal.
Welded the upright fittings tight to ¾” from edge allowing the outer weld beads to breach into that outer space a bit. Dremel ground a small amount off the outer beads allowing foam tape to lay straight and flat next to each upright.
Flex-Seal taped a couple spots under the foam tape to equalize surface levels, for a good weather seal. This was due to slight variation where the front corners were built. Then installed the foam tape.
Grinding
Flex Seal for low spots
Foam tape
Initially set the base bars on the foam tape to mock-up the clamp location and accurately mark the holes for drilling. Instructions had clamp separation at 18” max., 12” for a stronger build, I used 9”. Used narrower spacing at the corners, base bar junctions, and ends, per instructions. Mocked-up pouch thickness and shape with paper sheets to align base bars passing by uprights, for accurate marking.
Used extending magnets a) below deck to locate the center point of the crossway channels, by feel, and b) above deck to match that location above for drilling. This allowed for marking by myself, with some Gumby stretching.
Base bar measuring & top frame drilling

Last edited by EM-0785; 11-28-2020 at 09:39 PM..
Reason: Spelling
|

11-28-2020, 06:32 PM
|
 |
Senior CC Premier Member
|
|
|
Join Date: Nov 2015
Location: Bellevue,
WA
Cobra Make, Engine: Everett-Morrison 514, Toploader 4 sp, Jag IRS
Posts: 278
|
|
Not Ranked
Trailer Project
Serpent Express Retro Kit (2 of 3 posts)
Vinyl Top
Initial sneak peak of the top in its box, looking good! Laid out the top on the deck to acclimate with garage temp turned up. Set top over loosened frame for continued acclimation. Corners and peaks settled into place nicely.
Top in box
Top laid out
Top on frame loose
Fastening Top
My Aluma had 3 fastening typical scenarios, front, front corners, and sides. Front being most challenging.
The front frame is 2” x 5” aluminum requiring longer drill bits. Has a center channel underneath, with ½” wide channel access exposing the true bottom an inch up into the channel. Also reinforced with internal structure, so drilling was more difficult.
It was critical to drop the bolts centered in the channel to get washers and nuts on w/o cutting the ½” channels open. By aligning foam tape to the outer frame edge, that was a hard reference point, dictating the base bar and clamp, and therefore clamp hole, locations. I centered the base bars on the foam, snapped the clamps on, and marked the holes where they naturally fell.
Fortunately, after drilling those front holes, they dropped through ‘dead center’ into the narrow channels below, allowing me to (barely) fasten them. It took fingertips, taping washers in place, and several tries to thread the nuts.
It took various wrenches to manage inside the channels, and taped wrenches until I got in place with both upper and lower wrenches, and various extenders, but managed all myself. A sense of accomplishment on those front bolts.
Front channel and holes
The front corners just required specific length hardware, yet were easily accessible.
Front corner holes
The sides were middle of the road challenging, and there were a lot of them. I computed hitting centers on the variable-width underside structural cross channels, by using 9’ hole spacing. Centering those maximized the tight fingertip access and allowed for large washers.
I set weight on the bolt heads to get 1-2 threads to protrude below to start the nuts, and avoid popping-up when barely touched. Taped washers on (using a guided missile type blind thrust with one fingertip, many tries on the most challenging locations) and the threaded nuts blind with fingertips. Tightening allowed more threads to pull down as the foam compressed.
Side holes
Used a roto-hammer in drill mode worked well, especially on the more challenging fronts with long bits. Used blue tape for marking on and keeping bits from traveling. Did 5-6 steps from small pilot bit up to final hole bit for the ¼” deck bolts. This kept the bits under control and achieved accurate holes/locations.
Started with big box store Cobalt bits and cutting oil, wasn’t doing the job and breaking smaller bits. Got fastener specialty store Cobalt M-35 steel bits and Boelube Paste, a Boeing developed drilling & cutting lubricant. That setup worked very well, no more broken bits, lubricant paste stayed on bit no mess and superb drilling effectiveness.
