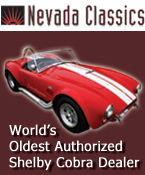 
Main Menu
|
Nevada Classics
|
Advertise at CC
|
S |
M |
T |
W |
T |
F |
S |
|
|
|
|
|
1 |
2 |
3 |
4 |
5 |
6 |
7 |
8 |
9 |
10 |
11 |
12 |
13 |
14 |
15 |
16 |
17 |
18 |
19 |
20 |
21 |
22 |
23 |
24 |
25 |
26 |
27 |
28 |
29 |
30 |
|
CC Advertisers
|
|
4Likes

02-21-2006, 07:14 AM
|
CC Member
|
|
|
Join Date: Jun 2001
Location: Atlanta,
ga
Cobra Make, Engine: Building from scratch
Posts: 141
|
|
Not Ranked
Welding and Materials
All Welding and or Material
__________________
Cobracer#15
|

02-21-2006, 07:26 PM
|
 |
CC Member
|
|
|
Join Date: May 2001
Location: California,
Ca
Cobra Make, Engine: NAF 289 Slabside Early Comp Car with 289 Webers and all the goodies. Cancelling the efforts of several Priuses
Posts: 6,592
|
|
Not Ranked
Huh???????????????
__________________
Rick
As you slide down the Banister of Life, may the splinters never be pointing the wrong way
|

02-21-2006, 07:36 PM
|
 |
CC Member
|
|
|
Join Date: Jun 2004
Location: Amarillo,
TX
Cobra Make, Engine: Scratch build......a little every day.
Posts: 563
|
|
Not Ranked
Yes
To build a Cobra from scratch, you will need both. 
__________________
55 mph is unsafe at any speed. Huh?
|

02-21-2006, 07:46 PM
|
 |
Senior Club Cobra Member
|
|
|
Join Date: Jan 2004
Location: St. Louis,
Mo.
Cobra Make, Engine: 427 S.O. Dual Quad / Cobra undecided
Posts: 1,380
|
|
Not Ranked
What Rick said.............???????
|

02-21-2006, 08:09 PM
|
 |
Senior Club Cobra Member
|
|
|
Join Date: Sep 2000
Location: Holderness, NH, US of A,
NH
Cobra Make, Engine: CSX 4772 old iron FE
Posts: 5,499
|
|
Not Ranked
Thanks Alex
Some excellent topic starters for us. I guess they don't appreciate the value of such discussion. They can help by keeping stuff near the top I suppose. I however am part of another very good thread you started with a mere 159 replies and 7053 views 
|

02-21-2006, 09:01 PM
|
 |
CC Member
|
|
|
Join Date: Dec 2000
Location: Los Angeles,
CA
Cobra Make, Engine: E.R.A. FIA #2088 1964 289 w/Webers
Posts: 2,151
|
|
Not Ranked
Will Cast iron rod work?  So I get really intrested in metal shaping every so often & would really like to learn more. I have read some books & would really like to get my hands dirty, so to speak.... Armed with a million questions I'll start by asking some of the stupid ones. On an aluminum bodied car when the panels are shaped are they welded together? What is the process here?
__________________
Hyde D. Baker
|

02-21-2006, 09:54 PM
|
 |
CC Member
|
|
|
Join Date: Feb 2006
Location: Bellows Falls,
vt
Cobra Make, Engine: ERA 289 fia #2110, 302/331
Posts: 34
|
|
Not Ranked
i a in the middle of a welding class so i am far from an expert. I know aluminum can be welded by a TIG welder. they are a little expensive but they are very nice. I will probably be purchasing a miller 135 mig welder. it can weld up to 1/4 in. steel and runs about $630. it seems like a great welder. we don't get to try TIG welding this class tho. anywho, ya you can weld aluminium, it just takes practice. i am taking classes at a local community college which are held at a metal shop and they are great, they have the equip and supplies. if you can find some classes, they are worth it.
__________________
Dreams of Maine coastal roads....
|

02-22-2006, 06:53 AM
|
 |
CC Member
|
|
|
Join Date: Dec 2000
Location: Los Angeles,
CA
Cobra Make, Engine: E.R.A. FIA #2088 1964 289 w/Webers
Posts: 2,151
|
|
Not Ranked
We have a few welders at work, including an aluminum spool gun which seems to work really well. I need to go in work clothes some day so i can get in & get dirty.
__________________
Hyde D. Baker
Last edited by Tongue Pirate; 02-22-2006 at 09:11 PM..
|

