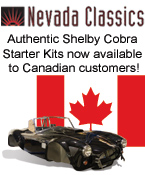 
Main Menu
|
Nevada Classics
|
Advertise at CC
|
April 2025
|
S |
M |
T |
W |
T |
F |
S |
|
|
1 |
2 |
3 |
4 |
5 |
6 |
7 |
8 |
9 |
10 |
11 |
12 |
13 |
14 |
15 |
16 |
17 |
18 |
19 |
20 |
21 |
22 |
23 |
24 |
25 |
26 |
27 |
28 |
29 |
30 |
|
|
|
|
CC Advertisers
|
|

08-06-2010, 02:56 PM
|
CC Member
|
|
|
Join Date: Dec 2004
Location: Kansas City,
KS
Cobra Make, Engine: jbl
Posts: 2,291
|
|
Not Ranked
jb weld in engine valley
putting some fittings in an engine valley and using jb weld to hold them, has anyone done this and does the stuff stay put and not crack out or come loose? cast iron block
|
-
Advertising

08-06-2010, 03:12 PM
|
Senior Club Cobra Member
|
|
|
Join Date: Jul 2002
Cobra Make, Engine:
Posts: 15,712
|
|
Not Ranked
Pssst, don't tell anyone, I like JB Weld, use it for all kinds of stuff. I had a crack in an oil pan that was seeping oil, I wasn't sure that would hold (heat, vibration, hot oil). Heck it worked out real well. Also used it on the seam of a gas tank, good to go! It don't get much respect around here...
I guess my biggest concern would be if the area wasn't prepped really good (clean beyond clean and into the sanitary zone) what if it came loose and the oil pump ate it?
I don't generally use any kind of epoxy in an area where something like that could happen. Heck you even hear about intakes with epoxy used for smoothing or whatever, and then a chunk breaks loose. Not good... Just something to consider.
|

08-06-2010, 04:39 PM
|
CC Member
|
|
|
Join Date: Oct 2003
Posts: 4,078
|
|
Not Ranked
I've used it on cast iron inside a block in a high oil area. Never came out or failed. The key is a bone-dry, hospital-clean prep.
__________________
Chas.
|

08-06-2010, 09:11 PM
|
 |
Senior Club Cobra Member
|
|
|
Join Date: Jul 2001
Location: Carrollton,
TX
Cobra Make, Engine: JBL now SOLD
Posts: 1,735
|
|
Not Ranked
I've seen more than once where BBC folks use epoxy in the lifter valley to glue wire mesh over the drain holes. So if it were to fail they would have two materials loose inside the engine, but they seem to trust it.
__________________
6th generation Texan....
|

08-07-2010, 04:21 AM
|
CC Member
|
|
|
Join Date: Dec 2004
Location: Kansas City,
KS
Cobra Make, Engine: jbl
Posts: 2,291
|
|
Not Ranked
i've seen the epoxy stuff used but not sure i could get the right stuff. i'm using the jb weld to secure brass fittings. hospital-clean-dry. thanks for the info guys. sssshhhhhhh, now everybody walk away quietly.
|

08-08-2010, 12:45 AM
|
 |
CC Member
|
|
|
Join Date: Feb 2007
Location: Colorado Springs,
CO
Cobra Make, Engine: Backdraft, supercharged Coyote
Posts: 2,453
|
|
Not Ranked
I use JB Weld for a lot of stuff. It works well, but doesn;t last forever. Heat, vibration, and oil will cause it to break down. I would not put it in the lifter valley. 2-3 years from now, you'll wish you didn't.
It's not the same as epoxy.
|

08-08-2010, 02:30 AM
|
 |
CC Member
|
|
|
Join Date: May 2002
Location: Beaufort,
SC
Cobra Make, Engine: Classic Roadsters '66 427 Replica-SOLD
Posts: 299
|
|
Not Ranked
I JB "Welded" a steel washer in the aluminum pan on the transmission in my 04 Mercury Marauder 3 years ago!!  It holds the magnet it place that catches any ferrous metal debris and so far it has held up well....180*-200* constantly immersed in ATF!!  Surfaces MUST be clean as mentioned before...I'd go for it!!
BTW, it is supposed to be good to 600*F and your lifter valley should never see more than about 200*?? 
|

08-08-2010, 07:35 AM
|
CC Member
|
|
|
Join Date: Dec 2004
Location: Kansas City,
KS
Cobra Make, Engine: jbl
Posts: 2,291
|
|
Not Ranked
the epoxy i was looking at was good to 250, the jb weld 600.
i could see a vibration problem causing the stuff to crack, but wouldn't the epoxy also?
maybe i should have said i need to buy some stuff to secure some fittings in the lifter valley.....it's all in the delivery.
|

