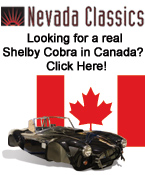 
Main Menu
|
Nevada Classics
|
Advertise at CC
|
S |
M |
T |
W |
T |
F |
S |
1 |
2 |
3 |
4 |
5 |
6 |
7 |
8 |
9 |
10 |
11 |
12 |
13 |
14 |
15 |
16 |
17 |
18 |
19 |
20 |
21 |
22 |
23 |
24 |
25 |
26 |
27 |
28 |
29 |
30 |
31 |
|
|
|
|
|
CC Advertisers
|
|
4Likes

03-26-2006, 10:16 PM
|
 |
CC Member
|
|
|
Join Date: Jan 2001
Location: Sunbury,
VIC
Cobra Make, Engine: Rat Rod Racer, LS1 & T56
Posts: 5,391
|
|
Not Ranked
The pic of mine was after a quick scrub with a wire brush. The soot looks nasty but comes off easy. Welding aluminium also makes a lot of smoke too. Definitly a job to be done in a well ventilated workshop.
I usually keep to a fairly sheltered spot when welding as I'm a bit cheap and try to keep my shielding gas uses to a minimum. When I'm finished I open up the doors and turn a fan on to clear the air. I'll often wair my spray painting respirator under my welding helmet as well.
Cheers
__________________
Mike Murphy
Melbourne Australia
|

03-27-2006, 01:20 AM
|
 |
CC Member
|
|
|
Join Date: Jun 2000
Location: Cape Town, South Africa/Mainz, Germany,
Posts: 1,601
|
|
Not Ranked
stainless
hi Nick,
okay: I try another one.
when working with stainless (welding as well), never use tools that have been used with mild steel.
stainless will attract the rust from mild steel and start to corrode.
after welding stainless clean the heat affected zone generously at least with distilled water or better yet with a suitable cleaning agent.
otherwise you will get rust close to where you welded and not only at the weld!
dominik
__________________
If I don't respond anymore, that's because I can't log in
|

08-30-2006, 03:08 PM
|
 |
CC Member
|
|
|
Join Date: Aug 2006
Location: Van Buren, AR,
AR
Cobra Make, Engine: B & B , 351W 400+
Posts: 153
|
|
Not Ranked
Re: Mig Aluminum - Try to watch out for that crater at the end of the weld. Cracks start in craters as the weld pool cools and the material shrinks. Also, the welds should be at worst flat, better if a little convex (higher in the center). Use the right filler material for the base metal both for strength and appearance. Miller and Lincoln both have a lot of published materials on Mig and Tig aluminum welding. Buy your welding equipment and supplies from a welding supply distributor as opposed to Lowes or some tool company. You can negotiate for as good a price (or better) AND get all the consulting and welding hints you need.
|

09-19-2006, 07:31 PM
|
 |
CC Member
|
|
|
Join Date: Sep 2006
Location: Avenue,
Md
Cobra Make, Engine: scratch built (in process) 4.6 2v mustang
Posts: 61
|
|
Not Ranked
Mike, Wish you were in my backyard. That is some beautiful work. Not many in my area good with alum.
stangden (Dennis)
|

09-19-2006, 07:43 PM
|
 |
CC Member
|
|
|
Join Date: Jan 2001
Location: Sunbury,
VIC
Cobra Make, Engine: Rat Rod Racer, LS1 & T56
Posts: 5,391
|
|
Not Ranked
Truth be known I'm not that good with aluminium. I'm getting better results with practice but I'm no where near what the professional welders can do.
I must say it's very satisfying when you do a good weld on any material.
Practice, practice, practice.
Cheers
__________________
Mike Murphy
Melbourne Australia
|

05-15-2007, 07:33 PM
|
 |
CC Member
|
|
|
Join Date: Mar 2007
Location: Alpena,
Mi
Cobra Make, Engine: Scratch building frame,FFR Mkll body ,302w, and T5 trans, 3.0 rear.
Posts: 416
|
|
Not Ranked
I've welded in the factory for over 15 years and the secret to good welda of ANY kind is practice,practice and more practice. I've done very little aluminum welding, mostly while in the reserves ( Air Force) but I love my 120v mig unit for body work and my old 225 Lincoln for heavier stuff. just my .02 worth.
__________________
1963 Mercury Monterey 460+ .060 .//Cobra clone, Scratch build frame /302/ T-5 WC / 3.00-9in/FFR mkll body (Broken but repairable) /91 Lincoln Wire Wheels  //  :  N.S.M.C Charter/Life Member// Die Hard Blue Oval Nut
The finish is better than the beginning. Ecc7:8
|