Roto-hammer, Boeing lube and instructions
Larry included extra clamps in the kit, for 50 total. I used all 50 given my spacing used. The top’s 5 access doors allowed doing all but a handful of the fasteners by myself. A lot of twisting and stretching, fit by feel, various extensions, seemingly always upside down, but it all worked.
Base bar clamps loose
Base bar clamps fastened
Base bars fastened – outer corners
Base bars fastened – outer sides
All hardware was stainless from McMaster-Carr. Was very happy with their stainless flanged nylocs with black nylon. I found a group of tools that managed the deck fastening pretty well, per photo.
Hardware & tools
Fastening Frame
With the base bars fastened down, it came time to drill, place, and fasten the bolts in the welded deck uprights. These go through both the fitting tubes and inserted conduit frame uprights, to hold the frame securely in place. There is a small amount of play by design.
One decision was whether to drill before or after the top was tensioned. If after tensioning it seems they would take their natural shape and have less fastened tension (maybe good with aluminum fittings). However, doing them first would make managing the remaining frame easier and more stable. After much back and forth, the answer presented itself.
I could tell I was going to need to use some extension all around to tighten/smooth the vinyl top. So, I did those deck fitting bolts first, pressing each upright to its outermost play position in the fitting while drilling (the corners pressed out at 45 degrees). This was done with a kneel pad and my head, both hands on the roto-hammer.
The 4 corner upright bolts are spec’d carriage bolts with smooth rounded heads to avoid damaging the top. Those ideally require squared holes. I used a Dremel and mini files to square out the corner fitting holes.
Corner round hole
Corner square hole
Dremel & mini-files
Bolted - corner
Bolted - non-corner
Initially I tensioned the upper frame slightly front to back, tightening connectors as I went. Not so tight as to over stretch it. Just to smooth it out some, I will retension the top after some trips with vibration and weather cycles. I’d left the top in its box for months before starting, so there were some fold lines. Many came out during acclimation and initial tensioning. The rest will work out with use and retensioning.
Top initially tensioned
Rear Door
I put a lot of thought into the rear door hold down. The standard spec is to drill holes in the side frame for the rear base bar to protrude through with trailer clips on the outsides. That works pretty well. However, it seemed to be a single fixed position that could be under/over tension depending on the fitting height or if the top stretches. The ones I’ve seen were almost over-tensioned, and tended to expand the holes in an aluminum trailer frame due to wear over time. Also, releasing the rear door can be a two person job at times, particularly if the bar sticks in the pouch, and puts added movement in the top and of the base bar in the pouch which all can tend to wear more over time. Granted, with a fixed position base bar, one can always re-tension at the upper rear frame, yet I was looking for a more real time flexible door fastening solution.
My goals included no side-to-side material movement to open, and an easy, one person, variable tension fastening method. Stainless steel Terry Body hold down springs & hooks were used to hold the rear door down with a firm and flexible tension approach in basically a straight down hold fastening solution. I used a shop for winch mounting and rear door fastening solution. They came up with this rear door solution without hesitation as I was explaining the goals!
As opposed to the ½” hollow conduit (which is a bit over 11/16” OD) as typically spec’d, I first planned to use a ½” solid aluminum round bar in a 6061-T6-cold finish which has 0.50” OD. However, as the shop recommended, we used flat aluminum stock with dimensions 1-¾” wide x ⅛” thick. That used more of the tall rear pouch for added rigidity. It was thinner, so dropped the bar/pouch perfectly into the rear channel in my trailer design without being tight and scuffing/wearing the vinyl pouch.
My Serpent door was specifically designed to extend a bit past the deck to drop into that channel given my trailer’s design. This all worked to create a pretty good natural weather seal for the rear door. Also, the mounts used for the tension fasteners bolt through the flat bar putting the downward force on the bar. The ends of the bar don’t extend past the pouch so it has a clean appearance, plus the bar won’t slide out with the through bolting.
My goals for opening and holding up the rear door were a simple, competent means that’s easily workable by one person. Again, the shop came up with an elegant solution. It was achieved using 24 lb neodymium magnets and nylon straps on each side. One magnet is attached to the upper inside frame with a nylon strap attached to it and another magnet attached to the loose end of the strap. The door is rolled up and the straps wrapped around with the loose end magnet attaching to the fixed frame magnet, magnetically clamping through the vinyl top. It holds firmly and is simple to manage in seconds by one person.
