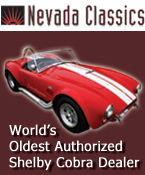 
Main Menu
|
Nevada Classics
|
Advertise at CC
|
February 2025
|
S |
M |
T |
W |
T |
F |
S |
|
|
|
|
|
|
1 |
2 |
3 |
4 |
5 |
6 |
7 |
8 |
9 |
10 |
11 |
12 |
13 |
14 |
15 |
16 |
17 |
18 |
19 |
20 |
21 |
22 |
23 |
24 |
25 |
26 |
27 |
28 |
|
|
CC Advertisers
|
|

03-10-2008, 09:54 PM
|
CC Member
|
|
|
Join Date: Nov 2004
Location: Hillsboro,
OR
Cobra Make, Engine: ERA 541, Shelby 427, TKO600
Posts: 59
|
|
Not Ranked
F$!%ng Dowel Pins
Hey guys, need some help. I need to remove the dowel pins in the block that locates the bell housing. I have a scatter shield and I dialed it in but I need to replace the pins with longer ones so I can weld on locating washers to the bell housing. The pins in the block seem like they are welded in  I wonder if it is worse because I have a aluminum block with steel pins...
Anyone have an idea on how I might get them out? I tried heating them, grabing them with vice grips but nothing works. Can't even get them to rotate. I have a big slide hammer but I need to attach it to something. I thought about welding a bolt to the pin but that seems sort of drastic. Also thought about drilling a hole in them and then seeing if I can tap threads so I can put a bolt to pull on with the slide hammer, but again pretty drastic and the pins are REAL hard.
I am out of ideas. If anyone has any ideas let me know... help!
Thanks,
Russ
|
-
Advertising

03-10-2008, 10:28 PM
|
 |
CC Member
|
|
|
Join Date: Feb 2006
Location: Gilroy,
CA
Cobra Make, Engine: SPF 2291, Whipple Blown & Injected 4V ModMotor
Posts: 2,738
|
|
Not Ranked
Dowel Pin Removal
This is the tool you need to get them out.
Click here => http://stefs.com/bandb/products/prod...npullerset.htm
If they are frozen in or if the ends are mutilated from the vise grips then you have two other alternatives if the block casting can be drilled from behind the dowel pin then you can drive it out with a hammer and a drift. If not then you need to EDM it out.
Hope this helps and hope you don't need EDM.
Ed
__________________
Help them do what they would have done if they had known what they could do.
|

03-11-2008, 05:51 AM
|
CC Member
|
|
|
Join Date: Mar 2001
Location: E BRUNSWICK N.J. USA,
Posts: 3,841
|
|
Not Ranked
Playing with fire?
1Trkpony Russ Drill two small holes through the bell housing and into the block. Use these as your alignment dowels. Heating, drilling, tapping, hammering, and drilling out the back side can all break that Aluminium block. Get 2 long 1/4 roll pins, drill 2 1/4 hole about 1/2 deep through bell housing and block, Tap the pins in and everything will be centered. Messing with thoses dowels is a pain in the A$$. I ground out all my mount holes to get mine centered ( bellhousing) 3 hours later from .038" to .002" in the car. Welded nuts to the bell housing to keep centered. I just did a stroker kit and rechecked the bell housing again. It was .012" off. I recenter the housing( out of the car) and added the 2 pins at 10 o clock and 2 oclock. Removed the housing and rechecked center after pins reinstalled, bell right on the number. This is alot easier if you have the room in the holes to move the bell housing around. I have each bell housing for each motor, I don't switch them. Mated for life, or explosion, which every cames last. Rick L Ps 90 degree drill make this alot easier in the car.
|

03-11-2008, 05:55 AM
|
CC Member
|
|
|
Join Date: Dec 2001
Location: Louisville,
KY
Cobra Make, Engine: I'm Cobra-less!
Posts: 9,417
|
|
Not Ranked
The way I do it is to take a slide hammer, find a nut that will thread on the end of it, then tack the nut to the dowel. Thread the slide hammer into the nut, jack it a couple times, and you're done.
|