12-29-2009, 03:21 AM
|
 |
CC Member
|
|
|
Join Date: Oct 2009
Location: United States,
pon
Cobra Make, Engine: United States
Posts: 9
|
|
Not Ranked
Welding and Materials
My latest welding project, a mailbox for the wife. I purchased a set of scroll benders from Harbor Freight last month to bend the scroll pieces and twist the flat bar. All of the pieces were welded using an old Sears Mig welder I just bought. The mig machine worked great after I purchased Lincoln wire, the original owner had been using some really cheap wire that wouldnt even burn...another great deal on a broken welder
This picture is just before we installed the box.
Keith
|

12-29-2009, 07:18 AM
|
 |
Senior Club Cobra Member
|
|
|
Join Date: Sep 2000
Location: Holderness, NH, US of A,
NH
Cobra Make, Engine: CSX 4772 old iron FE
Posts: 5,499
|
|
Not Ranked
I've also found a big difference between wire brands, especially on aluminum MIG. The polarity has to be set correctly for flux core or it won't burn properly or at all.
|

06-09-2011, 12:36 AM
|
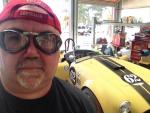 |
CC Member
|
|
|
Join Date: Feb 2002
Location: Alice Springs, central Australia,
NT
Cobra Make, Engine: Classic revival kit (CR3181), gen III engine, T56 6 speed box, AU XR8 lsd diff
Posts: 5,699
|
|
Not Ranked
I am wondering if anyone knows of a printable flow chart that shows amperage versus material thickness and argon flow rates for TIG welding?
I have found a Miller online chart, but really want something I can print off, laminate and hang off my welding trolly.
Cheers for any help.
__________________
Cruising in 5th

---------------------------------------------
Never be afraid to do something new, Remember, Amateurs built the Ark: Professionals built the Titanic.
|

06-09-2011, 01:32 AM
|
 |
CC Member
|
|
|
Join Date: May 2001
Location: California,
Ca
Cobra Make, Engine: NAF 289 Slabside Early Comp Car with 289 Webers and all the goodies. Cancelling the efforts of several Priuses
Posts: 6,592
|
|
Not Ranked
I believe the aluminum boodies are & were gas welded.
Several years ago I watched a fellow gas weld aluminum mufflers for RC Control Planes at the manufacturing plant in the outskirts of Sacramento. It was a work of art to see the aluminum just reach the point were it began to flow and see him dab the aluminum filler rod in the puddle.
__________________
Rick
As you slide down the Banister of Life, may the splinters never be pointing the wrong way
|

06-09-2011, 02:06 AM
|
Senior Club Cobra Member
|
|
|
Join Date: Feb 2008
Location: Jacksonville,
FL
Cobra Make, Engine: VSE alum. frame, FFR carbonfiber body (under construction)
Posts: 293
|
|
Not Ranked
Boxhead:
Miller makes a nice quick reference calculater; It is a sleve with a card inside that you slide up and down to identify material type, thickness, etc.: (Miller TIG welding Calculator 171086):
Miller TIG Welding Calculator 171086
Good luck,
John
|

06-09-2011, 12:46 PM
|
 |
Stolen Avitar
|
|
|
Join Date: Oct 2004
Location: Brunswick,
GA
Cobra Make, Engine: BDR 1311 428PI
Posts: 3,044
|
|
Not Ranked
I bought a Lincoln 216 a few months back to replace a smaller flux only unit that was stolen. I bought it at that time because they were running a special where you could get $100 back or you could get a spool gun. Of course I went for the spool gun. With the small aluminum stuff that I've done so far I'd have had much better luck with a TIG but that would be $$$$ and this is way better than what I had before anyway. I found out the hard way about moving fast as the first couple of scraps that I tried to weld just turned into molten AL and dripped on the floor. Luckily not my feet! My Lincoln also has a reference chart for power, metal gauge, wire speed/thickness, etc. on the inside of the cover. I've found that to be quite convenient so far.
Steve
|

06-09-2011, 09:05 PM
|
 |
Senior Club Cobra Member
|
|
|
Join Date: Sep 2000
Location: Holderness, NH, US of A,
NH
Cobra Make, Engine: CSX 4772 old iron FE
Posts: 5,499
|
|
Not Ranked
I just got Eastwoods 175 MIG with a spool. I just repaired some 16 Ga ally body work with it and had minimal distortion. It really shouldn't weld anything that thin but a copper backing block is the trick there, that and the right push angle. I would have preferred to TIG that thickness but I'm sure it would have wrinkled up like Grandma.
|

