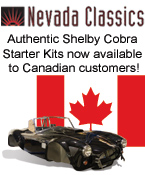 
Main Menu
|
Nevada Classics
|
Advertise at CC
|
S |
M |
T |
W |
T |
F |
S |
|
|
|
1 |
2 |
3 |
4 |
5 |
6 |
7 |
8 |
9 |
10 |
11 |
12 |
13 |
14 |
15 |
16 |
17 |
18 |
19 |
20 |
21 |
22 |
23 |
24 |
25 |
26 |
27 |
28 |
29 |
30 |
31 |
|
|
CC Advertisers
|
|

07-05-2005, 05:58 PM
|
CC Member
|
|
|
Join Date: Jan 2005
Location: Hillsboro,
OR
Cobra Make, Engine: Scratch built CSX style frame, Carbon fiber body, 393 Stroker, T-bird IRS, T5
Posts: 1,623
|
|
Not Ranked
Welding problems
Maybe somebody here can help me out with this problem-
I bought a used wire feed welder- a Miller 135 Mig with bottle and everything included. I haven't used the Mig setting yet or hooked up the bottle, but that isn't the issue at the moment (I don't think) I thought this set up would be the cat's whiskers for this type of fabrication.
I'm using .035 self shielding flux core wire at the highest setting on the machine.
When I'm welding, sometimes the welder starts just jumping, like the wire is jumping in the gun and not striking an Arc when it hits the metal right away. I can't tell if the feed is jumping or I'm losing my arc but it is driving me crazy.
Anybody ever have this happen?
Another problem I'm having is that I have a hard time seeing my joint when welding with the wire feed. With the stick welder it isn't a real problem. Do you guys use a lighter lens for wire feed welding? I think I have a #10 in my helmet now. I noticed if I keep my shield glass real clean it helps a little, but not quite enough.
At this point, except for some tacking chores, I'm back to using my old Miller buzz box stick welder for important work. I'm definitely not a pro welder- in fact, I hope my welds are pretty much where they won't be seen at this point. Thank goodness for a good 4 1/2" grinder!
Thanks, Bob
Last edited by Three Peaks; 07-05-2005 at 06:00 PM..
|

07-05-2005, 06:18 PM
|
CC Member
|
|
|
Join Date: Aug 2004
Location: Tarpon Springs,
fl
Cobra Make, Engine: scratch building
Posts: 182
|
|
Not Ranked
welding
Hey Bob,
i would suggest you get a bottle of gas ,argon-co2 /75-25% for steel .Inner shield is ok but too much spatter and smoke.Mig wire should be adjusted for max penetration and smooth arc like bacon sizzling.get a good grade of solid wire the right gauge for your parent metal and amperage.watch the grade ..no junk..Destruct test some welding coupons before real stock is used and you should be set.Go to miller and lincoln sites for some good info.Gas fed mig welds should look real nice with min spatter...PS. did you consider tig? Jumping wire could be dirty rollers,bad feed pressure,wire drag, too low amps,liner build up...you name it..all takes practice.Hope this helps.
Alex and I use anti spatter and nozzle dip...helps.
|

07-05-2005, 06:26 PM
|
CC Member
|
|
|
Join Date: Aug 2004
Location: Tarpon Springs,
fl
Cobra Make, Engine: scratch building
Posts: 182
|
|
Not Ranked
welding
Almost forgot your question on lens.Use the recommended # and add light to illuminate the joint.I use a high intensity light and pyrex nozzle (tig) to see joint..Push your torch and get as comfortable as possible.Stich weld if needed....your scaring me about the grinder part...Later
Al
|