02-22-2006, 11:03 AM
|
CC Member
|
|
|
Join Date: Sep 2003
Location: Bronxville, NY,
Posts: 96
|
|
Not Ranked
TiG welding aluminum takes a bit of practice and hand/eye/foot coordination, but its great fun. Just be careful not to rest your elbow on the (steel) workbench or you can get a zap you'll remember for a long time
|

02-22-2006, 04:14 PM
|
CC Member
|
|
|
Join Date: Nov 2003
Location: New Britain,
CT
Cobra Make, Engine: Size 10 Feet
Posts: 3,011
|
|
Not Ranked
Quote:
Originally Posted by Tongue Pirate
We have a few welders at work, including an aluminum pool gun which seems to work really well. I need to go in work clothes some day so i can get in & get dirty.
|
Dirty is the operative word. With aluminum, both TIG and MIG require clean metal. Especially MIG, since DC current doesn't clean as well as the AC of TIG. Use a solvent to remove any oils and a stainless wire brush immediately before you weld.
Last edited by strictlypersonl; 02-22-2006 at 04:20 PM..
|

02-22-2006, 05:16 PM
|
 |
CC Member
|
|
|
Join Date: Aug 2004
Location: SE Wisconsin,
Wi
Cobra Make, Engine: Arntz/SBC/Jag
Posts: 1,033
|
|
Not Ranked
Cleanliness IS godliness where the metal meets the metal !
|

02-22-2006, 08:44 PM
|
 |
Senior Club Cobra Member
|
|
|
Join Date: Sep 2000
Location: Holderness, NH, US of A,
NH
Cobra Make, Engine: CSX 4772 old iron FE
Posts: 5,499
|
|
Not Ranked
Aluminium welding
The stainless brush should be used only on your aluminum and not get contaminated with any other uses. MIG is good for thicker aluminum but requires at least a teflon liner or better yet a spool gun. It runs hot and fast and requires a push technique for gas coverage and a big contactor to work gap as it is actually a spray transfer process. TIG is good for control and thinner materials. It is a bit of a head game as you have to break through the oxide and make a molten puddle to get it going. Once it is going it really crackles and spits as the magnesium alloy in it burns. There are some good tips and tricks on these at the miller web site.These first two make too much heat and distortion on your freshly hand beaten body panels. For that you need to braze them together with a flame and flux (or flux core) and rod. There is some awesome Cobra and other aluminum car stuff as well as good information on the tools, tin knockers links etc at http://panel-craft.com I didn't mean to make it a sermon. I just happened to be trying to dial in a spool gun at the moment. It should be worth it and save me a lot of TIG time on a big job I'm doing. Good stuff ain't it!
|

02-22-2006, 10:45 PM
|
 |
CC Member
|
|
|
Join Date: Jan 2001
Location: Sunbury,
VIC
Cobra Make, Engine: Rat Rod Racer, LS1 & T56
Posts: 5,391
|
|
Not Ranked
I spent a bit of time getting my 200 Amp Mig running aluminium and I'm getting good results now. mickmate is right, you get your best results in spray transfer. That means lots of current and wire and a steady hand cause you've got to work quite fast. I've been welding thicker materials with mine and getting quite good at it. Preheating larger pieces certaily helps. I've got a portable gas stove that I sit the larger work piece on. I welded up a manifold for Bernies Cobra a while back and the gas stove worked a treat for preheating it.
Getting the teflon liner, rollers and tip right is the key I reckon. I went through 2 liners getting mine right. You need to set up the liner so it so close to the rollers that it rubs on them. This stops the wire from bunching up at the rollers if your arc goes out and the wire hits the work piece or if it sticks in the tip. You also need the brass sleeve that slides over the outside of the liner to keep it straight where it meets the roller.
U grove rollers have more surface contact with the wire and mean you don't use so much tension on the pinch roller. The wire will still drive smoothly but you can back the tension off enough that the rollers slip if the wire jams. It takes a bit of experimentation to get the pinch roller tension right.
The other trap is the tips. 0.9mm aluminium wire tips have a larger hole than a 0.9mm steel wire tip. Aluminium expands more when heated so it needs a bit more clearance or it'll jam in the tip. If you don't have any aluminium tips available just use the next size up steel tip i.e. a 1.0mm or even 1.2mm steel tip for 0.9mm aluminium wire.
You can get some great results on nice clean billet aluminium but castings can have variable results due to the porosity of the material and casting sand trapped in the pores. The weld may look good on the outside but hit it with a grinder and you may see bubbles.
Here's one of my home made quick jacks prior to polishing. They were water cut from 6mm aluminium plate.
Cheers
Michael
__________________
Mike Murphy
Melbourne Australia
|

