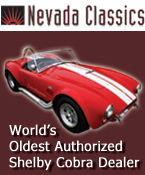 
Main Menu
|
Nevada Classics
|
Advertise at CC
|
March 2025
|
S |
M |
T |
W |
T |
F |
S |
|
|
|
|
|
|
1 |
2 |
3 |
4 |
5 |
6 |
7 |
8 |
9 |
10 |
11 |
12 |
13 |
14 |
15 |
16 |
17 |
18 |
19 |
20 |
21 |
22 |
23 |
24 |
25 |
26 |
27 |
28 |
29 |
30 |
31 |
|
|
|
|
|
|
CC Advertisers
|
|

01-30-2021, 05:27 PM
|
CC Member
|
|
|
Join Date: Mar 1999
Location: TACOMA,
WA
Cobra Make, Engine: Everett Morrision FE 427 so 2-4s
Posts: 2,025
|
|
Not Ranked
CWI JAG rear suspension parts diagram?
I have an older replica with a CWI Jaguar IRS. My problem is the outer U-joints on the half shafts. The Universal joint on both sides are enclosed in the uprights protective bell. The zerks are straight and I can't get a grease fitting to connect because of the angle and proximity to the heavy protective bell on inside of the upright housings. I need to remove the straight zerk and install an angled zerk to get access. Problem is the straight zerk is tight and I can't get on it. I think I need to separate the half shaft from the upright just long enough to swap out the zerks. I do not know exactly what I'm getting into. I'm thinking the way in is to remove the Allen headed bolt on the wheel flange and separate the upright from the half shaft. I expect some shims, but I do not know where. I'd like an exploded parts diagram or some instructions. I didn't connect to CWI are they still around or have changed their name?
__________________
Mike H
|
-
Advertising

01-30-2021, 06:02 PM
|
 |
CC Member
|
|
|
Join Date: Nov 2007
Location: Clayton,
IN
Cobra Make, Engine: ERA 838
Posts: 1,126
|
|
Not Ranked
You need to remove the upright and half shaft. I can send you a pdf of that part of the Jag manual. If you have never torn into a Jag rear it is a pretty big job.
I suggest finding a way to get the grease fitting out. You could put a lot of time in the effort and still be ahead of the game.
Alternatively, you could run it until you have a U joint issue. Because you will essentially have to tear down far enough to replace a U joint. That seem pointless to tear down that far to save a U joint. It could run for years without greasing.
John
|

01-30-2021, 06:38 PM
|
 |
Half-Ass Member
|
|
|
Join Date: Jun 2005
Cobra Make, Engine: ERA #732, 428FE (447 CID), TKO600, Solid Flat Tappet Cam, Tons of Aluminum
Posts: 22,017
|
|
Not Ranked
Or cut a small notch out of the upright that let's you get a grease fitting on to the zerk. 
|

01-30-2021, 10:46 PM
|
CC Member
|
|
|
Join Date: Mar 1999
Location: TACOMA,
WA
Cobra Make, Engine: Everett Morrision FE 427 so 2-4s
Posts: 2,025
|
|
Not Ranked
The straight zerk is pointed at tht side wall of the upright. A hole might work but it's the point. I have had the whole rear suspension out years ago to reseal the third member, Replacing the leather seals. The car was constructed in 84, I've had it since 99. Those two zerks have always been an issue. I have taken HUUMMVS front drop spindles apart when I worked and these shouldn't be much worse. I'm not planning on adjusting any shims, Just separate the half shaft from the upright housing enough to get to the zerk, I have found an allen bit to fit the bolt on the wheel flange. The seals do not leak, But then again I haven't done theses before, I should have twenty years ago.
__________________
Mike H
|

01-30-2021, 10:58 PM
|
CC Member
|
|
|
Join Date: Mar 1999
Location: TACOMA,
WA
Cobra Make, Engine: Everett Morrision FE 427 so 2-4s
Posts: 2,025
|
|
Not Ranked
It looks to me that the large Allen headed bolt is the key. I remove that bolt and the wheel flange and the upright should lean outward and away from the half shaft exposing the zerk.
__________________
Mike H
|

01-31-2021, 02:16 PM
|
CC Member
|
|
|
Join Date: Mar 1999
Location: TACOMA,
WA
Cobra Make, Engine: Everett Morrision FE 427 so 2-4s
Posts: 2,025
|
|
Not Ranked
I ordered that adapter, should have it by Saturday. I wish the original builder had caught this back when. I have replaced a lot of zerks to over come just this stuff back when I was working. I think a 45° zerk would have made this a non issue. I can see that when installing the straight zerk in the U-joint before the assembled half shaft was installed in the upright with it's protective bell. My right knee is in need of a rest so I'll wait.
__________________
Mike H
|