07-05-2005, 07:51 PM
|
CC Member
|
|
|
Join Date: Jun 2001
Location: Atlanta,
ga
Cobra Make, Engine: Building from scratch
Posts: 141
|
|
Not Ranked
Mig
Bob,
Not much to add but the first thing I would do is buy some solid .035 Hobart wire.
Blow out your wire feed with clean air.
Buy some Lube-Matic and the sponge attachment.
Try setting the tension to about 3 with solid wire.
My guess is the person you purchased it from did not keep it covered while grinding in the shop. The fine metal tends to be attracted to the roll of wire and will eventually end up in your wire feed.
Also, jumping will also happen if your wire is feeding too fast.
As for seeing:
I have noticed the older I get the brighter the light required, and stronger reading glasses I need.
Of course, I am 59 and still doing this building and racing.
I don't know what the highest watt bulbs I will end up with but now it's the Home Depot Floods. LOL
Seriously, try the above with the correct gas pressure, solid wire,
and you will find that it is the cats wisker.
Also, let us know the thickness and we can get pertty close to the correct settings to start.
__________________
Cobracer#15
|

07-05-2005, 08:40 PM
|
CC Member
|
|
|
Join Date: Jan 2005
Location: Hillsboro,
OR
Cobra Make, Engine: Scratch built CSX style frame, Carbon fiber body, 393 Stroker, T-bird IRS, T5
Posts: 1,623
|
|
Not Ranked
I've been welding mostly on the frame tubes to attach some pick up points, motor mounts, and transmission mounts. Now, I'll be mostly welding .120 and .090 for the bird cage and a few other parts.
The welder is the older wire feed type with the 4 settings for amperage instead of the infinite adjustment of the newer machines. I've had to set it to the max setting to get any decent penetration. Where I really have a problem is making vertical welds- they just seem to run like crazy and glob.
I'll try your suggestions and see if it helps. It sure is a lot easier getting into the tight spots with the wirefeed and having continuous feed to weld as opposed to the stick welder.
BTW, I've been using a small quartz halogen work light to illuminate my work area when welding, so you aren't the only old guy around here needing glasses these days. But I'm just spry young'n at 52! LOL  - Bob
|

07-05-2005, 08:49 PM
|
CC Member
|
|
|
Join Date: Apr 2001
Location: Abe Lincolns Birthplace,
Ky
Cobra Make, Engine: CSX4761, KCR Shelby Alloy 496,760hp
Posts: 867
|
|
Not Ranked
Bob,
It just takes some time and practice to get used to the mig,I suggest getting solid wire and 75/25 mix gas.
If the feed is too fast as Alex said it will chatter.Mig is all about speed and setting ,just takes time. I still have a hard time welding thin stuff,exhaust etc.
My 135 came with a vhs that was very helpful,you may want to get your hands on one. good luck,,Tim
__________________
Tk
"this whole Adult thing just isnt working for me "
|

07-05-2005, 11:28 PM
|
 |
CC Member
|
|
|
Join Date: Jul 2000
Location: Las Vegas,
NV
Cobra Make, Engine: 427 SC
Posts: 1,076
|
|
Not Ranked
Bob,
I know some of those Blueshield gases can make the welds hotter and prevent spatter. It may be worth it hook up the gas and use solid wire.
When your welds run and glob up, your speed of travel is too slow, or your heat is too high. If it were me, I would probably speed up some more, or better yet, practice welding downhill. There are well procedures out ther that allow it doing the GMAW process. I do almost all chassis welding with .035 wire in the downhill direction of travel. Just watch the puddle and make sure it stays somewhat egg shaped.
__________________
kris kincaid
|

07-06-2005, 12:03 AM
|
CC Member
|
|
|
Join Date: Jan 2005
Location: Hillsboro,
OR
Cobra Make, Engine: Scratch built CSX style frame, Carbon fiber body, 393 Stroker, T-bird IRS, T5
Posts: 1,623
|
|
Not Ranked
Do you drag your wire in the puddle toward the travel direction like you would with 6013, or do you point the gun toward the direction of travel and push the puddle with the wire?
I'm obviously new with the wire feed but I'm learning fast. I guess I need to invest in some scrap steel and practice, practice, practice.  - Bob
|

07-06-2005, 12:46 AM
|
 |
CC Member
|
|
|
Join Date: Jul 2000
Location: Las Vegas,
NV
Cobra Make, Engine: 427 SC
Posts: 1,076
|
|
Not Ranked
If I am welding a crossmember, I point the gun probably 5 degrees uphill, then let the puddle sort of fall down. I always oscillate the gun when I am Mig welding. It makes some nice looking beads, and if you do it right it makes really nice, strong welds. If you are welding flat, you angle the gun 5 degrees or so away from the weld (or into the direction of travel) and pull the puddle. Never push the puddle or there is a good chance of getting lack of fusion.
__________________
kris kincaid
|

