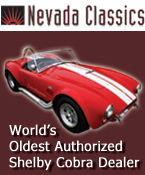 
Main Menu
|
Nevada Classics
|
Advertise at CC
|
January 2025
|
S |
M |
T |
W |
T |
F |
S |
|
|
|
1 |
2 |
3 |
4 |
5 |
6 |
7 |
8 |
9 |
10 |
11 |
12 |
13 |
14 |
15 |
16 |
17 |
18 |
19 |
20 |
21 |
22 |
23 |
24 |
25 |
26 |
27 |
28 |
29 |
30 |
31 |
|
|
CC Advertisers
|
|

03-19-2009, 06:31 PM
|
CC Member
|
|
|
Join Date: May 2006
Location: St. Louisville,
Oh
Cobra Make, Engine: A&C 67 427 cobra SB
Posts: 2,445
|
|
Not Ranked
converting slip joint to flange on side pipes
My headers and side pipes fit together with slip joints. They rattled and leaked. As suggest here I am in the process of converting to flanges.
I made 4 flanges out of 3/8" thick plates. OD of header pipes is 2.005" and OD of side pipes is 2.190." On the side pipes flange, I left 3/16" of meat at the tightest point between the pipes, so there was something to weld to and there will be a seal between the pipes, when I'm done. The pipes were spaced about 1/16" apart before I started. So I did change this spacing.
Now the headers are made with the front two cylinders on one short flange, and the back two cylinders are on a different flange. In other words, the headers are two parts per side.
My plan was to slip the plates on the side pipes. Slip both header halfs into that flange plate. Then slip them together, as they were originally designed. Then I was going to aligne the head flanges to the gasket and clamp to a straight edge. The idea was to get everything aligned up and tack the headers to the flange. Well with the flange plates in place it is difficult to slip it all together, and not possible to pull the head flanges into position to aligne it with the gaskets.
Any body have suggestions on the best way to make sure my side pipes line up correctly after I get it all welded together?
I'm thinking I will have to cut the header tubes off flush to where they would but up to the side pipes rather than slip in. But how do you get the flange plates all perfectly square?
Last edited by olddog; 03-19-2009 at 06:40 PM..
|
-
Advertising

03-19-2009, 06:48 PM
|
CC Member
|
|
|
Join Date: Mar 2004
Location: Haughton,
LA
Cobra Make, Engine: ERA234 427s/o toploader
Posts: 242
|
|
Not Ranked
Olddog,
Did you ever get the F.I. tweaked to your satisfaction? Kind of Interested in the old girl.
Toby
__________________
.....oil dry magnate!
|

03-19-2009, 07:21 PM
|
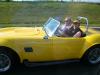 |
Senior Club Cobra Member
|
|
|
Join Date: May 2001
Location: Florence,
AL
Cobra Make, Engine: RCR GT 40 & 1966 Fairlane 390 5 speed
Posts: 4,511
|
|
Not Ranked
Before you remove your slip pipes, drill two small holes in two of the tubes. Then you can remove the headers and side pipes, put them together, using the small holes to aline. Mark you cut lines onto the pipes. Cut (Porto-band saw) thru all of the tubes. If you cut the pipe a little crooked you can grind it or hide it in the flanges. Slip your flanges onto the pipes and bolt together. Square (framing square or small speed square) the flanges with the pipes. Tack weld, one small spot on each tube, maybe two. Check everything. You could install the header with two bolts into the head. Test fit the side pipe. Then remove everything and finish the welding. If you use MiG then preheat pipes to 400 degrees. The best for exhaust pipe is Tig weld. So I have been told.
Dwight
__________________
''Life's tough.....it's even tougher if you're stupid.'' ~ John Wayne
"Happiness Is A Belt-Fed Weapon"
life's goal should be; "to be smarter than inanimate objects"
Last edited by Dwight; 03-19-2009 at 07:23 PM..
|