02-07-2021, 06:45 AM
|
CC Member
|
|
|
Join Date: Mar 2013
Location: Lewes,
DE
Cobra Make, Engine: ERA #448, 1964-427
Posts: 111
|
|
Not Ranked
Greetings All,
I'm in the same situation, almost, as Michael Henry. Except, the 45 degree part of jerk fitting broke off the u-joint under the upright. I was able to unscrew the jerk body from the u-joint. My problem now, I'm unable to thread the new zerk fitting back into the u-joint, I can't get the threads started with my fat fingers. Any suggestions would be great. Thanks, Art Fink
|

02-07-2021, 11:51 AM
|
CC Member
|
|
|
Join Date: Mar 1999
Location: TACOMA,
WA
Cobra Make, Engine: Everett Morrision FE 427 so 2-4s
Posts: 2,025
|
|
Not Ranked
I didn't have much room to do much with the new 45° zerks as they have a 3/8" hex body even with the half shaft partially separated. The puller legs bolt to the wheel flange studs ans the threaded screw shaft pushes against the tip of the half shaft. The puller did it's part it started the upright with it's wheel hub moving and made an ideal handle to push the upright down further down. I didn't take the fulcrum apart, it was stiff. My sway bar was connected to my lower support arm and not the aluminum upright. How much of the zerk broke off? Was it the zerk tip or did the body break off the 1/4" x 28 threads? My half shaft was anchored into the wheel flange with a large Allen bolt. It took about all my old impact would do to break it loose. Weather your Jag is held together with a Allen bolt like mine or the large castellated nut with a cotter pin, I'm betting you'll have to take it apart like I did. What do you think got in to the zerk to break it in the first place? The "True Power" puller I bought was a good value but there are more expensive pullers available. Are you going to do it yourself or take it to a shop? I see an equipped shop taking two hours or so if that castellated nut comes apart with out a lot of trouble.. IF this or that? Is there anything else you might want to take care of while you are in there? I was a heavy equipment mechanic and swapped a lot of zerks as if I was going to be the next guy to half to work this vehicle again. There are some differences in zerks. I chose a zerk that had more hex body to get a wrench on. It had shorter threads but over all length was the same. I used a local hydraulic supply store that makes hoses and such. If there is a fitting I'd need ?, they'd have it. The zerk I bought was in a bin that must have been the last of a style they had and they could not identify its part number or price. I'm sure I got a deal at $1 each.
__________________
Mike H
Last edited by Michael C Henry; 02-07-2021 at 11:56 AM..
|

02-08-2021, 07:13 AM
|
CC Member
|
|
|
Join Date: Mar 2013
Location: Lewes,
DE
Cobra Make, Engine: ERA #448, 1964-427
Posts: 111
|
|
Not Ranked
Greetings Michael, This zerk was the last one I greased, I was able to grease the u-joint, but when I pulled the grease gun nozzle off of the fitting the 45 degree part pulled out of the fitting body. It looks like the threads had been stripped as there were no threads left. In hind sight, I should have just tapped the broken piece back into the other part and be done. The car will never need grease for another 20 years. But, now I need to fix the problem. I take it that, moving the axle and lowering the upright is a problem and needs a puller of some sort? I was hoping to unbolt the axle and pull the upright down enough for room to screw the new zerk into the u-joint. Am I getting in over my head? Thanks for your help...................Art
|

02-08-2021, 12:24 PM
|
CC Member
|
|
|
Join Date: Mar 2013
Location: Lewes,
DE
Cobra Make, Engine: ERA #448, 1964-427
Posts: 111
|
|
Not Ranked
Update on Zerk Fitting Problem
Greetings Michael, I have solved my zerk fitting problem after sleeping on it. I threaded a paper/wire bread bag tie through the new zerk fitting body leaving about 1/4" exposed at the threaded end and forming a tee configuration at the top. Stuck the short end into the hole in the u-joint which kept it straight and even with the hole. I was able to start the treads with my 2 fat fingers. At that point, I was able to snug it up with an open-end. I then pulled the paper/wire out of the fitting body and screwed the 45 degree part into the fitting body. It saved me a lot of time and a big headache. Thanks for all your help and information. Art Fink
|