07-06-2005, 09:02 AM
|
 |
Senior Club Cobra Member
|
|
|
Join Date: Sep 2000
Location: Holderness, NH, US of A,
NH
Cobra Make, Engine: CSX 4772 old iron FE
Posts: 5,499
|
|
Not Ranked
Bob the Cobra builder, can he fix it?
Hey Bob, your original problem sounds like polarity to me. Heres the formula, for flux core (what your using) the welder needs the big wire or ground wire to be wired positive. If you are using backing gas (which I prefer) make the ground negative. I also like the previously recommended mixed gas. I use the push technique on welding when I have a gap to fill or thin metal that burns through easily. It isn't something I use structurally or aesthetically. Cleanliness is next to godliness with welding as the boys said, clean welds, anti spatter, clean wire, no rusty wire, clean ground etc. Let us know how you make out.
Cheers Nick
|

07-06-2005, 03:14 PM
|
CC Member
|
|
|
Join Date: Jan 2005
Location: Hillsboro,
OR
Cobra Make, Engine: Scratch built CSX style frame, Carbon fiber body, 393 Stroker, T-bird IRS, T5
Posts: 1,623
|
|
Not Ranked
I've checked the polarity on the machine, and it is hooked up properly for flux core wire. I will need to change it for MIG hook up and gas, only takes a minute.
I'll try the MIG thing in the next couple days and see if it cures some of my problems. My wife says most of my problems are beyond help? Are your wives as mean as mine is?  - Bob
|

07-06-2005, 06:10 PM
|
CC Member
|
|
|
Join Date: Aug 2004
Location: Tarpon Springs,
fl
Cobra Make, Engine: scratch building
Posts: 182
|
|
Not Ranked
welding
Define mean??Mine calls ME a problem.....
Anyway stop by your local book store or Home Depot and get Richard Finch's book "Welders Handbook" bout 18.00 or so. A lot of good tech info.I made my grandson read it before he touched a torch.
Al
|

07-06-2005, 07:20 PM
|
CC Member
|
|
|
Join Date: Jan 2005
Location: Sydney,
nsw
Cobra Make, Engine: N/A
Posts: 31
|
|
Not Ranked
Hey Bob,
With a Mig you should always push the weld, the reason is a Mig is cold on start of weld so if you pull a weld you are always working away from the heat. If you are are pushing you will always be laying the wire into the heat therefore you will have better penetration. I will admit it, i can make a better looking weld by pulling, but it is not the best practice.
Steve
|

07-06-2005, 07:47 PM
|
 |
CC Member
|
|
|
Join Date: Jul 2000
Location: Las Vegas,
NV
Cobra Make, Engine: 427 SC
Posts: 1,076
|
|
Not Ranked
Skulper,
Maybe I am not understanding you, but this is how I weld:
http://www.thefabricator.com/Article...cle.cfm?ID=301
If you have the machine so cold that you cannot get a decent weld pulling, you need to turn it up. 
__________________
kris kincaid
|

07-13-2005, 09:02 PM
|
 |
CC Member
|
|
|
Join Date: Jul 2005
Location: Cedar Rapids,
IA
Cobra Make, Engine: 1966 427 cobra 427 fiberglass shell with intents of a Square tube Aluminum frame.
Posts: 19
|
|
Not Ranked
Three Peaks Alfy is giving good advice! As for the wire kicking back on you you may very well have a bad ground conection to the work peice check your ground wire ends to make sure that they are not dammaged or such. also you cand set your feed roller tention by angling the nozel at 45 degrees into the palm of your gloved hand and pull the trigger the wire should coil up tighten the drive rollers until the wire does not feed into your hand then back off the tention 1 turn.
.035 / 0.9mm solid wire will work perfectly for your aplication no need to go any thicker unless you plan to weld steel that is 2 inches or more thick. use the 75/25 argon/carbon. Flux core wire is OK but if you have a bottle and regulator get rid of the fluxcore!! or you could use up the flux core with the gas (however it will burn alot hotter than normal this way.). The angle grinding your welds is not a good idea you need your weld to be strong as a posible.
I would recomend going to a lighter lens in your hood if you are having a hard time seeing you work peice.
The key to welding is getting comfortable. with steel you can either push or pull= (Like special k's diagram) Aluminum is different you should always push to prevent build up (night crawlers)
good luck
Also you can adjust your wire speed while welding on a peice of scrap you simply adjust the dials till it performs well for you I can usually get a mig to near no spatter just sounds like bolt of electricity.
|

