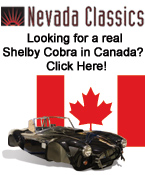 
Main Menu
|
Nevada Classics
|
Advertise at CC
|
S |
M |
T |
W |
T |
F |
S |
|
|
|
1 |
2 |
3 |
4 |
5 |
6 |
7 |
8 |
9 |
10 |
11 |
12 |
13 |
14 |
15 |
16 |
17 |
18 |
19 |
20 |
21 |
22 |
23 |
24 |
25 |
26 |
27 |
28 |
29 |
30 |
31 |
|
|
CC Advertisers
|
|

02-02-2004, 07:12 PM
|
 |
CC Member
|
|
|
Join Date: Jan 2001
Location: Sunbury,
VIC
Cobra Make, Engine: Rat Rod Racer, LS1 & T56
Posts: 5,391
|
|
Not Ranked
I can't take credit for the radiator, I only machined up the brackets for the fan. Norm at Aussie Desert cooler built the rad for me and he's very good with a Tig.
I looked at doing the phase converter with my milling machine. It's a huge Cincinati Toolmaster turret mill about 7' tall. It had a 3HP 3 phase motor on it and I thought about getting 3 phase installed (too expensive) checked out the phase converters but getting one that could deliver enough grunt to drive the motor was pretty expensive too. In the end I bought a 3HP single phase motor and machined up an adaptor plate and new shaft to mount it and it works a treat. I have a 240V 35A main circuit I installed into my workshop and several seperate 15A feeds off that that'll run pretty much every thing I have.
My friends and I have found it much cheaper to buy ex industrial 3 phase equipment than smaller single phase stuff. The single phase stuff is mor popular with home users so fetches a higher price. I'm part of a group friends that have a heap of machinery between us. We can pretty much do most machining jobs between us. I've got more of the small/medium machinery but I've only got a 30'x30' shop. A friend up country has a 30'x90' shop and has some huge 3 phase machines but he's more into fixing tractors and heavy stuff. Great fun to see the size of some the huge cuts he does on the lathe. Stand back or that swarf will grab hold of you
My Tig is a smaller portable unit and it uses Mosfets rather than a transformer to deliver the current. It's fairly basic and doesn't have a high frequency generator in it or a power back off so I can't weld aluminium with it (touch start only). It's great for stainless, molly and mild steel though and that's what I'm using it for. I bought a gas lens for it a couple of weeks back and I'm very impressed with it. I've found I can extend the electrode further to get into tight corners.
I still think the Mig is the best all rounder for a home shop. I set mine up with a teflon liner and a roll of aluminium wire the other day but I think I'll need a fair bit more practice to do a decent aluminium weld. lose your arc and that wire is going to bunch up on the rollers quicker than you can release the trigger. I've got it working OK but it needs a lot more tuning. I've set it up with just a whisker of tension on the pinch roller so that you can stop the wire feeding with your hand and the roller slips. The welds don't look as good as steel yet but... practice practice practice.
I'm not a pro but I think my welding is pretty good. The Mig is my best friend but Tig is still a new skill for me. The Tig skills are steadily improving with practice.
Here's a few pics of my welding

__________________
Mike Murphy
Melbourne Australia
Last edited by Aussie Mike; 02-02-2004 at 07:29 PM..
|

02-02-2004, 08:50 PM
|
CC Member
|
|
|
Join Date: Oct 2002
Location: Above Ground,
Par
Cobra Make, Engine: 2003 Ford Cobra Mustang
Posts: 157
|
|
Not Ranked
Was your rod not long enough when this was welded?

__________________
no signature
|

02-03-2004, 12:11 AM
|
 |
CC Member
|
|
|
Join Date: May 2003
Location: Bugtussell,
AR
Cobra Make, Engine: FFR 4859GT Spyder GT 414W EFI
Posts: 257
|
|
Not Ranked
Howdy Demon,
So, you can download pics and repost them. my 8 yo can do that. Doesn't mean you can weld.
I know 2 guys that can do what you had listed and they make over $150,000.00 a year doing it part-time.
Plus, I don't claim to be a world class welder. I just know enough to know that you know very little 'bout welding.
Plus, how can you TIG weld at 300' underwater? The water will absorb the argon and since you don't know anything about welding, you cannot TIG w/out an inert gas to act as a shield.
Anyway, try to think up more good ones. I'm just unwinding before I go to bed.
Back to my question...."Where's the NON-truth?"
Paul
__________________
"A veteran - whether active duty, retired, national guard, or reserve - is someone who, at one point in his or her life, wrote a blank check made payable to The 'United States of America', for an amount of 'up to and including my life.'" (Author unknown)
|