The rear access holes in the side base pouches, and the hollow side base bar ends seemed exposed to weather and grime. I installed metal conduit caps to protect those. That left small pouch openings above the base bar. I may fill with a clear sealant, maybe Flex Seal. I’m not going to worry about it on the rear door base bar pouch. There is a slight open area at the rear corners below the end of the door zipper. I’ll monitor that and either not worry about it or may cut some foam or such to insert on the inside to block when the rear door closes for a complete weather seal.
Rear door - flat bar hold down with tensioners
Rear magnetic door holder straps

Last edited by EM-0785; 12-08-2020 at 09:02 PM..
Reason: Remove word
|

11-28-2020, 06:37 PM
|
 |
Senior CC Premier Member
|
|
|
Join Date: Nov 2015
Location: Bellevue,
WA
Cobra Make, Engine: Everett-Morrison 514, Toploader 4 sp, Jag IRS
Posts: 278
|
|
Not Ranked
Trailer Project
Serpent Express Retro Kit (3 of 3 posts)
Tie Downs
Goals here included over-capacity strength and quick ease of use. I mulled over several approaches to tie downs. Wheel nets were not as accessible given my trailer. E-tracks to suspension arms were a concern over strength given side angles and intermittent welded solution being considered.
In the end, I went with the trailer’s 4 existing swivel floor mount flush tie down ring wells that correspond nicely to the new tie-down rings welded on the front of the Cobra and given the rear suspension. They ended up being fairly ideally placed for my car. Some additional structure was added to the front of my car to both support adding an anti-roll bar and attaching tie-down rings in easy reach.
The existing swivels provide similar strength regardless of horizontal clock orientation. The front Cobra welded rings are further forward than the suspension arms we’d otherwise considered reaching to strap around, so very quick to clip to.
This solution requires short straps, all 4 easily accessible from my trailer doors with a quick easy reach to simply clip the hook on the welded front tabs and an easy loop around the rear inner half shafts. Granted this does bind down the suspension, but for the limited time usage in the end that was acceptable to me.
I bought some 6061-T6 aluminum E-tracks from Mac’s that I’d planned to have tig welded to the deck, but opted for the above solution instead. After some trailer usage, I’ll determine if there are areas for gear that it would be helpful to have some e-track welded on for, I prefer to minimize bolts/holes through the deck.
My friend Larry, who built a Serpent for his Cobra, gave me a gift of custom heavy duty straps he and his friend Scott had designed for his Serpent setup. That was a real honor, and I will always use these straps in honor of my friend Larry! They offer e-track capability as well, by design, if using a trailer with e-tracks.
Car strapped down
Winch
Welded two hollow aluminum winch mounting bases to the front of the deck. These served to raise the winch to reduce the chance of the rear deck interfering with the cable, and as a base to achieve mounting of the winch plate and winch, while hiding wiring connections underneath.
Replaced the new winches’ metal cable with a nylon cable for ease of use, smaller winding, and softness in the event it rubs on anything.
Due to pull angles for loading, the car will be towed (winch cable attached) through the grille. This is achieved with two hidden tow rings inside the mouth of the Cobra that a cross strap attaches to for a winch attachment point in the center of the grille.
Winch mounted (with nylon cable & wireless remote added)
Inside Lighting
Installed 4 ea long swivel dual-tube LED light fixtures with a switch accessed inside the front right door near the battery. These are oriented front to back at each corner. Due to the angled down shape of the top/frame, each is angled to project light in toward the center of the trailer. This provides ample lighting throughout the trailer and coming above from all directions to help avoid dead zones.
Tow Rig
Bought an eight year old 2011 Ram 1500 Big Horn with 8K miles in like new condition. It came with a SnugFit canopy. The prior owner towed it behind their RV to have a vehicle when they took trips. I added a Tekonsha P3 brake controller.
