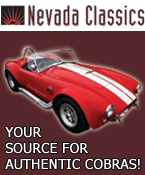 
Main Menu
|
Nevada Classics
|
Advertise at CC
|
S |
M |
T |
W |
T |
F |
S |
|
|
|
|
|
|
1 |
2 |
3 |
4 |
5 |
6 |
7 |
8 |
9 |
10 |
11 |
12 |
13 |
14 |
15 |
16 |
17 |
18 |
19 |
20 |
21 |
22 |
23 |
24 |
25 |
26 |
27 |
28 |
29 |
30 |
31 |
|
|
|
|
|
|
CC Advertisers
|
|
65Likes

11-17-2017, 04:20 PM
|
 |
CC Member
|
|
|
Join Date: Feb 2013
Location: Carlsbad,
Ca
Cobra Make, Engine: SAI FIA, 289HP (5-bolt), 48IDA Webers
Posts: 1,244
|
|
Not Ranked
Nuts & bolts 101
I was going to call this thread "Nut & Bolt Etiquette" but it is really a little more serious than that.
I recently purchased a new high end Cobra for a client that needed to have the drivetrain and a few personal touches that the client thought he would like to have added to his vehicle. I will keep all brands and businesses out of this thread as it is about the proper way to assemble components using the correct assembly procedures. Upon receiving the Cobra we started in on installing the drivetrain when we noticed a component that had an issue, no problem it is covered under warranty. What we didn't expect to find was that during the removal and replacement procedure was the nuts and bolts that were used to assemble the halfshafts to their respective components were very questionable in terms of safety and performance. As anyone building one of these vehicles knows there is an abundance of power and torque applied to the drivetrain components of these vehicles and they need to be assembled to withstand the power that is being put through them. As someone once said, " a chain is only as strong as its weakest link". This is where we get into when is a bolt not really any bolt. A short story on the chain of events that produced this particular Cobra, this Cobra is assembled to a "roller" by a company that the delivers it to a subcontractor that installs the components needed to transform the Cobra into the Cobra that that Cobra manufacturer specs their Cobra to before it ships to the buyer or drivetrain installer (me). I hope everyone was able to follow that last bit. In any event the subcontractor that installed those special components to make the Cobra something else is the reason for this technical mumbo-jumbo. I found a couple of reasons for concern this being the biggest. With all of the power and torque output created by these engines one would think that the subcontractor would have used the strongest hardware and assembly practices that you could, I know I would. Could you imagine causing the carnage that would happen when these components come unglued?! Here's what I found vs the way something this critical should be put together, the subcontractor had used to assemble the halfshaft flanges to each of the outer componts flanges, fully threaded (coarse) "grade 8" bolt, a lock washer positioned at the head of the bolt and a nylock nut at the other side of the flanges. There is no end to the many ways that this kind of assembly procedure could fail. I do give the subcontractor credit for using a "grade 8" bolt but that's it.
Here's the reason for not using fully threaded fasteners in a shear type assembly:
1) The threads are already a predetermined point of failure, the root of the thread (actually a fully threaded bolts largest outside dimension, .380") is already a built in stress fracture point. Even a fine thread bolt would have been stronger than what was used.
2) The outside thread diameter (.431") of the bolt is less than the outside diameter (.461") of the hole that it is going through in the flanges this creates a cutting motion each time that torque is applied. You can think of it like scissors cutting paper.
I would have been a little more at ease with this subcontractors assembly practices if they would have used a "grade 8" bolt that had the proper load bearing width (called the grip length) and cut down the thread legth to fit the application, fine thread as it is stronger. As for the use of a lock washer and nylock nut, neither is acceptable in this application:
1) The lock lock washer causes a stress riser as it bites into the metal surfaces, in this case in the root of the bolt head and in the flange surface.
2) With the heat generated in this area the nylock function is questionable at best, it should have had at least a flat washer to seat against instead of the flange surface.
What should have been installed in this critical area is a superior strength bolt with the proper grip length to support the width of both flanges a flat washer, either thick or thin to adjust the grip length if needed, and a fully metallic locking nut.
I use nothing but aircraft specification hardware when assembling these types of components, you can never be to careful when assembling someone else's vehicle, or your own!
As a closer to this article I'll leave you with this. The subcontractor in their infinite wisdom decided to use a nylock nuts to secure the differential hanger bolts, only problem was when he welded them to the chassis bracket! I'll let you decide what happened from there...
Last edited by CompClassics; 11-17-2017 at 04:36 PM..
|

