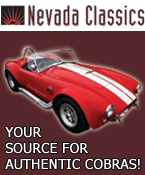 
Main Menu
|
Nevada Classics
|
Advertise at CC
|
February 2025
|
S |
M |
T |
W |
T |
F |
S |
|
|
|
|
|
|
1 |
2 |
3 |
4 |
5 |
6 |
7 |
8 |
9 |
10 |
11 |
12 |
13 |
14 |
15 |
16 |
17 |
18 |
19 |
20 |
21 |
22 |
23 |
24 |
25 |
26 |
27 |
28 |
|
|
CC Advertisers
|
|

01-16-2004, 06:58 AM
|
 |
Renegade Nuns on Wheels
|
|
|
Join Date: Aug 2001
Location: columbus,
Oh
Cobra Make, Engine: Unique 427 roadster with 351C-4B
Posts: 5,129
|
|
Not Ranked
Brake Worksheet
Through my long and tedious process (not to mention ongoing) of brake upgrades and redesigned I have picked up a LOT of good information and have had some excellent help from some of our foremost experts.
I have compiled every little formula required to design a braking system and analyze the impact of change on an existing braking system. I have put some of that information in a Excel spreadsheet that I am prepared to share.
This is the FIRST itteration of the spreadsheet. As time goes by there will be MUCH more functionality added, help, nice graphs, more user friendly, etc. Currently it takes into account everything from aerodynamic forces and centers of gravity to surface/tire grip and gives pressures and sizes for master cylinder and allows you to play with EVERY variable from disc size to caliper size to peddle effort and lever ratio and tire size, etc, etc, etc.
If you would like a copy for your amusement or to actually use, drop me an email and I will send a copy off!
Rick
|
-
Advertising

01-16-2004, 07:57 AM
|
CC Member
|
|
|
Join Date: Dec 2001
Location: Louisville,
KY
Cobra Make, Engine: I'm Cobra-less!
Posts: 9,417
|
|
Not Ranked
Great looking spreadsheet Rick....thanks a lot. This looks a lot like the stuff I had to do in engineering school....hehehe....lots of fluids and dynamics....
|

01-16-2004, 08:12 AM
|
 |
Renegade Nuns on Wheels
|
|
|
Join Date: Aug 2001
Location: columbus,
Oh
Cobra Make, Engine: Unique 427 roadster with 351C-4B
Posts: 5,129
|
|
Not Ranked
Thanks. I know it is really poorly laid out at this point. I want to take it a LOT further and maybe even develope a commercial brake program.
Engineer eh....... do you know the formula for calculating disipation of heat for ferious and non-ferious metals? I can calculate the temperature rise but do not have the formula for heat disapation. Many variables here so assumptions would ahve to be made. But I can give a worst case scenerio and then the user could go from there.
Any one have telemetry data for a popular road course from a Cobra? Rate of deceleration and speeds? How about I cook up a portion of the sheet that gives expected brake temperatures for a road course?
I need to retire
Rick
|

01-16-2004, 08:23 AM
|
CC Member
|
|
|
Join Date: Dec 2001
Location: Louisville,
KY
Cobra Make, Engine: I'm Cobra-less!
Posts: 9,417
|
|
Not Ranked
Rick, you an engineer too? Since you have AEP on your email addy, you a EE?
Disipation of heat for ferrous and non-ferrous...hmmm...Let me see if I can find something in my Heat Transfer book. If I can remember, there's a lot of variables in such as air flow, area, source of heat, etc. May not be as easy as one formula.....
|

01-16-2004, 08:28 AM
|
Banned
|
|
|
Join Date: Oct 2003
Location: Yorba Linda,
CA
Cobra Make, Engine: SPF w/392CI stroker
Posts: 3,293
|
|
Not Ranked
How about sharing with us some of the highlights in text format here? Are there specific brake line diameters that work best? Which size rotors front and back? Who makes the best calipers? I also know a thing or two (experience) about ceramic brake pads...I'm sure some would like to hear about those, too.
Thanks!
-Deano
|

01-16-2004, 08:31 AM
|
 |
Renegade Nuns on Wheels
|
|
|
Join Date: Aug 2001
Location: columbus,
Oh
Cobra Make, Engine: Unique 427 roadster with 351C-4B
Posts: 5,129
|
|
Not Ranked
Good guess but no, not an engineer. I write software, primarily on the mainframe. I don't expect it to be able to do it on one formula on a spreadsheet but that is OK. After I get every thing I want on there then I will begin making it look better and easier to use. Then I will hide all the interim results on another page or something. In the mean time, I use those results so that I can manually verify them.
That would be great if you look the formulas up. I know the rise in temperature formula was very simple. Seems to me it involved only the amount of kinetic energy to be absorbed and mass.
Thanks
Rick
|