Hitch & Scale
Went with a Convert-A-Ball 10,000 lb shock absorbing cushioned ball mount with a 6” drop. Added a Weight Safe hitch ball with built in scale for dialing in tongue weight. Bought these from etrailer.com.
Side Yard – Serpent Den
One major thing I had to do was create a place to keep the trailer. While we designed the trailer to fit in my garage, I still intend to store it outside most of the time. My side yard is just barely big enough for the trailer and was overgrown. I cleared that out and lowered the pad by a foot of soil to level it out. Added a new fence and ⅝ minus crushed rock pad with heavy duty landscape paper. Added a short chain link fence on the back end to keep our little dogs in the backyard.
A main goal was a sturdy gate that would not sag over time like so many around here. I spec’s a heavy duty or commercial style hinge for overkill. The fence company delivered and used an aluminum frame for the gates as well. Also maximized the fence height to keep the trailer from being seen over the fence.
Extended the crushed rock out to the street, with landscape timber borders. Replaced the water main with a flexible one (we’d last done copper many years ago) and dug it deeper this time. Re-routed the sprinklers in that area. Moved the two sprinkler boxes to align with the water meter box and get more out of the way of the tire paths. Replaces boxes with stronger, drive over versions.
Serpent Den development
Serpent Den in use
Trailer Cover
Due to the unusual shape of the Serpent trailer, I toyed with the thought of a custom cover, or using tarps and just wrapping the excess on the short height end.
Yet I found an ADCO Tyvek All-Climate + Wind RV Cover for Pop-Up Camper up to 16’ Long on etrailer.com in gray. It had almost the same dimensions as my Serpent except some expected excess in the front that I’d bungee down. I liked the all weather capabilities, with material that breathes with moisture and protects against the sun.
Ends up it fit almost perfectly in the front, and the rear fit was nice and tight just a few inches short in back (as expected). It fit better even than expected, so I’m pleased with it.
Logo Decals
I hadn’t planned to place any logos on the trailer. However, given Larry’s superb assistance and support of our hobby with the Serpent Express small business, I still may proudly display the Serpent Express logos once the top is fully smoothed out after some use. That could also increase visibility to other drivers.
Summary
That, Cobra aficionados, is how I built my Serpent trailer. Perhaps soon to be a long-lost art as they now offer a hardtop enclosed version in the same shape, without all the work! However, I am very comfortable with the sturdy base flatbed I used that should meet any of my trip plans/needs. This will remain a very satisfying mechanical endeavor for me, right to my limits!
See you on down the road...
Last edited by EM-0785; 07-05-2021 at 11:26 PM..
Reason: Add photo, correct spelling
|

04-20-2021, 11:47 PM
|
 |
Senior CC Premier Member
|
|
|
Join Date: Nov 2015
Location: Bellevue,
WA
Cobra Make, Engine: Everett-Morrison 514, Toploader 4 sp, Jag IRS
Posts: 278
|
|
Not Ranked
Just a report on the newly added front trunk area for the dogs….
The photo is the end result with the dogs now being very comfortable and willing riding with us in the Cobra.
The video linked below reflects the ‘training days’ to get them acclimated to the Cobra. It’s a regular routine now, which they look forward to (well, demand) on the minute nightly. The mere mention of the Cobra gets them excited. Note that I notched some foam dog stairs for the side pipes to facilitate this training!
https://youtu.be/d1Ey4syyJFY
Lastly, now when I open the drawer for my leather Cobra key ring, and they get a whiff of it, they begin siren-like hound dog howling and run to the garage door.
So far, so good…it’s working well. Brent
|

01-20-2022, 10:40 PM
|
 |
Senior CC Premier Member
|
|
|
Join Date: Nov 2015
Location: Bellevue,
WA
Cobra Make, Engine: Everett-Morrison 514, Toploader 4 sp, Jag IRS
Posts: 278
|
|
Not Ranked
Oil Cooler Installation
Goals included:
- Significantly reduce engine oil temperatures and sustain
- Achieve desired cooler size via extra width vs height
- Limit height to not interfere with tow hoop solution
- Maintain distinct use for each of radiator and oil cooler openings
- Maximize use of oil cooler opening
- No visible mounting hardware (rivets, bolts, etc.)