11-17-2017, 05:00 PM
|
 |
CC Member
|
|
|
Join Date: Nov 2007
Cobra Make, Engine: Midstates/Shell Valley Street Cobra
Posts: 899
|
|
Not Ranked
The only thing that I have ever know about nuts and bolts is what my dad taught me....." eighty tidy .....lefty loosie ".......
|

11-17-2017, 05:03 PM
|
 |
CC Member
|
|
|
Join Date: Nov 2007
Cobra Make, Engine: Midstates/Shell Valley Street Cobra
Posts: 899
|
|
Not Ranked
The only thing that I have ever know about nuts and bolts is what my dad taught me....." righty tighty .....lefty loosey ".......
|

11-17-2017, 05:25 PM
|
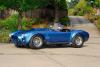 |
Senior Club Cobra Member
|
|
|
Join Date: Jan 2005
Location: saratoga,
ca
Cobra Make, Engine: Kirkham #185, Shelby Alloy 482; sold
Posts: 1,190
|
|
Neutral
I know you tighten them until the head breaks off, then back off half a turn.
__________________
Dave
|

11-17-2017, 08:31 PM
|
CC Member
|
|
|
Join Date: Dec 2015
Posts: 1,442
|
|
Not Ranked
Comp you bring up good points.
AC43-13 is "the guide" A&Ps fall back on when they can't find criteria in the manufactures manuals or get direction from engineering, or are working vintage aircraft.
Although it is used quite a bit by Mom&Pops shops and homebuilders on small propeller aircraft.
Some good information but very basic.
https://www.faa.gov/regulations_poli...cumentID/99861
Chapter 7 has the hardware.
https://www.faa.gov/documentLibrary/...Chapter_07.pdf
|

11-18-2017, 12:28 PM
|
 |
CC Member
|
|
|
Join Date: Feb 2013
Location: Carlsbad,
Ca
Cobra Make, Engine: SAI FIA, 289HP (5-bolt), 48IDA Webers
Posts: 1,244
|
|
Not Ranked
As a manufacturer of these high performance vehicles you would think that the management of the company involved or even the "DIY" guy at home in their garage should be interested in making their vehicle as safe as possible.
I know that there are other Cobras out there that had gone through this particular shop for the completion to customer delivery or completed to a turn key Cobra, these owners are completely unaware of the ticking time bomb that they are driving around. The owner of the company that uses this subcontractor has been notified of this potential issue.
Last edited by CompClassics; 11-18-2017 at 06:16 PM..
|

11-18-2017, 03:19 PM
|
 |
CC Member
|
|
|
Join Date: Apr 2005
Location: Tucson,
AZ
Cobra Make, Engine:
Posts: 5,391
|
|
Not Ranked
Proper use of fasteners and build practices is utmost! Converting my Hurricane to IRS, where the IRS unit bolted on the frame, I enlarged the holes and welded in tubes for the mounting bolts to pass through. That allowed the bolts to be tightened to torque spec w/o squeezing or dimpling the sides of the box frame. It was a lot of work but I've seen "loose" parts on cars because of "get it together" build practices and poor workmanship. Safety and quality go hand in hand.
Larry
__________________
Alba gu bràth
|

11-19-2017, 01:35 AM
|
 |
CC Member
|
|
|
Join Date: Aug 2009
Location: Adelaide,
SA
Cobra Make, Engine: AP 289FIA 'English' spec.
Posts: 13,152
|
|
Not Ranked
If the fastener is threaded up to the head, it's a screw ....and a screw should never be used it a shear load application
Cheers,
Glen
Last edited by xb-60; 11-19-2017 at 10:48 PM..
|