01-16-2004, 08:40 AM
|
CC Member
|
|
|
Join Date: Dec 2001
Location: Louisville,
KY
Cobra Make, Engine: I'm Cobra-less!
Posts: 9,417
|
|
Not Ranked
Well, this is how I would look at the rate of heat transfer or disipation. You're referring to how the heat transfers between brake pads and rotors, correct?
If that's the case (if not, just tell me), then you have to look at two cases....1. You have heat transfer between the pad and the rotor...conduction. 2. You have heat transfer from air flow over the pads and rotors....convection.
Before I go any further, is this what you're talking about?
|

01-16-2004, 08:52 AM
|
 |
Renegade Nuns on Wheels
|
|
|
Join Date: Aug 2001
Location: columbus,
Oh
Cobra Make, Engine: Unique 427 roadster with 351C-4B
Posts: 5,129
|
|
Not Ranked
See what I mean, I am NOT an engineer! What would be of interest to me is the transfer of heat from the pad to the rotor and from the rotor to the air mass.
Brings up some interesting thoughts. If the pad and the rotor turn kinetic energy into heat, does the temperature rise at the same rate. I would think not because of mass but I would also think that material difference would be a factor. Then of course you would think that they would loose heat at a different rate. Then each would have a different begining temperature each time.
I guess what I am REALLY interested in is pad temperature. This of course to use as a guide for pad selection.
I have a convection oven, is this related
Rick
|

01-16-2004, 09:15 AM
|
CC Member
|
|
|
Join Date: Dec 2001
Location: Louisville,
KY
Cobra Make, Engine: I'm Cobra-less!
Posts: 9,417
|
|
Not Ranked
Well, I can give you formulas for deriving pad temperature based on heat transfers in both accounts like I described earlier.
q'' = convective heat flux
h = heat transfer coefficient (you will need these for the various materials you're anticipating using....i.e. material for rotors, and the material for the pads.
t=thickness of pad
k = thermal conductivity ( you will need to find this also for the various materials)
Tp = Temp of pad
Tinf = Temperature infinity....i.e. temp of ambient air
A = area of pad. This will be a doozy to find out....each pad will be different...you might just wanna use a general catch-all number for all pads...maybe a general area for single piston calipers, one for dual piston, one for quad piston...etc....
Now with that being said, total heat flux will be the sum of the conduction between the metals, and the convection between the metals and the ambient air.
So if you focus on the pad, you can generalize that on one side of the pad during braking contact, you will have conduction heat transfer from the pad to the rotor....and there will also be air flowing around the caliper and part of the pad itself.
qtotal = (k(Tp-Tinf))/t) + hA(Tp-Tinf)
That's gonna be as close as I can get ya without some deeper analysis of piston diameters, air flow, etc....
q should come out in W....
What I haven't stated from the beginning is that you're gonna need some sample temperatures to get you started....because you have basically two unknowns.....the heat flux (q) and the pad temperatures. You can probably get some sample values of each and interpolate.
I know this is as clear as mud...I'm doing the best I can...it's been like almost 3 years since I've had this course...and like almost everything else, you don't use it after you take it in class.
I'll try to help you as much as I can...let me know if you have any questions...I'll try to explain what I did....
|

01-16-2004, 09:25 AM
|
CC Member
|
|
|
Join Date: Dec 2001
Location: Louisville,
KY
Cobra Make, Engine: I'm Cobra-less!
Posts: 9,417
|
|
Not Ranked
I basically forgot one key step....the heat generation comes FROM the rotor to pad relationship....that changes things a little...I told you that I was rusty....
Heat energy is generated from pad to rotor contact, and is disipated through air to pad relationship....
You can think of it as overall energy balance...
Ein - Eout = 0
qconduction - qconvection = 0
qconduction = qconvection
So using the rambling from the previous post,
(k(Tp-Tinf))/t) = hA(Tp-Tinf)
This takes the heat flux variable out of it, and will allow you to concentrate on temps... you can solve for Tp.
|