- Minimize front visible line routing (direct back, not looping up/around)
- All black lines/hardware with overall black/silver theme
- Finished look for nose of car
During my prior radiator/cooling system project, including Evans Waterless conversion, I’d planned to next monitor oil temperatures and consider adding an oil cooler if necessary. I determined it necessary and have now completed the oil cooler project as documented here.
Nose before oil cooler
Nose after oil cooler
After much research I selected a Setrab product solution. That included a ProLine stacked-plate style oil cooler with fins and conversion to a remote oil filter setup using a block oil filter take off plate and a thermostatic oil filter remote stand. Also used their high flow, cleanable engine oil filter, plus various applicable fittings and hoses.
Oil Cooler (Setrab image - not my specific size)
Block oil filter take-off plate (Sertab image)
Thermostatic oil filter remote stand (Setrab image)
High flow, cleanable engine oil filter
Filter blow-up (Setrab image)
Filter (Setrab image)
The thermostatic remote stand combines the functions of a traditional remote filter head and a standalone oil thermostat to control oil flow, keeping parts and plumbing connections to a minimum. The 180-degree thermostat limits flow to the cooler to a minimum below that. The integrated thermostatic oil valve controls oil flow to oil cooler downstream.
Fittings and hoses are all AN -10 black aramid to match those throughout the engine bay. The Setrab remote stand and take off plate are machined from billet aluminum and anodized in titanium gunmetal gray for durability. The oil filter is engineered to balance performance and flow, including for street vehicles.
Thermostatic remote stand installed
I went with a shorter, wider cooler than many 427 cars, so stylistically a bit more like the lower, wider 289 competition Cobra coolers. That minimized blocking air flow to the radiator and filled the oil cooler opening for air flow coverage through it. It resulted in distinct functionality and appearance within each respective front-end opening (radiator and oil cooler). The wider cooler also placed the hoses in a less obtrusive visual location and shortened the turns and runs back into the engine bay, both to my preference.
A taller, narrower cooler of this type does reduce flow restriction compared to a wider/shorter cooler of the same capacity. However, my assessment is that the wider, shorter cooler of the same capacity meets/exceeds the primary requirements of adequate flow/cooling/pressure, while achieving the additional benefits of distinct functional openings and my visual preference. The flow and pressure are well within range for my engine usage needs. It seems to be working well so far.
Planning the cooler installation began with designing the front cooler mount with fabricated structure welded in to fit the space. One goal was a clean look with no fasteners (rivets, bolts) visible from the front. After some minor trimming the cooler fit the opening very well. Support bracing was added to the cooler side plates. Filler plates were fabricated next to the oil cooler, on either side, to route air toward the radiator and fill in the visually empty space next to cooler.
A top cooler plate was fabricated to remain at or below the level of the cooler space and radiator, to minimize impeding air flow to the radiator. The rear most edge of the plate is curved downward to allow airflow to the bottom of the radiator fins. Fabricated pieces were powder coated black before final re-assembly.
Remote stand & fuel line welded mounts
Planning the plumbing installation included fabricating a remote oil filter stand mounting bracket, welded to the frame. The thermostatic remote oil filter stand attached to that bracket, and the oil filter is spun onto that. It was located for road protection and ease of maintenance and simple, elegant line routing. The lines coming out of the oil cooler are highly visible so it was important to make them as equivalent as possible on each side.
While the cooler, fabricated plates, and lines were black, the radiator was left silver which allows the fittings and lines to retain a visual impact against that backdrop. It also carries a silver metallic feel from the engine bay for a balanced blend of silver and black in the nose of the car as well. The look is now finished, yet still mechanical and raw. The overall installation was low profile enough to avoid interference with the function of the tow hoops previously installed approximately center height inside the radiator nose opening.
Nose after installation
Plumbing routing from nose (below tow hoops)
Congestion of existing parts in the area near the lower steering shaft and block take-off plate warranted routing the lines around behind and through the driver side wheel well structure. The lines are tucked tight up underneath and mounted with proper isolating mounts.