06-10-2011, 06:25 AM
|
 |
CC Member
|
|
|
Join Date: Dec 2010
Location: Allen,
TX
Cobra Make, Engine: Werk77 289FIA
Posts: 1,295
|
|
Not Ranked
Quote:
Originally Posted by COBRANIP
Boxhead:
Miller makes a nice quick reference calculater; It is a sleve with a card inside that you slide up and down to identify material type, thickness, etc.: (Miller TIG welding Calculator 171086):
Miller TIG Welding Calculator 171086
Good luck,
John
|
John,
Miller direct charges only $1.50 --- besides that Miller has the calculator online for free...
Miller - TIG Welding Calculator
__________________
Scratch build 289 FIA see the Scratch builder forum on CC - sold
DRB GT40 MK1 red #49- sold
FF5 Mk4 #7733 302/T5/IRS - dark blue - sold
FF5 MK4 #7812 427/TKO/IRS - Guardsman Blue - sold
FF5 MK4 #8414 501/TKO600/48IDA Ollie the Dragon #91 - sold
FF5 Daytona Coupe 347/TKO/IRS Homage CSX2299 Viking Blue - sold
SPF 2063
|

12-09-2015, 12:15 AM
|
 |
CC Member
|
|
|
Join Date: Dec 2015
Location: Clarksville,
TN
Cobra Make, Engine: Scratchbuild, 289 FIA Replica
Posts: 198
|
|
Not Ranked
I'm relatively new to the forum, and notice this section doesn't get much play.
I used to be an A&P mechanic and have welded up a few aircraft tube steel frames out of 4130 chromoly using Oxy-Acetylene out of a micro-torch. I'm wondering if anyone out there is scratch building Cobra frames using this or everyone is just using TIG/MIG.
I'm also looking for reliable drawings for the Cobra frame, or a modern adaptation that would work.
|

12-09-2015, 02:11 AM
|
 |
CC Member
|
|
|
Join Date: Aug 2009
Location: Adelaide,
SA
Cobra Make, Engine: AP 289FIA 'English' spec.
Posts: 13,152
|
|
Not Ranked
Quote:
Originally Posted by 120mm
....or a modern adaptation that would work.
|
Could try an AP semi-monocoque:
http://www.absolutepace.com/images/brochure_pace427.pdf
Cheers,
Glen
|

12-09-2015, 06:07 AM
|
 |
CC Member
|
|
|
Join Date: Jun 2000
Location: Cape Town, South Africa/Mainz, Germany,
Posts: 1,601
|
|
Not Ranked
Drawings
Welcome 120mm!
I built a handful of chassis based on the Cobra Restorers drawings. They are actually not that bad. I did improve on a few measurements, based on a CSX 4000 chassis which I measured here in South Africa. I can't recall the changes because I built the last one years ago. The scuttle hoop is critical.
Mickmate build a usable chassis from CR prints and might be able to assist.
There are plenty of modern adaptions around, and it's a matter of preference I suppose.
I drew up a chassis from a SA built version, done by a local race car builder, whose car handled extremely well. I managed the same lap times with a 302 and 290hp as the local 300+ hp 911s.
What I mean is, plenty of chassis that behave 90% well if the suspension is thought through nicely. The other 10% I leave to the professionals :-)
__________________
If I don't respond anymore, that's because I can't log in
|

12-15-2015, 09:38 AM
|
CC Member
|
|
|
Join Date: Aug 2004
Location: Tarpon Springs,
fl
Cobra Make, Engine: scratch building
Posts: 182
|
|
Not Ranked
CR drawings
I used the CR drawings but modified to portion of rear frame to be a little different for the jag rear end...seems ok so far...scuttle tube had to be lowered about an inch or so to fit the body that I used...trial and error..lol.... used a tig for all steel, stainless and aluminum...
|

12-15-2015, 11:29 AM
|
 |
CC Member
|
|
|
Join Date: Dec 2015
Location: Clarksville,
TN
Cobra Make, Engine: Scratchbuild, 289 FIA Replica
Posts: 198
|
|
Not Ranked
So, the "scuttle tube" or "scuttle hoop" is the lateral curved tubing behind and/or in front of the cockpit that lends the body support and shape?
Looking at various build photos, I don't see how it is essential, strength-wise, to the chassis. So would it be possible to leave these off until the body is selected and fitted?
Sorry if that's a dumb question. I've welded up a few Piper Cub fuselages and they have a central core for strength and an outer framework for shape. Am wondering if these are similar structures. With those, I tacked everything together first to make it easier to "try and fit" the rest of the structure, then finish welded using skip welding to keep warpage down.
|

12-15-2015, 01:11 PM
|
CC Member
|
|
|
Join Date: Aug 2004
Location: Tarpon Springs,
fl
Cobra Make, Engine: scratch building
Posts: 182
|
|
Not Ranked
Support
Supports the cowl, dash ,door hinges front coil over uprights and adds ridgety to the frame..I put in a bolt in backbone over transmission to add some strength.. no reason not to set a body in place and tack in support tubes..I think my gallery might show you some frame pics that might help.
Last edited by alfy65; 12-15-2015 at 03:07 PM..
|
Posting Rules
|
You may not post new threads
You may not post replies
You may not post attachments
You may not edit your posts
HTML code is Off
|
|
|
All times are GMT -7. The time now is 06:39 AM.
Links monetized by VigLink
|