01-16-2004, 09:27 AM
|
CC Member
|
|
|
Join Date: Dec 2001
Location: Louisville,
KY
Cobra Make, Engine: I'm Cobra-less!
Posts: 9,417
|
|
Not Ranked
hehehe....one more thing....the heat generation from the pad/rotor contact should be halved, since you will have two pads splitting the heat generation.
Man, I should have never opened my mouth....heheheh
|

01-16-2004, 09:44 AM
|
 |
Renegade Nuns on Wheels
|
|
|
Join Date: Aug 2001
Location: columbus,
Oh
Cobra Make, Engine: Unique 427 roadster with 351C-4B
Posts: 5,129
|
|
Not Ranked
Wow! I never thought to get such a quick answer! Excuse me while I print this out and try and absorb the information! Hopefully I will put this to good use some day.
Thanks for the information.
Rick
|

01-16-2004, 09:44 AM
|
CC Member
|
|
|
Join Date: Dec 2001
Location: Louisville,
KY
Cobra Make, Engine: I'm Cobra-less!
Posts: 9,417
|
|
Not Ranked
<---------------- Tinf (Air Flow)
_________T2________
| |
-------------------------------
Tp
Rotor Side
(K(Tp-T2))/t = h(T2-Tinf)
Again, you would have to know the temp of the pad closest to the air flow....
Solving for Tp.....
Tp = (ht(T2-Tinf)+T2)/k
On the flip side, if you know how much heat is generated (from where you convert kinetic to thermal energy, friction b/t pad and rotor), and you know the temp of the pad on the piston side, you can use:
q = (k(Tp-T2))/t.....where q is the heat generated from kinetic to thermal energy.
Either way, you're gonna have to get some sample temps or assume temperatures.
|

01-16-2004, 09:53 AM
|
 |
Renegade Nuns on Wheels
|
|
|
Join Date: Aug 2001
Location: columbus,
Oh
Cobra Make, Engine: Unique 427 roadster with 351C-4B
Posts: 5,129
|
|
Not Ranked
The formula I do have calculates the rise in temperature using kinetic energy (which I can calculate) and mass. How does that come into play?
Rick
|

01-16-2004, 10:07 AM
|
CC Member
|
|
|
Join Date: Dec 2001
Location: Louisville,
KY
Cobra Make, Engine: I'm Cobra-less!
Posts: 9,417
|
|
Not Ranked
That's awesome then....when you look at a heat transfer balance, there's a fine line between temperatures. If you look at the thickness of a brake pad, one side should be a lot hotter than the other. That side of course would be the rotor side. The other side, which is exposed to air, would of course be cooler. So if your formula's solution is the temperature of the rotor side, then you can just plug and chug into my formula from above. Using the assumption that the part of the pad touching the rotor would be equal to the temperature of the rotor, and that heat is transferred through the thickness of the pad to the air that is flowing over it....you can solve the above formula for T2 (which is the temp of the pad facing the piston)....
(k(Tp-T2))/t = hA(T2-Tinf)
(k(Tp-T2))/t = hAT2 - hATinf
k(Tp-T2) = hAtT2 - hAtTinf
kTp-kT2 = hAtT2 - hAtTinf
kTp = hAtT2 - hAtTinf + kT2
kTp + hAtTinf = hAtT2 + kT2
kTp + hAtTinf = hAtT2 + kT2
kTp + hAtTinf = T2 (hAt + k)
T2 = (kTp + hAtTinf)/(hAt +k)
So you just plug your temperature result from your formula into Tp...Tinf would be the temperature of ambient air, you'll have to find h & k from a chart somewhere, A is the area of the pad, t is the thickness of the pad....and boom....you have the temp of the pad on the piston side.
Given that heat flux through the pad....once you know the temperature of each side, I can give you another formula will can show the temperatures at any point (x) in the pad...so you can see where the heat is the highest.....my guess is it would be highest right at the rotor, and then taper off through the cross section of the pad.
I'm sorry for all the babbling....like I said, I'm having to remember this as I go...it's been awhile. But the above stuff should get you going. Oh yeah, temperatures are in Kelvin.... h is in W/m^2 and k is in W/m*K.
|

01-16-2004, 10:19 AM
|
 |
Renegade Nuns on Wheels
|
|
|
Join Date: Aug 2001
Location: columbus,
Oh
Cobra Make, Engine: Unique 427 roadster with 351C-4B
Posts: 5,129
|
|
Not Ranked
T2 = (kTp + hAtTinf)/(hAt +k)
There is it! Kelvin, good to know! I have already dropped a note to a tech guy at Wilwood to find out h & k.
Still have to digest this quite a bit. But I know who to contact when the time comes!
Thanks
Rick
|