The filter is a cleanable, ‘permanent’ type filter, with a surgical-grade stainless-steel mesh media filter element that captures all particulates above 30 microns (absolute filtration rating). It’s designed for high flow and low pressure drop, given a relatively low filtration size. Its rare-earth magnet captures ferrous particles. The physical size is small, yet I service my filters very regularly. For my usage, and maintenance routine, this should provide a good balance of flow and filtration.
AN-10 hoses were made to run from the engine to the filter and from the filter to the cooler.
This included rerouting the fuel line to the fuel filter. That provided the opportunity to eliminate the zip tie that previously temporarily held the fuel hose in place as it was routed across the front of the engine bay. The new oil filter mount took this into consideration and incorporates a rubber cushioned support to constrain and support the fuel hose. That’s now a permanent, functional solution that also looks better.
The system was tested, running through its first heat cycle then changed the oil and cleaned the filter. There was no apparent residue from the recent work trapped in the filter or housing. The engine oil capacity is now 5.75 quarts (up from 5 quarts) with a typical oil change and filter cleanout.
In testing, the engine was run until the oil bypass opened and with it just sitting in the shop the heat exchanger outlet temperature averaged 15 degrees cooler than the inlet and held a consistent temperature. That seemed significant given that performance would be even better with positive pressure air moving across the heat exchanger plates and fins.
In initial drive testing on a 45 degree day for 45 minutes with several four gear runs for some carb tuning, the air and water temps remained nearly matching each other, consistently, ranging between 180-190. Previously oil temps would just continue to consistently climb to 245+, even at a similar cool outside air temperature.
Granted, we also dialed in carb tuning, timing, the pcv system, etc., yet the oil cooler was the main component necessary for gaining control of the oil temperature (with significant reduction), particularly in conjunction with my Evans waterless coolant, which did seem to raise combustion chamber temperatures in my application.
The oil cooler project is very functional (the main goal) and helps finish off the look of the front of the car. Thanks to my shop friends at Rule Garage for their design, fabrication and installation, all in line with and achieving my standards and goals for this project.
Overall car after oil cooler
I’ll add some photos soon of the fabricated oil cooler mounting structure underneath.
Brent
Last edited by EM-0785; 12-02-2022 at 04:23 AM..
Reason: Removed unnecessary sentence
|

01-21-2022, 12:31 AM
|
 |
CC Member
|
|
|
Join Date: Aug 2009
Location: Adelaide,
SA
Cobra Make, Engine: AP 289FIA 'English' spec.
Posts: 13,151
|
|
Not Ranked
Wow, Brent....that's really impressive!
It's also the 5 longest posts I think I've ever seen. Great job!
What's next?
Cheers,
Glen
|

01-21-2022, 01:15 AM
|
 |
Senior CC Premier Member
|
|
|
Join Date: Nov 2015
Location: Bellevue,
WA
Cobra Make, Engine: Everett-Morrison 514, Toploader 4 sp, Jag IRS
Posts: 278
|
|
Not Ranked
Quote:
Originally Posted by xb-60
Wow, Brent....that's really impressive!
It's also the 5 longest posts I think I've ever seen. Great job!
What's next?
Cheers,
Glen
|
Thanks Glen, next up is a recently completed dual flow adjustable M/E Wagner PCV valve upgrade, followed by a larger pending exhaust upgrade. Exhaust parts on order, work likely won't be started for a few months though. A minor twist I'm looking forward to as well in that project, you'll have to wait to see!