11-19-2017, 02:58 AM
|
CC Member
|
|
|
Join Date: Jun 2012
Location: Naracoorte,
SA
Cobra Make, Engine: CR Cobra 3169
Posts: 818
|
|
Not Ranked
Spring washers seemed like a good idea many years ago, but proofed to be so wrong. Under severe torque it can spread apart and loosen the nut. You won't see any manufacturer use them anymore. Just flat washers if any, and no lock nuts either. The best idea I've seen were 2 washers with opposite micro ramps that, if any vibration tried to undo the nut it would actually tighten itself.
I still like nyloc but never use a impact gun to tighten them.
JD
|

11-19-2017, 12:06 PM
|
 |
CC Member
|
|
|
Join Date: Feb 2013
Location: Carlsbad,
Ca
Cobra Make, Engine: SAI FIA, 289HP (5-bolt), 48IDA Webers
Posts: 1,244
|
|
Not Ranked
Taken from an old Convair employee training booklet, invaluable sources of information.
|

11-19-2017, 12:12 PM
|
 |
CC Member
|
|
|
Join Date: Feb 2013
Location: Carlsbad,
Ca
Cobra Make, Engine: SAI FIA, 289HP (5-bolt), 48IDA Webers
Posts: 1,244
|
|
Not Ranked
Here's the type of application that can be so critical in mechanical or safety related reasons.....after replacement with proper hardware.
|

11-19-2017, 12:35 PM
|
 |
CC Member
|
|
|
Join Date: Feb 2013
Location: Carlsbad,
Ca
Cobra Make, Engine: SAI FIA, 289HP (5-bolt), 48IDA Webers
Posts: 1,244
|
|
Not Ranked
Getting back to the subcontractors work, the nylock. What is the worst enemy of a nylock type locknut......
|

11-19-2017, 02:40 PM
|
 |
Senior CC Premier Member
|
|
|
Join Date: Nov 2015
Location: Bellevue,
WA
Cobra Make, Engine: Everett-Morrison 514, Toploader 4 sp, Jag IRS
Posts: 278
|
|
Not Ranked
CompClassics, thanks for this timely and useful post.
My driveshaft is removed as I replace u joints and fasteners and restore finishes.
The existing flange fasteners were fully threaded grade 8 with nylocs. I’ll be changing those out for the solution you indicate.
Will be checking my rear half shafts as well when I work on that area in the near future, nice reminder here.
Other shear bolts I replaced to date did have smooth bolt shanks for shear, as included with component packages. If I find any others on my car they will be updated!
As many fastening resources/standards as I have been researching since owning my Cobra, I’m probably barely even at 101. I tend to take fastening solutions and techniques very seriously, so this is welcomed information.
Thanks again for highlighting an important detail! Brent
|

11-19-2017, 06:01 PM
|
CC Member
|
|
|
Join Date: Jun 2012
Location: Naracoorte,
SA
Cobra Make, Engine: CR Cobra 3169
Posts: 818
|
|
Not Ranked
Is that a crack next to the weld? It doesn't look like a penetrating weld.
Heat is the enemy of a nyloc nut that's why you shouldn't impact wrench them as the heat generated as it spins also melts the nylon.
JD
|

11-19-2017, 06:41 PM
|
Senile Club Cobra Member
|
|
|
Join Date: Feb 2001
Location: Buffalo, NY USA,
NY
Cobra Make, Engine: Superformance
Posts: 4,548
|
|
Not Ranked
We use aircraft bolts and locking nuts from Aircraft Spruce (not the only source but easy for small volume orders) for halfshaft fasteners, etc.. And a fastener without a nut is a screw, so a screw can also be a bolt! Grip length is a major concern when choosing a fastener. A proper grade five fastener can out perform a grade 8 or an AN fastener when used properly.
__________________
"I'm high all right, but on the real thing....powerful gasoline and a clean windshield..."
rick@autoventureusa.net
|