07-24-2005, 02:34 PM
|
CC Member
|
|
|
Join Date: Jan 2005
Location: Hillsboro,
OR
Cobra Make, Engine: Scratch built CSX style frame, Carbon fiber body, 393 Stroker, T-bird IRS, T5
Posts: 1,623
|
|
Not Ranked
Well, I finally had a chance to pick up some wire, get a refill on my Argon/CO2 tank, and get back to welding on my birdcage.
Just wanted to say thanks to everyone who directed me in the right direction.
It has helped immensely to use the shielding gas and solid wire. My welding has improved at least 90%. The other 10% is on me and is probably beyond help, but by time I finish with this frame I should be getting much better at this. Maybe by that time I'll be good enough to start on another one?
I've got most of my birdcage tacked in place now. Just have to make up about 4 more pieces at the front scuttle body support and around the rear of the doors and put it all together. Should be painting the frame in about a week or two- then moving on to suspension.
Are you listening Grumpy?
Thanks again guys- Bob
|

07-25-2005, 08:07 PM
|
 |
CC Member
|
|
|
Join Date: Jul 2005
Location: Cedar Rapids,
IA
Cobra Make, Engine: 1966 427 cobra 427 fiberglass shell with intents of a Square tube Aluminum frame.
Posts: 19
|
|
Not Ranked
Cool Deal Three Peaks sounds like you are pretty stocked! Have fun bro!
|

07-25-2005, 08:11 PM
|
CC Member
|
|
|
Join Date: Jan 2005
Location: Hillsboro,
OR
Cobra Make, Engine: Scratch built CSX style frame, Carbon fiber body, 393 Stroker, T-bird IRS, T5
Posts: 1,623
|
|
Not Ranked
BTW, what do you set your flow guages at? The guy at the welding/gas place said to set the flow at 25 lph, but man am I using up gas fast! That little 20 cf tank isn't going to last long at the rate I'm going!
Guess it's time to invest in a 40cf tank?
|

07-25-2005, 09:54 PM
|
 |
Senior Club Cobra Member
|
|
|
Join Date: May 2001
Cobra Make, Engine: A CSX Cobra,1966 GT350 and an '06 Ford Heritage GT
Posts: 1,829
|
|
Not Ranked
Thats a lot of argon flow! Step back to 20 or so. Another useful hint...use anti-spatter spray. You can use less argon and still get good shielding and it's a lot easier to clean up.
__________________
"I think we have more machinery of government than is necessary, too many parasites living on the labor of the industrious." Thomas Jefferson
|

07-25-2005, 10:50 PM
|
CC Member
|
|
|
Join Date: Mar 2002
Location: Plantersville,
TX
Cobra Make, Engine: Self Built, 427 USRRC, 427FE, Toploader
Posts: 583
|
|
Not Ranked
3Peaks,
Cut her down to 16.5 or so on your flow, and use a "u" shape movement on the puddle, then set you your feed and heat lower for your 0.75"x.065" birdcage tube joints.
We have a two small 220amp Lincolns for the birdcage/jigged portion of our chassis fabrication and have found that if you select 0.023 wire in a 0.025 tip it runs beautifully for speed and economy.
Practice, practice, practice, in other words build a dozen or so and you will have a joint that looks as good as a lot of TIG joints at 60% the cost.
grumpy
|
Posting Rules
|
You may not post new threads
You may not post replies
You may not post attachments
You may not edit your posts
HTML code is Off
|
|
|
All times are GMT -7. The time now is 03:38 PM.
Links monetized by VigLink
|