03-19-2009, 07:29 PM
|
CC Member
|
|
|
Join Date: May 2006
Location: St. Louisville,
Oh
Cobra Make, Engine: A&C 67 427 cobra SB
Posts: 2,445
|
|
Not Ranked
Quote:
Originally Posted by Toby
Olddog,
Did you ever get the F.I. tweaked to your satisfaction? Kind of Interested in the old girl.
Toby
|
No. I'm still debating which way to go. I like the TWEECER but the cost is fairly high compared to just letting MassFlow chip it. I'm a little reluctant to spend money in this economy.
I did play around with the fuel pressure to get it to idle better cold. Rebuilt the fuel pressure regulator, as it wasn't holding vacuum - leak. I couldn't find anything wrong with the parts I took out.
I let it idle until warmed up, and then pulled it on the ramps and changed the oil. Then pulled the plugs before removing the headers and side pipes. The pluggs were black and sooty. I'm quite sure the EFI would do better if it was told about all the modifications made to the engine.
The biggest thing I did was the intake was sucking in oil and got oil up on the flow meter. The intake ports were shifted off center of the bolt holes on one side and quite smaller than the gaskets. I port matched it up to the gaskets. The heads were already perfectly matched to the gaskets. The fuel injection bungs were partially blocked by the welds. I machined them back out. I also polished the inside of the intake while it was off. Lets see the four end bolts were bottoming out before they tighten - I think that caused the leak. I tapped the heads and re-did the heli-coils. Oh yea I put a windage tray in it and welded the oil pan while I was at it. Felt like I picked up 50 hp after all of that above. However I think the oil on the flow sensor may have shifted its calibration some, even though I cleaned it.
Don't get me wrong, it runs decent as it is. I think there is still another 50 hp to be had with better tuning.
Buy the way, was the heads ported? They looked very nice and intake and exhaust match gaskets perfectly. I doubt they come out of the box that good.
|

03-19-2009, 07:44 PM
|
CC Member
|
|
|
Join Date: May 2006
Location: St. Louisville,
Oh
Cobra Make, Engine: A&C 67 427 cobra SB
Posts: 2,445
|
|
Not Ranked
Quote:
Originally Posted by Dwight
Before you remove your slip pipes, drill two small holes in two of the tubes. Then you can remove the headers and side pipes, put them together, using the small holes to aline. Mark you cut lines onto the pipes. Cut (Porto-band saw) thru all of the tubes. If you cut the pipe a little crooked you can grind it or hide it in the flanges. Slip your flanges onto the pipes and bolt together. Square (framing square or small speed square) the flanges with the pipes. Tack weld, one small spot on each tube, maybe two. Check everything. You could install the header with two bolts into the head. Test fit the side pipe. Then remove everything and finish the welding. If you use MiG then preheat pipes to 400 degrees. The best for exhaust pipe is Tig weld. So I have been told.
Dwight
|
Thanks that gives me some ideas.
|

03-20-2009, 02:44 PM
|
CC Member
|
|
|
Join Date: Mar 2004
Location: Haughton,
LA
Cobra Make, Engine: ERA234 427s/o toploader
Posts: 242
|
|
Not Ranked
Olddog,
I know the ports were matched, but I have no evidence that it was more than port deep. As you know, those heads were little better than factory, except for being aluminum. If you were to really open them up that cam would match better. That guy from mass- flo told me the cam overlap is holding back the F.I. in its present state of tune. Who knows, If you ported and polished the heads where they picked up another 100 CFM that may be all it takes. BTW, those KCR stage 1 heads really woke up my FE.
Toby
__________________
.....oil dry magnate!
|

03-20-2009, 04:37 PM
|
CC Member
|
|
|
Join Date: Jan 2005
Location: Hillsboro,
OR
Cobra Make, Engine: Scratch built CSX style frame, Carbon fiber body, 393 Stroker, T-bird IRS, T5
Posts: 1,623
|
|
Not Ranked
Agree with the above, but after tacking everything together on the outside tubes at the flange, weld the pipes on the inside of the flanges and grind the weld down when you're done. Much cleaner job when you are done and you can grind off the outside tack welds with a die grinder and really clean it up.
Bob
|

03-20-2009, 09:34 PM
|
CC Member
|
|
|
Join Date: Nov 2007
Cobra Make, Engine:
Posts: 327
|
|
Not Ranked
Olddog, you better make sure after you get your headers fixed the way you like it, your gunna have some big time vibration issues, you need to make sure your side pipe mounts where they mount on the frame, have a rubber isolater, to help with the vibration , if not your gunna start cracking things.So what I am telling you is the slip fit do leak a little, but they flex, and give you some leeway, now you have taken that away. If you guys agree chime on in.
|