11-19-2017, 07:41 PM
|
CC Member
|
|
|
Join Date: Jun 2012
Location: Naracoorte,
SA
Cobra Make, Engine: CR Cobra 3169
Posts: 818
|
|
Not Ranked
With aircraft bolts they tend to be a lower grade bolt so as not to be brittle. The aircraft bolt tends to bend before it breaks so at least it's still hanging on, but you cannot torque it as much as it will strip much easier as well.
JD
|

11-19-2017, 11:07 PM
|
 |
CC Member
|
|
|
Join Date: Aug 2009
Location: Adelaide,
SA
Cobra Make, Engine: AP 289FIA 'English' spec.
Posts: 13,152
|
|
Not Ranked
It’s worth noting that the only correct method of transmitting torque through a flange joint is via friction of the two mating surfaces.
If the friction between the two flanges is overcome (by not having the correct type and number of bolts, tightened to the correct torque), then the bolts are placed in shear….which is an unacceptable situation.
A bolt should never be in shear in a torque transmission situation.
Cheers,
Glen
|

11-19-2017, 11:30 PM
|
 |
CC Member
|
|
|
Join Date: Feb 2013
Location: Carlsbad,
Ca
Cobra Make, Engine: SAI FIA, 289HP (5-bolt), 48IDA Webers
Posts: 1,244
|
|
Not Ranked
jaydee,
No cracks were encountered at the welds. You are correct I pin your answer about heat being the enemy of a nylock. The nylock material in the bolt was melted to the point where it was mostly melted away, what was there was crystallized to the point of providing any kind of mechanical locking advantage. Hence there is no provisions for locking the bolt into a secure position.
Completely understand the advantages of the "grade 5" bolt, by allowing the bolt to have some elasticity it may prevent a catastrophic failure as compared to a "grade 8" bolt that has no elasticity and as a result will fail completely when exceeding its threshold. AN bolts tend to be strongest in a shear applications rather than tension, but the strength of an AN3 - A20 will be at least as strong as an SAE fastener under tension, per written specification.
FYI,
The aviation industry does not recognize the SAE standards of fasteners nor do they allow the use of SAE fasteners in the aviation industry.
xb-60,
I believe that you meant to say that a bolts thread should never be subjected to a shear load under torque?
Last edited by CompClassics; 11-19-2017 at 11:49 PM..
|

11-19-2017, 11:47 PM
|
 |
CC Member
|
|
|
Join Date: Oct 2016
Location: Pleasanton,
CA
Cobra Make, Engine: ERA 824 with 470 FE BBM street 427
Posts: 550
|
|
Not Ranked
Quote:
Originally Posted by Jaydee
Spring washers seemed like a good idea many years ago, but proofed to be so wrong. Under severe torque it can spread apart and loosen the nut. You won't see any manufacturer use them anymore. Just flat washers if any, and no lock nuts either. The best idea I've seen were 2 washers with opposite micro ramps that, if any vibration tried to undo the nut it would actually tighten itself.
I still like nyloc but never use a impact gun to tighten them.
JD
|
JD,
I think you’re describing Nord-Lock washers—by far the best locking mechanism for high vibration and heat. They come in a variety materials for hostile applications.
Nord-Lock Group | Secure and Innovative Bolting Solutions
|

11-19-2017, 11:57 PM
|
CC Member
|
|
|
Join Date: Jun 2012
Location: Naracoorte,
SA
Cobra Make, Engine: CR Cobra 3169
Posts: 818
|
|
Not Ranked
Years ago when I was involved in Gyro-copters. There is a Jesus bolt in the center of the rotor housing. One of the guys had a crash and the rotors struck the ground. The force was that great it stretched and bent the bolt, but never separated the rotors. I think it was a long 15 mm bolt in tension. JD
|
Posting Rules
|
You may not post new threads
You may not post replies
You may not post attachments
You may not edit your posts
HTML code is On
|
|
|
All times are GMT -7. The time now is 12:12 AM.
Links monetized by VigLink
|