02-03-2004, 03:17 AM
|
 |
CC Member
|
|
|
Join Date: Jan 2001
Location: Sunbury,
VIC
Cobra Make, Engine: Rat Rod Racer, LS1 & T56
Posts: 5,391
|
|
Not Ranked
Demon didn't mention Tig welding under water he refers to stick welding at depth. I can't see any gain for anyone in the arguments and this is turning into a pissing match. I'm out of here, I don't want my new shoes getting wet in the cross fire.
Cheers
__________________
Mike Murphy
Melbourne Australia
Last edited by Aussie Mike; 02-03-2004 at 03:23 AM..
|

02-03-2004, 03:34 AM
|
 |
CC Member
|
|
|
Join Date: Jan 2001
Location: Sunbury,
VIC
Cobra Make, Engine: Rat Rod Racer, LS1 & T56
Posts: 5,391
|
|
Not Ranked
Rich just wants to gain some welding skills with his Mig in a home workshop environment. Maybe if we try to get back on the subject we can create a thread that will be of some real use to other readers on the forum.
I'm all for learning new skills. I'd like to get my Mig running aluminium better for a start since I havent got $4500 spare for a new Tig with the bells and whistles.
Cheers
__________________
Mike Murphy
Melbourne Australia
|

02-03-2004, 07:28 AM
|
 |
CC Member
|
|
|
Join Date: Jan 2003
Location: Atlanta,
GA
Cobra Make, Engine: CAV GT40 with 331 KC
Posts: 2,187
|
|
Not Ranked
Thanks Mike - I agree.
I wanted to do some aluminum welding with my MIG and was advised by more than one weldor NOT to do it unless I get a spool gun - as those are around $500 I weighed the benefit of learning vs. taking my stuff to a shop that really does a great job.
Of course if I lived far away from such a place I would definitely try it.
The tips I got (if I wanted to try it) were to use a really stiff wire (5XXX) and keep the line as straight as possible.....is that about it?
|

02-03-2004, 07:51 AM
|
 |
CC Member
|
|
|
Join Date: Jan 2004
Location: coronado,
ca
Cobra Make, Engine: revell. snap together
Posts: 84
|
|
Not Ranked
Back on subj. would be good.
you "can" weld with a teflon guide inside your mig gun, and if your doing it just to complete a home welding project, then its acceptable I think. If your production welding aluminum, the cost of a spool gun offsets the loss of materials and man hours wasted on trying work with aluminum and a standard Mig setup.
LateApex. That peice was done as a fitment/volume test peice in a friends Garage.
So, I had to sew it up freehand, and standing up. Without any jigging tools whatsoever. So, what you are seeing is my tack-points. after the assy was tacked, i just went back and closed everything up airtight (for the volume testing). Also, that pic was taken "as welded", no cleanup postweld.
__________________
Gov. bred "Lurker"
|

02-03-2004, 07:53 AM
|
 |
CC Member
|
|
|
Join Date: Jan 2001
Location: Sunbury,
VIC
Cobra Make, Engine: Rat Rod Racer, LS1 & T56
Posts: 5,391
|
|
Not Ranked
Hi Pat,
The guy I get all my welding consumables form is a retired welder and he's been helping me with my set up.
The teflon liner is important to minimise drag on the wire in the lead. it also needs to come right back almost to touch the rollers. This reduces the chance of the wire kinking befor it gets into the liner. The roller tension is very important as it has to be soft enough to let the wire slip if you lose your arc and the wire stalls on the work piece. The tip size was a facor too, this guy reccomends using the next size up tip for your torch to reduce the drag on the wire.
The wire I'm using is 0.9mm but I think 1.0mm would be better but I don't have rollers to fit it.
The rollers should be U groved rather than V groved for aluminium as the V grove can distort the wire and lead to easier kinking.
The workpiece needs to be as clean as possible and should be wire brushed imediatly prior to welding to minimise the surface oxide build up which will give a dirty looking weld and might stall your arc. he also recomends keeping a stainless wire brush handy whilst welding to brush of the oxide that builds from the heat of the weld as you go.
I havent had much time to practice aluminium lately since I had a bunch of steel to weld and it takes a while to swap liners and bottles.
I'd like to just run straight Argon for both Mig and Tig regardless of material. I run a normal CO2 Argon mix for for steel and I'm told it has some different properties for penitration and weld spatter than straight Argon but I can't get a straight answer from the gas companies. I'd like to save a few $$ on the extra bottle rental.
I've been taking my alluminium stuff to a pro welder as well but I'd like to be able to set it up at home just for the challenge. Got to do a bit more investigation.
Cheers
__________________
Mike Murphy
Melbourne Australia
|

