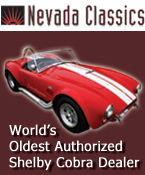 
Main Menu
|
Nevada Classics
|
Advertise at CC
|
S |
M |
T |
W |
T |
F |
S |
|
|
1 |
2 |
3 |
4 |
5 |
6 |
7 |
8 |
9 |
10 |
11 |
12 |
13 |
14 |
15 |
16 |
17 |
18 |
19 |
20 |
21 |
22 |
23 |
24 |
25 |
26 |
27 |
28 |
29 |
30 |
|
|
|
|
CC Advertisers
|
|

05-29-2020, 02:40 PM
|
CC Member
|
|
|
Join Date: Sep 2006
Location: Benbrook,
TX
Cobra Make, Engine: West Coast
Posts: 6
|
|
Not Ranked
Issue Installing Wheel Craft Wheels
I have an older set of Cobra Wheel Craft pin drive wheels with adapters that are very difficult to install the wheels on the adapters.
The first time I installed the wheels took several hours hitting the wheels and tires and then the spinner with a rubber mallet to get them on.
After that I got a lead hammer but taking the wheels off or putting them on still takes quite a while. Should I put anti seize compound, grease, oil or something on the mating surfaces.
When first putting the wheels on they will not go on far enough to get the spinner started on the threads on so I have to push and beat on the tires with a mallet for ever to get the spinner on and then use the lead hammer for another 30 - 60 minutes to get the wheel seated good.
Has anyone had this issue or have suggestions to help this situation?
Thanks,
Steve
|

05-29-2020, 03:06 PM
|
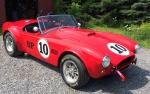 |
CC Member
|
|
|
Join Date: Aug 2013
Location: Canandaigua,
NY
Cobra Make, Engine: SPF MKII Riverside Racer FIA
Posts: 2,506
|
|
Not Ranked
You should put some anti seize on the prevent them from locking on, but you really shouldn't have to beat a tire on, and if you do that it will be really difficult to get it off. Sounds like the holes in the wheel are undersized for the pins that you have. You might want to consider getting a drill bit that is slightly larger than the holes that you have and drilling them larger. The pin do not have to be tight, the spinner is holding the wheel on, the pins are just preventing it from spinning on the hub under acceleration. Do not over drill them, just open the holes up a little, drill straight and mark the depth of the drill bit so that you do not drill too deep. You can slowly step up the size of the drill bit until the wheels go on and off easily, just do not over drill to the extent that they are wobbly on the pins.
__________________
|

05-29-2020, 03:23 PM
|
 |
CC Member
|
|
|
Join Date: Feb 2018
Location: Lodi,
CA
Cobra Make, Engine: 427 manowar forged crank roller rockers . BIG CAM.
Posts: 785
|
|
Not Ranked
Or just replace with proper size pins.
|

05-29-2020, 08:26 PM
|
CC Member
|
|
|
Join Date: May 2002
Location: SF, Bay Area,
CA
Cobra Make, Engine: SPF832, 466cid
Posts: 505
|
|
Not Ranked
If these are all the original wheels, adapter and pins that have worked together in the past, maybe the pins are out of alignment. Utilizing a template to insure all the pins are perpendicular to the adapter after torquing will help to align to the wheel holes.
|

05-30-2020, 10:06 AM
|
CC Member
|
|
|
Join Date: Sep 2006
Location: Benbrook,
TX
Cobra Make, Engine: West Coast
Posts: 6
|
|
Not Ranked
Thanks for the suggestions and information guys.
I assume these are the original wheels, pins and adapters but I bought them second hand about ten years ago. Measuring with a caliber the pins are .77" and the holes in the wheel are also .77" and the spindle is 3.27", hole in wheel is 3.28".
I'm not sure I can take a hole that is .77" and enlarge it to around .8" with good enough precision that I feel comfortable with it.
Can the pins be ordered in all kind of sizes?
Thanks!
|

05-30-2020, 05:50 PM
|
 |
CC Member
|
|
|
Join Date: Jun 2007
Location: Caldwell,
NJ
Cobra Make, Engine: ERA 427, 482ci sideoiler
Posts: 144
|
|
Not Ranked
My take after a couple of glasses of wine, buyer beware! The spindle 3.27" locator and wheel 3.28" locator are an extreamly tight fit, with that said, I would not alter those dimensions, at this time. The locator pin 0.77" and wheel pin hole 0.77 dimensions are an iterference fit, although a very loose interference fit. What I would do is take the 0.77" pins thread them on to a threaded rod that can be placed in a drill chuck. Once threaded into the chuck, spin the pin and use sand paper or a fine file to take down the diameter of the pin a few thousandths, more so at the end of the pin and less at the spindle end, which should ease your fitting issues and not cause the fit to get to loose. Take it slow and do frequent trial fitting. Hope this helps.
|

05-30-2020, 08:56 PM
|
CC Member
|
|
|
Join Date: May 2002
Location: SF, Bay Area,
CA
Cobra Make, Engine: SPF832, 466cid
Posts: 505
|
|
Not Ranked
|

05-30-2020, 09:55 PM
|
 |
CC Member
|
|
|
Join Date: Jun 2001
Location: Mesa,
AZ
Cobra Make, Engine: ERA #2119 289FIA
Posts: 5,380
|
|
Not Ranked
If you go with new pins, be sure that the new pins don't bottom out in the holes in the wheel. Another tip is to NOT install the pins with an impact wrench. They may split or hog out the drive hole. Ask me how I know. 
__________________
Karlos
"In the Land of the Pigs, The Butcher is King"
|

05-31-2020, 08:18 AM
|
CC Member
|
|
|
Join Date: Sep 2006
Location: Benbrook,
TX
Cobra Make, Engine: West Coast
Posts: 6
|
|
Not Ranked
Thanks again for the information, suggestions and tips. I think I will start out with sanding or filing with the pin lug in a drill on the wheel that is currently off but will probably end up ordering a new forged set.
Maybe torquing these down has caused them to expand a little?
Although I have not torqued them to the 85 ft/lb I have seen lately on here.
|
Posting Rules
|
You may not post new threads
You may not post replies
You may not post attachments
You may not edit your posts
HTML code is Off
|
|
|
All times are GMT -7. The time now is 05:06 PM.
Links monetized by VigLink
|