02-23-2006, 06:17 PM
|
 |
Senior Club Cobra Member
|
|
|
Join Date: Sep 2000
Location: Holderness, NH, US of A,
NH
Cobra Make, Engine: CSX 4772 old iron FE
Posts: 5,499
|
|
Not Ranked
Hey Mike, that is a beauty piece of work! I have a question as I play with dialing this spool gun in. Are you running a weave to the bead? I am going like stink across this thing and don't know if I'd even have time for a weave. It seems I have to go fast to keep it cool enough to not burn through. The push with a slight angle helped a lot on keeping it more consistent along the weld. I'm going to play and see if I can come even close to what your doing
Cheers
|

02-23-2006, 07:25 PM
|
 |
CC Member
|
|
|
Join Date: Jan 2001
Location: Sunbury,
VIC
Cobra Make, Engine: Rat Rod Racer, LS1 & T56
Posts: 5,391
|
|
Not Ranked
No weave for me either. It's fairly blazing in spray transfer and you have to move quick. I run my torch in at nearly a 45 degree angle with about a 1 to 1.5cm arc. If I have it too close I find I too much buildup of spatter in the nozel. With the torch at this angle you can see what the pool is doing and push it right into the root of the fillet.
I've never been much of a weaver anyway. The only time I really do is a second pass, the root run is usually straight in to try and get the best penitration. I'm just a back yard welder but I think being able to watch and carefully control the pool is the key to getting a good result.
Cheers
__________________
Mike Murphy
Melbourne Australia
|

02-23-2006, 08:17 PM
|
 |
Senior Club Cobra Member
|
|
|
Join Date: Sep 2000
Location: Holderness, NH, US of A,
NH
Cobra Make, Engine: CSX 4772 old iron FE
Posts: 5,499
|
|
Not Ranked
Great advice thanks. That seems like quite the angle Miller recommended a 10-15 deg. I'll try your method and see what it does for me. I'm going for it tonight I'm even inspired to try and attach a pic.
|

02-23-2006, 09:09 PM
|
 |
CC Member
|
|
|
Join Date: Jan 2001
Location: Sunbury,
VIC
Cobra Make, Engine: Rat Rod Racer, LS1 & T56
Posts: 5,391
|
|
Not Ranked
It's probably more like 30 degrees now I look at it and think about it.
Nice looking weld, is that aluminium?
My next big aluminium welding project is building a blower manifold for to fit an Eaton M112 onto to my LS1. I'm looking forward to doing it but have a lot of other jobs to finish first.
Cheers
__________________
Mike Murphy
Melbourne Australia
|

03-07-2006, 07:51 AM
|
 |
Senior Club Cobra Member
|
|
|
Join Date: Sep 2000
Location: Holderness, NH, US of A,
NH
Cobra Make, Engine: CSX 4772 old iron FE
Posts: 5,499
|
|
Not Ranked
I ran out my first spool of .035" and threw in the 0.030". It started sticking and melting to the inside of the 0.035" tip so I threw a little more wire speed at it to try and cool it. NFG I'm going back to 0.035" wire and my original settings.
|

03-26-2006, 02:58 AM
|
 |
CC Member
|
|
|
Join Date: Jun 2000
Location: Cape Town, South Africa/Mainz, Germany,
Posts: 1,601
|
|
Not Ranked
clean it!
as SP said,
clean is the formula to work with.
I am not a welder, but we learned that laser cut parts don't like to get welded before you clean the "cut".
similar to grinding galvanized sheet metal to the bare metal before you start.
dominik
__________________
If I don't respond anymore, that's because I can't log in
|

03-26-2006, 08:03 PM
|
 |
Senior Club Cobra Member
|
|
|
Join Date: Sep 2000
Location: Holderness, NH, US of A,
NH
Cobra Make, Engine: CSX 4772 old iron FE
Posts: 5,499
|
|
Not Ranked
We covered that thanks Dom. We clean aluminum with a stainless wire brush that is only used for aluminum. The weld looks dirty as they make a lot of soot. The photo is after weld with no cleaning though the soot comes off easily.
|
Posting Rules
|
You may not post new threads
You may not post replies
You may not post attachments
You may not edit your posts
HTML code is Off
|
|
|
All times are GMT -7. The time now is 02:26 AM.
Links monetized by VigLink
|