01-16-2004, 10:45 AM
|
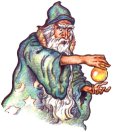 |
Senior Club Cobra Member
|
|
|
Join Date: Jun 1999
Location: Fallbrook, CA USA,
CA
Cobra Make, Engine: Porsche 928 S4
Posts: 739
|
|
Not Ranked
Hi Guys,
blykins said,
“Heat energy is generated from pad to rotor contact, and is disipated through air to pad relationship....”
This correct in part, however very little heat is dissipated directly from the pad to the air. The exposed surface area of the pad to the air stream is minimal at best. Rather the pad is an ablative material and most of the heat generated in pad is removed from the system by ablation.
(This is why pads are made certain sizes. A small pad will input just as much heat to the system as a large one, but it will ablate much quicker. This is the reason for 6 and 8 piston calipers. You increase the pad area to allow for this ablation and you have support this pad. Therefore, more pistons are needed to apply even force to the area. You do not increase clamping force with more pistons.)
Heat generated by the pad is typically transferred to the rotor. (Hopefully this transfer is at a rate greater than thermal conductivity rate of the pad material, Otherwise, one starts heating the pistons and therefore the fluid. )
Also, don’t forget coefficient of friction of the pad. Remember that this number is dependant on the temperature of the pad.
One must now start delving into integration.
If you really want to get confused, try running the numbers on carbon brake units. They are pure ablative systems. Less than 5% of the heat generated is stored in the system. As opposed to 65>80% in an iron/ablative system.
Brake thermodynamics are really quite complex and are really beyond my math capabilities. One of best friends and long time associates is my brake guru. He is physicist and holds many patents on brakes and brake materials. And the subject still is a bit of a black art to him when it comes heat transfer and optimal design of caliper and rotor systems.
|

01-16-2004, 11:10 AM
|
 |
Renegade Nuns on Wheels
|
|
|
Join Date: Aug 2001
Location: columbus,
Oh
Cobra Make, Engine: Unique 427 roadster with 351C-4B
Posts: 5,129
|
|
Not Ranked
I thought this might get your attention Richard. "ablation", had to look it up! Just something to keep me out of trouble. I was kicking around a device that would automatically compensate for bouyancy changes in compressed gas cylinder that could be added on to existing systems, be simple, reliable and cheap. Got bored. So now it is brakes!
Anyways, so the rotor acts main method of ridding the system of heat? In the most simplistic terms the rotor, by design and relationship to the air flow, cools faster and as the temperatures between the rotor and pad attempt to equalize thermal energy is transfered to the rotor and then disappated? Some where in the ball park?
Rick
|

01-16-2004, 11:22 AM
|
CC Member
|
|
|
Join Date: Dec 2001
Location: Louisville,
KY
Cobra Make, Engine: I'm Cobra-less!
Posts: 9,417
|
|
Not Ranked
Well in that case....
If you wanted to know the pad temperatures, Rick...I would assume like before that the pad temperature at the contact patch would be the temperature of the rotor at that patch....We could assume no heat transfer due to air movement, and I could still give you a formula to find the cross-sectional pad temperatures.
Given what Richard has explained to us, heat is disipated through the rotors....so if your formula has the max temperature of the rotor, then this is a convection heat transfer from air to rotor.
q(local heat flux) = hA (Trotor - Tinf)
One could assume that both sides of the rotor get air contact, so the A in the above equation would relate to the area of the rotor *2.
So how are you going to continue now, Rick? You gonna base your experiments on pad heat and then rate of rotor heat transfer? Those seem like two good spots to focus on...Of course you don't want to burn up your pads...and it just makes sense that the bigger the rotor, the more braking and cooling you could get.
|

01-16-2004, 11:31 AM
|
 |
Renegade Nuns on Wheels
|
|
|
Join Date: Aug 2001
Location: columbus,
Oh
Cobra Make, Engine: Unique 427 roadster with 351C-4B
Posts: 5,129
|
|
Not Ranked
Quote:
Originally posted by blykins
You gonna base your experiments on pad heat and then rate of rotor heat transfer?
|
That seems logical to me. Is it fair to assume that the drop in temperature of the rotor will be closely followed by the pad temperature? This may already be explained in the formulas but I have yet to digest them.
Rick
|
Posting Rules
|
You may not post new threads
You may not post replies
You may not post attachments
You may not edit your posts
HTML code is On
|
|
|
All times are GMT -7. The time now is 03:20 PM.
|