06-10-2006, 07:24 PM
|
 |
CC Member
|
|
|
Join Date: Jun 2006
Cobra Make, Engine:
Posts: 92
|
|
Not Ranked
Mike I'll make you jealious my home has 1300 amp 3 phase it is the only building on 3 transformers about 6' from the building. Anyhow I was part owner of a metal fab shop and we generaly stick welded anything over .5", either mig or tig welded .25" to .5", tig or gas welded below .25", and always tig on aluminum. As with anything there are exceptions we made a 2' diameter socket to remove the hub nut on miners, it was cheaper to fab than forge, that took a tool & die maker a minimum of a day to tig the assembly. We never had any sockets come back but they would bend up the handle which was 2"x10', Bubba musta eaten his wheeties that day. Since this forum is primaraly about Cobras my prefference is for most of the welding to be TIG simply because it is too easy to get a cold weld with MIG that is based on someone else doing the welding, I have a defibulator/pacemaker and am not supposed to do electric welding. My bro in law is a certified MIG welder and he welds .25" to over 2" all day with no problems building miners and bout the only thing they don't break is the welds.
Last edited by hssss; 09-08-2006 at 01:34 PM..
|

09-07-2006, 11:07 PM
|
CC Member
|
|
|
Join Date: Feb 2006
Cobra Make, Engine:
Posts: 118
|
|
Not Ranked
Where is Jamo when we need him.......j/k
Guys its not required of you to prove you can weld to give advice. I'm sure you both can weld very well.
However back to the original question. I also have been welding for years on all types of materials which means lots of practice, but for someone who wont do a lot of welding and wants to learn the basics I would suggest your local Junior College of a Tech school for an evening class if you have the time. You just need to get some experience doing it correctly. If time is an issue any of the welding equipment mfg's will supply helpful information if you would like to learn on your own. At least in a classroom you will have some sort of a teacher's help, and you will get to weld a lot. If you go on your own it will just take longer to get to level you feel comfortable with welding on your own stuff. Its true that no situation will be as good as the perfect situation you learn in at school. By the way most of the advice given was good and I'm sure very helpful if more information than you needed.
Best of luck
|

09-08-2006, 12:07 AM
|
 |
CC Member
|
|
|
Join Date: Jan 2001
Location: Sunbury,
VIC
Cobra Make, Engine: Rat Rod Racer, LS1 & T56
Posts: 5,391
|
|
Not Ranked
That's the best advice. When I decided I was going to learn to weld I enroled at the local tech school and did their MIG certificate course. It only cos a couple of hundred and it was a night class 2 nights a week. One night for practical and the other for theory. It went for about 3 or 4 months from memory.
It was very humbling to turn up to the first practical session and find your best welding efforts look like cockatoo sh!t compared to what the instructor was showing us. Not a problem though, the instructor soon showed us where we were going wrong.
Cheers
__________________
Mike Murphy
Melbourne Australia
|

10-04-2006, 03:41 AM
|
CC Member
|
|
|
Join Date: May 2002
Location: Ashburton, New Zealand,
..
Cobra Make, Engine: UK Ram SC. KC-Yates 373, Jerico 5 speed.
Posts: 1,240
|
|
Not Ranked
Welding
Well here goes, I have been welding for years, but dont profess to be a qualified welder, did both MIG and a heap of TIG welding the TIG was mainly stainless steel, and I built stainless steel buggies with a wind sail, that my friend who started the craze off and has International factories, I find stainless steel welding with the TIG quite easy to get good penetration!
Something I didnt bother with until now is I am doing more small circles with the electrode while welding steel to achieve that nice row of dime affect!
My question is with the MIG, I am aware of a good looking weld and little penetration and the inevitable failure, and as I am out of practise, what I do is with 3.2mm steel plate, I just wind up the 190amp MIG flat out, and let rip and it sizzles away, I guess it pays to weave slightly and not go to fast to avoid what Aussie Mike mentions about cold overlap, and I suppose a drag weld is hotter and has more penetration, than a push weld! I have welded heaps of car items with a Mini-Mig about 115amp, and what we did was preheat important parts with the gas and they held up I have never had a failure.......touch wood!
Any tips gratefully appreciated as I am welding up a steel bulkhead (3.2mm) in a few days as I had to re-position my steering column, and the hole is too big, this is a low priority area, so I am welding on a vertical face and going slighty upwards anti clockwise, and would probably do 160amps and do some practise, I suppose another technique do you guys weave to really make sure the surrounding area is contacted. I looked up the MILLER WEBSITE, they list amperage and IPM wire speed.
__________________
A J. Newton
The 1960's rocked!
Last edited by Ant; 10-04-2006 at 03:45 AM..
|