02-08-2021, 12:59 PM
|
CC Member
|
|
|
Join Date: Mar 1999
Location: TACOMA,
WA
Cobra Make, Engine: Everett Morrision FE 427 so 2-4s
Posts: 2,025
|
|
Not Ranked
You now have something in the hole to keep dirt out. The original hole was a 1/4" x 28 thread with a taper like pipe thread. You have to be careful that as you screw in, you can only advance into the hole. You have to keep asking yourself will it go another turn. The threads on the male portion will get compressed and if you back it up, it will not be as tight. So once it's at the optimum angle and reasonably tight, STOP. Back when, the shop had a product called "LEAK LOCK" a powder blue squeeze tube of goo. It dos exactly what the name says. Getting the part out will be a problem without a torch.
__________________
Mike H
Last edited by Michael C Henry; 02-08-2021 at 01:02 PM..
|

02-08-2021, 01:29 PM
|
CC Member
|
|
|
Join Date: Mar 1999
Location: TACOMA,
WA
Cobra Make, Engine: Everett Morrision FE 427 so 2-4s
Posts: 2,025
|
|
Not Ranked
My wheel flanges have the GM style 5 lug x 5 inch pattern with treaded wheel studs. The wheel flange and the tip of the half shaft were held together with an large fine thread Allen headed bolt. So my puller attached to three of the threaded studs of the wheel flange. My wheels are PSE aluminum with fake knockoffs. Black centers with polished outer rims and knockoffs. I have to remove the fake knock off before unbolting the wheel. The counter sunk screw that keeps the fake knock off on the wheel is hidden behind one of the three knockoff wings. Looks good but not quick to R&R a wheel.
__________________
Mike H
|

02-10-2021, 07:51 PM
|
CC Member
|
|
|
Join Date: Mar 2013
Location: Lewes,
DE
Cobra Make, Engine: ERA #448, 1964-427
Posts: 111
|
|
Not Ranked
Michael, FYI, I used a brass zerk fitting, not sure if that is better than a steel one. When I tightened the fitting I went a quarter turn past the favorable grease gun angle, to be snug. My plan, next time I grease that u-joint, I'll back it out quarter turn, squeeze in the grease and then retighten the quarter turn. This job could have been a real horror show.
Best of luck with your project, Art Fink
|

02-11-2021, 05:25 AM
|
CC Member
|
|
|
Join Date: Mar 1999
Location: TACOMA,
WA
Cobra Make, Engine: Everett Morrision FE 427 so 2-4s
Posts: 2,025
|
|
Not Ranked
Never had any experience with brass zerks. I think you traded corrosion resistance for strength.. If you did this without separating the wheel flange and half shaft. That is an accomplishment. Even with the separation getting the new angled zerk started and then tightening it was a bear of a job for me. The angled zerks have a 3/8" hex body and swinging a 3/8" open end wrench was tedious. The larger hex body zerk I used let me get an off angle bite. It now can be greased even with the wheels on. Lots better than the 37 years since it was originally put together.
__________________
Mike H
|

02-11-2021, 01:06 PM
|
CC Member
|
|
|
Join Date: Mar 2013
Location: Lewes,
DE
Cobra Make, Engine: ERA #448, 1964-427
Posts: 111
|
|
Not Ranked
Michael, glad to hear you're back in business after the hassle you went through. I was definitely lucky with mine. The broken fitting came loose with a 3/8 box wrench (thank you ERA for not over torquing that badboy), I was able to unscrew with a short socket, just enough room to do. The "Cobra Gods" were watching over me that day, as the new fitting threads caught rather easily and I was golden.
Enjoy the Ride............Art Fink
|

02-11-2021, 09:10 PM
|
CC Member
|
|
|
Join Date: Mar 1999
Location: TACOMA,
WA
Cobra Make, Engine: Everett Morrision FE 427 so 2-4s
Posts: 2,025
|
|
Not Ranked
I now have dark grease smears on the out side of the car and I'm out of paper towels. It is about freezing here and snowing which is rare this side of the mountains. I have gotten older and fatter with replaced right knee and hip. So getting in and out are not as they once were. A quick release steering wheel hub is the next thing. I have already bought the 9 bolt Flash Power flat 15" riveted wooden steering wheel and their adapter to go from 9 to 6 bolt pattern. with their horn button. I have gotten interested in IDIDIT's Quick Release Steering Hub. It is a spline connection with a dead spline for return to zero. They announced they had an internal horn electrical connection at the SEMA show in 2019. IDIDIT has not responded this last week about the horn thing. I'm kind of hung on this point. I do not want NRG hub, as I see them having a short life getting loose by their design. IDIDIT's local dealer is a shop for rice burners so I'm on my own.
__________________
Mike H
|
Posting Rules
|
You may not post new threads
You may not post replies
You may not post attachments
You may not edit your posts
HTML code is On
|
|
|
All times are GMT -7. The time now is 11:45 PM.
|