08-08-2010, 07:44 AM
|
CC Member
|
|
|
Join Date: Oct 2003
Posts: 4,078
|
|
Not Ranked
Quote:
Originally Posted by vector1
maybe i should have said i need to buy some stuff to secure some fittings in the lifter valley.....it's all in the delivery.
|
Then do some more work and make a mechanical fastener. Braze brackets to your tubes, drill and tap the valley and bolt them down with loctite. That will be a permanent installation.
__________________
Chas.
|

08-08-2010, 08:12 AM
|
CC Member
|
|
|
Join Date: Dec 2004
Location: Kansas City,
KS
Cobra Make, Engine: jbl
Posts: 2,291
|
|
Not Ranked
true, true. some of the threads on the fittings are ify so i wanted to secure them with something permanent that would help with support. i had thought about making a bracket and bolting it through the valley for support but thought as long as i was using liquid fastener i might as well use it for the support also.
they're already in now, so unless someone says definitely don't do it they stay.
|

08-08-2010, 09:29 AM
|
Senior Club Cobra Member
|
|
|
Join Date: Jul 2002
Cobra Make, Engine:
Posts: 15,712
|
|
Not Ranked
I think JB Weld on a threaded fitting is a good idea, it's a good example of where the stuff can be beneficial.
|

08-08-2010, 11:27 AM
|
CC Member
|
|
|
Join Date: Jun 2005
Cobra Make, Engine:
Posts: 3,077
|
|
Not Ranked
Not for your application but another magic bullet for gas tank, oil pan, brake reservoirs which crack or leak is SeaALL. It's about $4.00 tube.
|

08-09-2010, 05:23 AM
|
 |
CC Member
|
|
|
Join Date: Mar 2010
Location: Navarre,
FL
Cobra Make, Engine: Unique 427 S/C, 427ci
Posts: 166
|
|
Not Ranked
Quote:
Originally Posted by ERA Chas
Then do some more work and make a mechanical fastener. Braze brackets to your tubes, drill and tap the valley and bolt them down with loctite. That will be a permanent installation.
|
I agree with Chas.... do it right and forget the epoxy! If it's worth doing.... then do it right.
Mark
|

08-09-2010, 05:28 AM
|
CC Member
|
|
|
Join Date: Dec 2004
Location: Kansas City,
KS
Cobra Make, Engine: jbl
Posts: 2,291
|
|
Not Ranked
i think there is also a difference betwen the quik-set and regular stuff. quik-set tends to crack and fatigue from what i understand, regular stuff is preferred.
|

08-09-2010, 06:51 AM
|
 |
CC Member
|
|
|
Join Date: Dec 2000
Location: Central,
TX
Cobra Make, Engine: Midstates Cobra, RFGT40
Posts: 2,048
|
|
Not Ranked
As long as we are talking JB weld, I have a good one. My Dad rebuilds old tractors . He bought a John Deere M model. He rebuilt the motor and was assembling it when I noticed the exhuast manifold was broken in two. I said to him "looks like you
need a new manifold." he said, "naw, I'll just stick it together with some JB weld. I started laughing and
told him that was nuts.
A few days later I heard the tractor running. I went out. and watched. when he shut it down I looked and sure enough that old farmer stuck
the manifold together with JB. I still being the skeptic told him it would never last. Boy did I
eat those words. After five years that stuff was still holding. He sold the tractor when we moved to Texas. I bet that stuff is still holding.
I'm a believer now.
Hersh 
|

08-09-2010, 07:44 AM
|
 |
Senior Club Cobra Member
|
|
|
Join Date: Dec 2001
Location: Glendale,
AZ.
Cobra Make, Engine: Cobray-C3, The 60's body lines on todays chassis technology
Posts: 2,302
|
|
Not Ranked
Hey Hersh I can see your dad doing that, heck I can see you doing that too !
Vector, As other have mentioned making sure you have good clean surfaces is a real important step. You would not believe the things in this world with JOB Weld on or in them and I put a bunch of it there over the years. Back in my HS days I was racing a nasty little SB. Many hours of porting work done on the cast iron heads moving the runners,to the point where it had more JB than original material. Worked great.
|
Posting Rules
|
You may not post new threads
You may not post replies
You may not post attachments
You may not edit your posts
HTML code is On
|
|
|
All times are GMT -7. The time now is 05:51 AM.
|