10-04-2006, 05:14 AM
|
 |
CC Member
|
|
|
Join Date: Jan 2001
Location: Sunbury,
VIC
Cobra Make, Engine: Rat Rod Racer, LS1 & T56
Posts: 5,391
|
|
Not Ranked
The trick for doing a verticle up weld is to make little christmas trees. Start in the V of the fillet then move a little to the left side of the fillet then traverse across the center the right side of the fillet. Next move the pool up and into the root of the fillet across to the right side of the fillet then push the pool up and into the V of the fillet then move the torch back to the left side and then traverse back to the right then back up into the V of the fillet. (the drawing will probably make it easier to understand.
You keep working your way up making triangles. What you are doing is building a shelf for the weld pool as you go up and this stops the pool running back down. Traverse quite quickly across over the center of the weld and hold a bit longer on each side. That way you will get good penetration on the sides and maintain a flatter weld. Pushing the pool right into the root of the fillet as you go up is important to making a strong weld.
When the weld is done right it has a nice recuring infinity shaped wave (omega or figure 8 on it's side) as it goes up.
In my opinion this is about the most difficult weld to do. On short runs I can do it OK but after about 8" or 10" I'm starting to loose concentration. Practice makes perfect.
Cheers
__________________
Mike Murphy
Melbourne Australia
|

10-04-2006, 09:49 AM
|
CC Member
|
|
|
Join Date: May 2002
Location: Ashburton, New Zealand,
..
Cobra Make, Engine: UK Ram SC. KC-Yates 373, Jerico 5 speed.
Posts: 1,240
|
|
Not Ranked
MIG Welding
Aussie Mike,
Thanks that information is helpful, that coupled with the welder setup, and a bit of practise.....! Getting that pool working right from experience is important.
__________________
A J. Newton
The 1960's rocked!
|

10-08-2006, 11:27 PM
|
CC Member
|
|
|
Join Date: May 2002
Location: Ashburton, New Zealand,
..
Cobra Make, Engine: UK Ram SC. KC-Yates 373, Jerico 5 speed.
Posts: 1,240
|
|
Not Ranked
Mig welding
Aussie Mike,
I had a go using your diagram pattern, on a test piece, and got very good penetration, in fact you could just see a mild melt on the other side,
As I am going vertical, but also will go vertical/across, does the same technigue apply, and I guess you need same sort of weave for flat welding?
__________________
A J. Newton
The 1960's rocked!
|

10-09-2006, 12:58 AM
|
 |
CC Member
|
|
|
Join Date: Jan 2001
Location: Sunbury,
VIC
Cobra Make, Engine: Rat Rod Racer, LS1 & T56
Posts: 5,391
|
|
Not Ranked
You only need the christmas tree technique when going verticle up to provide a shelf to hold the weld pool up. When you go accross just go straight into it, I don't generally weave. Just watch the weld pool and control your speed to make sure it grabs both sides of the join and also gets right into the root of the fillet. On larger fillet welds it's often better to put a root run in and two capping runs on top. That way you get good root penitration which is where the real strength is. That's for heavy materials ie 10mm thick etc.
Cheers
edited for crappy spelling
__________________
Mike Murphy
Melbourne Australia
Last edited by Aussie Mike; 10-09-2006 at 09:12 AM..
|

01-06-2007, 05:19 AM
|
 |
CC Member
|
|
|
Join Date: Feb 2006
Location: Gore. New Zealand.,
SI
Cobra Make, Engine: DIY Coupe, F/T ,MkIV.
Posts: 808
|
|
Not Ranked
Multi Function Welders
While we are on Migs, have any of you had experience with the Lincoln or other brands Migs AC/DC with pulse on pulse along with Tig, plasma,stick etc all in the one machine. With a mig weld that has the appearance of a tig weld bead ( alloy ) it would seem like the answer to our prayers.  I am at the point where I either have to buy a new Tig or possibly one of these. The idea of tossing all the other individual machines out in favour of one appeals from a space point of view, but heaven help anything breakable if that one shiny machine was to fail & leave me high and dry without a backup.
Jac Mac
|

08-20-2007, 06:57 AM
|
CC Member
|
|
|
Join Date: Jun 2007
Cobra Make, Engine:
Posts: 52
|
|
Not Ranked
Lincoln gives some great classes. They have a one week course in Cleveland and throughout the year they conduct weekend classes in different areas of the country. The instructors are great and (of course) you will be using the latest in Lincoln equipment.
Sign up well in advance, the classes are always full.
One good investment and you will come away with the skills and all of the reference material to weld with confidence.
|
Posting Rules
|
You may not post new threads
You may not post replies
You may not post attachments
You may not edit your posts
HTML code is Off
|
|
|
All times are GMT -7. The time now is 05:29 PM.
Links monetized by VigLink
|