Welcome to Club Cobra! The World's largest
non biased Shelby Cobra related site!
- » Representation from nearly all
Cobra/Daytona/GT40 manufacturers
- » Help from all over the world for your
questions
- » Build logs for you and all members
- » Blogs
- » Image Gallery
- » Many thousands of members and nearly 1
million posts!
YES! I want to register an account for free right now!
p.s.: For registered members this ad will NOT show
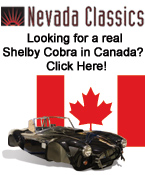 
Main Menu
|
Nevada Classics
|
Advertise at CC
|
April 2025
|
S |
M |
T |
W |
T |
F |
S |
|
|
1 |
2 |
3 |
4 |
5 |
6 |
7 |
8 |
9 |
10 |
11 |
12 |
13 |
14 |
15 |
16 |
17 |
18 |
19 |
20 |
21 |
22 |
23 |
24 |
25 |
26 |
27 |
28 |
29 |
30 |
|
|
|
|
CC Advertisers
|
|
2Likes

12-07-2006, 09:30 AM
|
 |
CC Member
|
|
|
Join Date: Dec 2004
Cobra Make, Engine: Kirkham 427SC, 427 SO from the Fliptop
Posts: 203
|
|
Not Ranked
Kirkham Engineering successfully implemented a product
durability test at a third party location on its gauges (and another competitor) using a shaker table that induces a 2G load at stepped multiple frequencies (HZ) and random burst loads in the laboratory environment and filmed the test with a High Speed video camera @ 1000 frames per second.
The trick, or art, was to run a random
test profile that represents the actual environment. Damage caused by vibration can be the result of either longterm
fatigue or short-duration exposure to high levels of vibration or stress
We left the test very very confident of our gauges and thier ability to hold a reading with out the needle bouncing all over the place. The video will be very revealing
Last edited by Rick162; 12-07-2006 at 09:49 AM..
|
Posting Rules
|
You may not post new threads
You may not post replies
You may not post attachments
You may not edit your posts
HTML code is Off
|
|
|
All times are GMT -7. The time now is 07:10 AM.
|
|