03-11-2008, 08:56 AM
|
 |
Senior Club Cobra Member
|
|
|
Join Date: Jul 2006
Location: McKinney,
TX
Cobra Make, Engine: ERA GT #2077, 331 SBF, Webers, Gurney Eagle heads
Posts: 1,275
|
|
Not Ranked
Grind a flat on one side of the dowel, squirt it with WD40 and try your vise grips again .. worked for me
Sam
|

03-11-2008, 10:19 AM
|
CC Member
|
|
|
Join Date: Nov 2004
Location: Hillsboro,
OR
Cobra Make, Engine: ERA 541, Shelby 427, TKO600
Posts: 59
|
|
Not Ranked
Hey guys great ideas. The more I think about it the more paranoid I am about using a slide hammer with the aluminum block. I like Rick's idea above as I have already dialed in the bell housing (~0.003") by carefully opening the holes in the housing in the direction needed.
I will heating it again tonight (after letting the penetrant sit too), but I think it is time for plan B. Grinding a flat spot on one side also might work as the vice grips can't grip the hard pins (don't even mark them up).
Keep up the good ideas, I will let you know how it works out.
|

03-11-2008, 02:16 PM
|
Senior Club Cobra Member
|
|
|
Join Date: Feb 2008
Location: Jacksonville,
FL
Cobra Make, Engine: VSE alum. frame, FFR carbonfiber body (under construction)
Posts: 293
|
|
Not Ranked
You are heating the block and not the dowels, correct?
Just my .02 euros.
|

03-11-2008, 03:47 PM
|
 |
CC Member
|
|
|
Join Date: Dec 2006
Location: Millbrook,
NY
Cobra Make, Engine: ERA 758 KC Pond 482
Posts: 391
|
|
Not Ranked
I just went through this. You are correct the dowel pins are REALLY hard and even with a carbide tipped drill bit it is very difficult to drill. I did the heat deal and managed to get one out. The other-no way. I finally ground 2 flats on it and once I turned it with a wrench, I could work it out.
For the best solution for longer dowel pins check these:
http://www.robbmcperformance.com/products/dowels.html
|

03-11-2008, 04:03 PM
|
Senior Club Cobra Member
|
|
|
Join Date: Jul 2000
Location: Las Vegas,
NV
Cobra Make, Engine: ERA 427 SO
Posts: 1,126
|
|
Not Ranked
Pony, one thing I did, not yet mentioned here: weld some 3/8" all-thread onto the end of the dowel, get a piece of pipe (I used 1/2")that will slip over the end of the all-thread and dowel, leaving about 1" of threads exposed. Put thick washer(s) on, put on a 3/8" nut to fit the all-thread and start tightening. It pushes the pipe against the block and pulls on the dowel, a nice gentle tug that will pull the dowel out of the block. Just do a good welding job on the all-thread to the dowel.
Let us know what works.
__________________
Ken
|

03-11-2008, 04:19 PM
|
CC Member
|
|
|
Join Date: Nov 2004
Location: Hillsboro,
OR
Cobra Make, Engine: ERA 541, Shelby 427, TKO600
Posts: 59
|
|
Not Ranked
Thanks everyone, I really appreciate all the ideas. Ken I like your idea as it does not put stress on the block that a slide hammer would. Tonight I am going to try :
More heat (I think I will use a propane torch vs my oxy torch as I don't have a rosebud just a very small welding tip) to block only - damm aluminum soaks the heat up too well then use a ice cube to cool the pin and see if I can loosen it up.
I think the lower pin is accessable from the backsize if I remove my clutch slave cylinder bracket and if so I can drive it out from the front but maybe it is not drilled all the way thru...
If that does not work I need to decide to either do the weld thing or grind some flats on it...
Thanks!!
Russ
|