03-21-2009, 09:00 AM
|
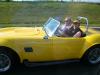 |
Senior Club Cobra Member
|
|
|
Join Date: May 2001
Location: Florence,
AL
Cobra Make, Engine: RCR GT 40 & 1966 Fairlane 390 5 speed
Posts: 4,511
|
|
Not Ranked
All the Unique that I have worked on have 2 solid mounts on the side pipe to frame on each side. I don't think they have a problem with cracks. I like to use one mount on the rear of the side pipe with a Mustang style rubber mount. I think it flexes better without breaking something. I have installed flanges on E-Ms and Shell Valleys. I have never seen a slip joint that did not leak.  Maybe if you run it rich till they seal up that would work. 
We have tried a lot of different sealers on slip joint with little success.
got to go Coach just call and he is on his way to pick me up in his Coupe! road trip 
Dwight
__________________
''Life's tough.....it's even tougher if you're stupid.'' ~ John Wayne
"Happiness Is A Belt-Fed Weapon"
life's goal should be; "to be smarter than inanimate objects"
|

03-21-2009, 10:56 AM
|
 |
CC Member
|
|
|
Join Date: May 2001
Location: California,
Ca
Cobra Make, Engine: NAF 289 Slabside Early Comp Car with 289 Webers and all the goodies. Cancelling the efforts of several Priuses
Posts: 6,592
|
|
Not Ranked
Quote:
--------------------------------------------------------------------------------
Olddog, you better make sure after you get your headers fixed the way you like it, your gunna have some big time vibration issues, you need to make sure your side pipe mounts where they mount on the frame, have a rubber isolater, to help with the vibration , if not your gunna start cracking things.So what I am telling you is the slip fit do leak a little, but they flex, and give you some leeway, now you have taken that away.
|
Believe it!
__________________
Rick
As you slide down the Banister of Life, may the splinters never be pointing the wrong way
|

03-21-2009, 11:52 AM
|
CC Member
|
|
|
Join Date: Mar 2006
Cobra Make, Engine:
Posts: 75
|
|
Not Ranked
Slip joint & Flanges
Olddog,
You can do it. The flanges should be 1/4". 3/8" is to heavy and will cause alot of unnecessary weight and vibration on the headers. 3/8th is good for the header flange at the head. Take your headers appart at the slip joint and slip on your flanges leaving an 1/8" between the flange and the pipe.(believe me you will need that much room) Bolt every thing back on the car, bolt the flanges together. Tack weld the pipe to the flange accordingly. Now square things up and burn it in. Use some good welding blankets so you don't burn your car up. Another concern is the torque on your motor. With your headers solid to your motor and frame, the torque will cause problems. If you are running stock ford mounts drill 2 holes through each one and put 5/16 grade 8 bolts through them, you will eliminate torque over but retain vibration dampening.
Good luck.
|

03-22-2009, 07:28 PM
|
CC Member
|
|
|
Join Date: May 2006
Location: St. Louisville,
Oh
Cobra Make, Engine: A&C 67 427 cobra SB
Posts: 2,445
|
|
Not Ranked
I put the flange plates on the side pipes and then leveled the tops of the side pipe tubes with a die grinder. With the new flange plates slipped on the side pipes, I assemble everthing on the car. Buy this I mean I put it together with the slip joints. Then I used a sharpy to mark the headers. Then removed headers and side pipes.
The cutoff saw was not able to make a perfect cut, so we cut the headers 1/8" long. Next we bolted the headers onto a 351W on an engine stand and rotated the engine to an easy to work position. Aligned the flanges to the marks. Then welded the flange to the headers. Ground the pipes off flush to the flange plate.
Tach welded the flanges to the side pipes. Then test fit everything on the Cobra. The dirvers side fit perfect. The passenger side has the side pipe about 1-1/2" low at the mounting point in the back. It looks like the flange on the header needs to be twisted clockwise. I was concerned about getting the flanges square to the pipes. It never dawned on me that they may need twisted. If I had twisted it to where it needs to be before welding it, then there would have been issues with the flanges at the head, as two pipe are on one flange and the other two a different flange.
So, my thought is mount the header to the 351 on the stand. Bolt the side pipe up. Heat the header tubes with a torch. Then twist the plate until I get the pipe where I need it. So much for saving the Jet hot coating.
Is there a better option?
Last edited by olddog; 03-23-2009 at 05:27 PM..
|

03-23-2009, 05:26 PM
|
CC Member
|
|
|
Join Date: May 2006
Location: St. Louisville,
Oh
Cobra Make, Engine: A&C 67 427 cobra SB
Posts: 2,445
|
|
Not Ranked
I know my previous post was long, but there really is a question at the end. Is it doable to heat the header pipes and twist the flange?
|
Posting Rules
|
You may not post new threads
You may not post replies
You may not post attachments
You may not edit your posts
HTML code is On
|
|
|
All times are GMT -7. The time now is 08:11 AM.
|