Brent
|

01-22-2022, 01:14 AM
|
 |
CC Member/Contributor
|
|
|
Join Date: Sep 2016
Location: (Beautiful) Sequim,
WA
Cobra Make, Engine: Pacific Roadster, 347 cu.in. 5-speed
Posts: 2,001
|
|
Not Ranked
@xb-60 , Glen I swear you & Brent are two peas in a pod  If anything is be done on your Cobras, it will be done to 10th degree. I believe neither of you know the Term 'Half-ass'  Brent, soon we'll be on the road tearing up the PNW roads with our "Twin Cobras" Who would have guessed we'd end up with the same paint schemes (Karma Brother) Cheers you two, TommyRot.
|

10-06-2022, 07:42 PM
|
 |
Senior CC Premier Member
|
|
|
Join Date: Nov 2015
Location: Bellevue,
WA
Cobra Make, Engine: Everett-Morrison 514, Toploader 4 sp, Jag IRS
Posts: 278
|
|
Not Ranked
Exhaust Upgrade May-22
Goals for this project included:
• Reduce decibel level and improve sound quality o Maximize muffler length to reduce decibel level Better protect hearing
o Increase side pipe diameter for a deeper sound
• Eliminate exhaust leaks at header/collector joints and header gaskets o Eliminate contribution to backfiring and flow impact
o Eliminate exhaust fumes/odor from engine bay
• Improve flow characteristics o Reduce reversion contributing to blackening of oil and impacting performance
o Ensure adequate exhaust scavenging and velocity
o Achieve positive performance impact by design
• Improve side pipe levelness, body orientation, and clean overall appearance o Achieve a clean, simple, integrated look
Single open straight pipe appearance
Subtle raw metal look, yet protective coated
Larger external tube diameter for look and sound
• Other - o Improve distance and consistency of pipe to body exit cutouts and to body
o Add O2 sensor bungs in collectors for future exhaust monitoring or EFI scalability
o Improve rear anti-vibration side pipe mountings
This has been a fun project with several improvements. After researching, I decided to use Classic Chambered CobraPack Hi-Flow Cobra mufflers and am pleased with them.
Prior mufflers were 22’ with the prior packing blown out. New mufflers are 3” flow path 36” mufflers, with packing. The mufflers have 4” OD smooth bodies. For a consistent smooth single, straight pipe look, we used matching 4” collectors and tips. The muffler seams were built up with TIG welding and ground/polished down to a smooth single pipe appearance, then ceramic coated.
Before Photos
After Photo
CobraPack Muffler Photos (example photos from Classic Chambered site, not my actual muffler)
 (outside of muffler))
 (inside spiraling)
The existing headers were maintained, with previous rough edges ground down. Prior header ceramic coating was kept, with the ground down areas touched up with high temp exhaust paint. The prior slip on, one bolt header/collector connectors were imprecise and leaked. These were converted to four bolt flange connections. Remflex high heat flexible graphite header and collector crush gaskets, and flanged nuts, were used to ensure sealing (worked well). The flanges were carefully oriented for welding at the proper angles to achieve the desired side pipe level, orientation, and distance from body. This included mating the headers to the merge collectors.
Photo of header/collector upgrade
Since we went away from four tubes exiting the body to a single 4” pipe design, we added an anti-reversion torque cone inside the collector to increase velocity and exhaust scavenging. It looks like a straight pipe with no muffler from the outside (like a semi-truck stack pipe). Yet most of the pipe is actually muffler, with functionality to ensure velocity and anti-reversion (the magic happens inside).
Photos of anti-reversion torque cone
Photos of body exit planning
Photos of side pipes during seam smoothing
The side pipes were extended back further utilizing available space. The longer pipes with turnouts further back now makes it easier to put a foot/leg down for ingress/egress. The simple fact the exhaust tip is a few inches back further helps with cockpit noise as well.
Here are some photos and a video from our two shop-organized test and tune track days at the skid pad during this exhaust upgrade (also testing some other suspension/brake upgrades and engine tuning). If you turn it up on a large computer you can hear the full and deep sounds and pulses the Classic Chambered mufflers and large pipes create.
First Test & Tune Day – The Ridge Skid Pad (crank volume on video for exhaust sound)
The pipes were just tacked together at this point for testing, and were later gap filled/smoothed and ceramic coated. In person, the sound is reminiscent of the old thunder boats.
Photos at initial test & tune day:
Video – initial skid pad session exhibiting new exhaust sound
https://youtu.be/uZyngBczbSw
While I’d intended to finish in satin black as before, I was quite enamored with the raw, metallic silver look at the track before finishing. Working with the ceramic coater, we used his Chromex color but held off on the final bead blasting to leave off the final polish level, then we hit it with a scotch bright pad to give it a raw metallic look, still with ceramic coating protection.