03-11-2008, 10:48 PM
|
CC Member
|
|
|
Join Date: Nov 2004
Location: Hillsboro,
OR
Cobra Make, Engine: ERA 541, Shelby 427, TKO600
Posts: 59
|
|
Not Ranked
Well I have been at it for about 3 hours... and NO DICE
I tried heating until I was blue in the face and nothing. I used ice to cool the pin with no results. I needed to go more drastic. I decided to weld all tread on the end of the pin and then use Ken's idea above. It was tough welding (took a lot more heat then I first guessed) and the second time I got a good weld/penetration. I used a socket and washers and tightened the nut and it just broke the all thread... I then welded a nut on the stub of the all thread to see if I could get it to turn, nope just broke the all thread again. I was careful not to damage the pin because I thought I might not succeed so it is still in good shape where the bell housing sits on it.
I think the pins are fused in the aluminum... I guess I can try welding a grade 8 bolt the with the head cut off but I am not sure it will work. Also was hoping the bottom pin had a hole in the front where I could drive it out, but nope a blind hole. I could drill into the block and then drive it out but I am not sure about that.
I am leaning towards Rick Lakes idea above about drilling 2 new 1/4" locating pins right now as that seems to be the only solution and the pins are still pretty well unmolested. I have been scooping out a good place to drill and it looks like the top of the BH seems to be the best place but I need to spend some more time on it to make sure.
If anyone has any more ideas or suggestions keep them coming...
Russ
|

03-12-2008, 04:57 AM
|
CC Member
|
|
|
Join Date: Mar 2001
Location: E BRUNSWICK N.J. USA,
Posts: 3,841
|
|
Not Ranked
Russ quit while your ahead
1Trkpony Russ I don't know how make heat cycles you have done with the torch, but stop before you breakoff that corner of the block or get the area out of center or weaken it. I have had this problem before with my Shelby and other Aluminium motors. Some come out and others stay in for life. I have cracked the ears off an LS1 motor trying to install off set dowel pins for a Lakewood bell housing for racing. 1/2" hole(2) deep and the pins was the easiest way to go. Put tape on the drill bit so you know where the 1/2" depth is. Good Drill bit and go slow, this is no race. Try and drill straight. IMO, the pins are more for centering the bell that stopping it from twisting. As long as you use all the bolts and a little loc-tite,(blue) there shouldn't be any problems. Don't over torque the bolts. Rick L. Ps Russ try and keep the pins as far away from each other as possible. If you are looking at a clock. mine are 10 and 2 positions. Don't put them within 2-4" of each other, there could be too much wiggle. Been there tryed that.
Last edited by RICK LAKE; 03-12-2008 at 05:06 AM..
Reason: Brain not working this early in the morning
|

03-12-2008, 04:59 AM
|
CC Member
|
|
|
Join Date: Dec 2001
Location: Louisville,
KY
Cobra Make, Engine: I'm Cobra-less!
Posts: 9,417
|
|
Not Ranked
Honestly, weld a nut to the dowel and use the slide hammer on it.....it will take you 5 minutes, I promise.
Most slide hammers have a threaded end so that you can screw on various attachments. Find a nut to match, tack it in about 2-3 spots, then screw the slide hammer in and work it.
|

03-12-2008, 11:53 AM
|
CC Member
|
|
|
Join Date: Nov 2004
Location: Hillsboro,
OR
Cobra Make, Engine: ERA 541, Shelby 427, TKO600
Posts: 59
|
|
Not Ranked
Hey Rick,
I did not over heat it, as I was afraid of doing that so no issue there. In fact I could not get it all that hot with my torch so I moved on to plan b with the all thread.
On the pins the way I opened the holes in the bell was with a file in one direction only so the original pins still do a good job of holding the twisting motion if needed.
On drilling for the pins, I am going to drill the bell housing and backing plate off the car (on a drill press) then install, re-center with dial indicator and drill just the block for the pins. I agree you want them ideally 180 out from each so I will try and find good spots. Right now 1-2 o'clock is easy and trying to get something around 7 o'clock if possible.
Brent, I think I am done welding on the pins and pulling them with my slide hammer makes me nervous that I will break ear off the aluminium block on the lower one. That would suck.
Russ
|

03-12-2008, 12:35 PM
|
CC Member
|
|
|
Join Date: Jan 2005
Location: Hillsboro,
OR
Cobra Make, Engine: Scratch built CSX style frame, Carbon fiber body, 393 Stroker, T-bird IRS, T5
Posts: 1,623
|
|
Not Ranked
Russ,
If you need a hand let me know. I'm just a short drive from your place.
Bob S.
|

03-18-2008, 06:31 PM
|
CC Member
|
|
|
Join Date: Nov 2003
Location: Carpentersville,
Il
Cobra Make, Engine: shell valley cobra-350 chevy
Posts: 62
|
|
Not Ranked
Did you ever get them out? What got the job done?
|

03-19-2008, 11:29 AM
|
CC Member
|
|
|
Join Date: Nov 2004
Location: Hillsboro,
OR
Cobra Make, Engine: ERA 541, Shelby 427, TKO600
Posts: 59
|
|
Not Ranked
Nope did not get them out, stopped trying before I damaged anything. I got the BH centered and welded on the "washers" without the block plate to make sure they fit nice. They are actually very close to working (centering the BH) with the block plate on but to be sure I then drilled 2 holes for new locating pins at 7 o'clock and 2 o'clock and used drill rod for a very tight fit. Now it is dialed in and will not move. If I every remove my engine I can have a machine shop remove the pins and put in the longer ones and all will still line up since the washers are already welded on.
|

03-19-2008, 02:08 PM
|
 |
Senior Club Cobra Member
|
|
|
Join Date: Dec 2001
Location: Glendale,
AZ.
Cobra Make, Engine: Cobray-C3, The 60's body lines on todays chassis technology
Posts: 2,302
|
|
Not Ranked
The pins can be a pain. An attachment screws to the end of a slide hammer and works great if you have room. If space will not allow then I weld a nut to the pin with an arc welder. Get big enough nut so it allows a good spot weld between inside of nut and the pin. The localized heat from the weld shocks pin and block to loosen it up many times. I use an air impact to rattle the nut while a screwdriver prys out from the block.
You got her handled but thought a mention of the welded nut may help someone in the future. Enjoy your Toy!!! Jeff C
|

03-19-2008, 02:38 PM
|
CC Member
|
|
|
Join Date: Mar 2006
Cobra Make, Engine:
Posts: 277
|
|
Not Ranked
Have you tried shrinking the aluminum and the pin away from each other with a CO2 extinguisher. Drill a hole in 1/2" plywood just large enough to not show daylight at the bell housing edges when dropped over the pin. Put the horn of the extinguisher down on the plywood and carefully discharge the CO2 to the metal parts. The pin should shrink away from the aluminum, and vice versa. Have used this method to shrink out crank bearings on motor cycles, and alternator housing front bearings for many years. Be careful, CO2 will freeze your skin instantly, and cause worst than frostbite.
|

03-12-2009, 08:35 PM
|
CC Member
|
|
|
Join Date: Jul 2008
Location: Driftwood,
TX
Cobra Make, Engine: Contemporary Cobra, 427 side oiler
Posts: 1,850
|
|
Not Ranked
Quote:
Originally Posted by vettestr
...eld a nut to the pin with an arc welder. Get big enough nut so it allows a good spot weld between inside of nut and the pin. The localized heat from the weld shocks pin and block to loosen it up many times. I use an air impact to rattle the nut while a screwdriver prys out from the block. You got her handled but thought a mention of the welded nut may help someone in the future. Enjoy your Toy!!! Jeff C
|
Your advice above helped me about two hours ago. I wound up MIG welding two 5/8" nuts onto the dowels and cranking on them just as you described. The dowels are super hard steel so you gotta really put the arc heat on them to get a bond with the nut. I twisted 4 nuts off on one dowel before I finally got the weld to stick. There is no way vice grips or any type of pulling with a slide hammer could have broken mine loose. This was by far the biggest pain in the a$$ I have had on the build project.
|
Posting Rules
|
You may not post new threads
You may not post replies
You may not post attachments
You may not edit your posts
HTML code is Off
|
|
|
All times are GMT -7. The time now is 01:27 AM.
|