Second Test & Tune Day – The Ridge Skid Pad
The pipes were coated now and we firmed up the coilovers, which helped with body roll. The car felt balanced and predictable, particularly on throttle coming out of corners and changing directions. It did pretty well, considering it has an iron headed 385 series big block (the proverbial 700 pound lump) in the front end. We’re still considering adding a tubular rear anti-roll bar and increasing the strength of the front tubular anti-roll bar.
We dialed in the brake bias at the track after changing rear pads.
Photo of brake bias tuning
Our son’s (family) friend is a professional photographer who’s started his own business and he captured photos and videos at the track. The below video sequence gives various sound shots around the autocross course, where you can hear the new exhaust. These test/tune sessions were my first experience with skid pad, figure 8, and autocross sessions. The video also captures my first ever donut session (just had to try it, the low-brow yay-hoo that I am). The Cobra was a star, with its 90’ wheelbase, it just naturally wanted to perform donuts. That was during the session practicing launch control, working to maximize traction at launch, which was also educational with the Jaguar posi rear end.
Video – Test & Tune Day #2
https://youtu.be/dO1TpLDPF2A
Overall, the exhaust sound is deep and purposeful, while less peaky on the decibels, particularly while cruising (easier to talk). It’s a nice blend of livability and punchiness. So far so good, and a fun day had by all!
Last edited by EM-0785; 10-06-2022 at 08:40 PM..
Reason: Grammar
|

10-06-2022, 09:19 PM
|
 |
CC Member
|
|
|
Join Date: Jan 2007
Location: SEQUIM,
WA
Cobra Make, Engine:
Posts: 138
|
|
Not Ranked
Brent, Wow! You have been busy!
__________________
Jim Nichols
|

10-06-2022, 09:42 PM
|
 |
Senior CC Premier Member
|
|
|
Join Date: Nov 2015
Location: Bellevue,
WA
Cobra Make, Engine: Everett-Morrison 514, Toploader 4 sp, Jag IRS
Posts: 278
|
|
Not Ranked
Quote:
Originally Posted by jknich
Brent, Wow! You have been busy!
|
Hey Jim,
Well I guess it's been a little slow going, I realize I started that writie-up back in May-22, looking at its title, don't know where these last six months went...!
Brent
|

10-10-2022, 11:10 AM
|
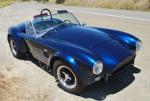 |
Senior Club Cobra Member
|
|
|
Join Date: Dec 2007
Cobra Make, Engine: ERA FIA 'Street' Build
Posts: 2,128
|
|
Not Ranked
Brent,
Not sure how I missed seeing this thread for so long, but glad I just ‘found’ it.
The extensive and detailed refurbishment / upgrade of your Everett-Morrison is impressive as is the documentation. Looks like you have touched just about every part of your Cobra. At this point, I would imagine your ‘to do’ list for your EM would be pretty short.
As to your trailer project, very creative way to build a custom trailer, including a place to park it.
Time to just drive it and enjoy it, keep up the good work and I can’t wait to see what you come up with next!
- Tim
|

10-10-2022, 01:13 PM
|
 |
Senior CC Premier Member
|
|
|
Join Date: Nov 2015
Location: Bellevue,
WA
Cobra Make, Engine: Everett-Morrison 514, Toploader 4 sp, Jag IRS
Posts: 278
|
|
Not Ranked
Thanks Tim, the car is very solid, reliable, and getting very dialed in now. You're correct on the list, I guess I'll need to turn my creative focuses elsewhere, including driving more. To that end, with the latest project done, we've been taking many weekend morning cruises and evening twighlight cruises, and they have just been glorious. What a great hobby we have, enjoy your Cobra! Brent
|
Posting Rules
|
You may not post new threads
You may not post replies
You may not post attachments
You may not edit your posts
HTML code is Off
|
|
|
All times are GMT -7. The time now is 07:20 AM.
Links monetized by VigLink
|