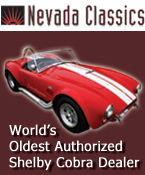 
Main Menu
|
Nevada Classics
|
Advertise at CC
|
S |
M |
T |
W |
T |
F |
S |
|
|
|
1 |
2 |
3 |
4 |
5 |
6 |
7 |
8 |
9 |
10 |
11 |
12 |
13 |
14 |
15 |
16 |
17 |
18 |
19 |
20 |
21 |
22 |
23 |
24 |
25 |
26 |
27 |
28 |
29 |
30 |
31 |
|
|
CC Advertisers
|
|
2Likes
-
1
Post By eschaider
-
1
Post By patrickt

01-01-2020, 09:29 AM
|
CC Member
|
|
|
Join Date: May 2015
Posts: 626
|
|
Not Ranked
Engine expansion when hot?
I wonder if anyone knows the answer? Scenario; Windsor iron block aluminum heads, as the motor goes form ambient to what 180+ degrees F, I would submit that the heads would get taller and wider (a minuscule amount)?
Resulting in the intake (which also gets wider) being “pinched” in the valley tighter?
__________________
Superformance 1764
Ford Racing 427 SB
|

01-01-2020, 10:01 AM
|
 |
CC Member
|
|
|
Join Date: Feb 2006
Location: Gilroy,
CA
Cobra Make, Engine: SPF 2291, Whipple Blown & Injected 4V ModMotor
Posts: 2,731
|
|
Not Ranked
Here is a posting I did about the effect on an engine block and heads as the engine comes up to operating temperature. The focus is on head gaskets and why the recommendation to retorque after an initial heat cycle.
The math and the thermal expansion phenomena occur in all directions not just one so the model can help you to actually measure what you are interested in. Because everything is bolted together when cold the similar metals will exhibit similar geometry after warm up. The disimilar metals will not. Here is the link => Effect of Engine Warm Up on Engine Dimensions
Ed
__________________
Help them do what they would have done if they had known what they could do.
|

01-01-2020, 01:30 PM
|
 |
Half-Ass Member
|
|
|
Join Date: Jun 2005
Cobra Make, Engine: ERA #732, 428FE (447 CID), TKO600, Solid Flat Tappet Cam, Tons of Aluminum
Posts: 22,011
|
|
Not Ranked
Iron Block and Aluminum Head Expansion Rates
Quote:
Originally Posted by tortuga
I wonder if anyone knows the answer? Scenario; Windsor iron block aluminum heads, as the motor goes form ambient to what 180+ degrees F, I would submit that the heads would get taller and wider (a minuscule amount)?
Resulting in the intake (which also gets wider) being “pinched” in the valley tighter?
|
I don't know the answer regarding intakes, but I have listened to and studied my iron block/aluminum headed mill for almost 15 years and the fact that it has a solid, flat tappet cam and the clatter that it makes, or doesn't make, depending on the time and temperature after start up. I gap my valves at .018" COLD and I have aluminum roller rockers. The cam maker calls for a lash of .025" HOT. The classic answer to the difference between cold and hot lash on an iron block/aluminum headed engine is .007", give or take. When I first start my engine up COLD, there is virtually no valve clatter at all. When I then take her out and she begins to warm up, as measured by the coolant temperature, the valve clatter will be at its loudest and sharpest when the coolant becomes hot but the oil is not. I presume that the aluminum heads and rockers have now had a chance to heat up, and expand, but the iron block has not. As the oil temperature reaches the same temperature as the coolant, the valve clatter reduces down to a "normal" level of clatter. I presume this is because the temperature of the iron, and the expansion of the block, has now had a chance to catch up with the temperature, and the expansion, of the heads. A few years ago we had a thread over on the FE forum about the difference between cold and hot lash on iron block/aluminum headed FEs with SFT cams. A couple of guys took it on themselves to go out to the garage, check their lash while cold, then they drove the car until the coolant showed it had warmed up, pulled back in the garage, checked their lash again, and proclaimed the difference to be .011" to .013" difference! That was quite a change from the standard answer. Of course they did not run their engines until the block was at the same temperature as the heads, just until the coolant got hot. When I run my engine, the lash starts out as .018" and the valve train is quiet as a mouse, the lash then grows to .030" or more for a short while (when the heads have expanded but the block has not), and the valve train has a really nice, pronounced clatter to it. Then the lash shrinks down to .024" or so and has a "normal" clatter to it. It actually took me years to figure this out.  Hope this helps.
|

01-01-2020, 05:23 PM
|
 |
CC Member
|
|
|
Join Date: Feb 2006
Location: Gilroy,
CA
Cobra Make, Engine: SPF 2291, Whipple Blown & Injected 4V ModMotor
Posts: 2,731
|
|
Not Ranked
The experience Patrickt is sharing with you is directly related to the differences in the coefficient of thermal expansion for the two metals. The coefficient of thermal expansion simply gives the amount of growth per degree of temperature increase that a particular metal will exhibit.
The increase and then subsequent decrease in valve lash is attributable to the differences in the thermal conductivity of the two metals. Aluminum has a higher thermal conductivity than cast iron which means it will expand more and initially faster than cast iron. The lower thermal conductivity and lower coefficient of thermal expansion for the cast iron means the cast iron will expand less (but it will still expand) and it will take longer to see this expansion because it's thermal conductivity is less than that of aluminum.
Eventually when both metals have had sufficient soak time to normalize their temperatures and realize their maximum expansion for the heat energy absorbed, the cam and valvetrain will have quieted down again. The reduced lash that has quieted the valve train is directly attributable to the cast iron block's expansion after it's operating temperature has normalized with that of the cylinder head.
Ed
__________________
Help them do what they would have done if they had known what they could do.
|

01-02-2020, 07:18 AM
|
CC Member
|
|
|
Join Date: May 2006
Location: St. Louisville,
Oh
Cobra Make, Engine: A&C 67 427 cobra SB
Posts: 2,445
|
|
Not Ranked
https://www.engineeringtoolbox.com/l...ents-d_95.html
aluminum is about 22 and cast iron is about 11 or aluminum grows twice that of cast iron.
As for your intake, that is the beauty of a 90 deg V block. As things grow longer it is growing half the distance vertically and half the distance horizontally, per head.
I think you are trying to understand your problem, but remember there are thousands of engines like yours. The aluminum/cast iron does make sealing harder, but the gaskets take the slight changes. If this were your only problem then all of these engines would have the same problem.
I mentioned measuring gaps while you had the engine apart in another thread. I think you mentioned doing some checking. Each little thing adds to what the gaskets have to make up for.
You have talked like the ports have been opened up to where there is very little seal surface left. Blown engines they often mil a tiny grove around the cylinder and put a wire in the grove. This bites into the gasket and can hold more pressure. Intakes I have seen rubber O-rings installed. I'm not suggesting this is "thee" solution, but it may be worth considering with some experts.
Oops: I may have original poster confused with someone else. Apologies if so.
Last edited by olddog; 01-02-2020 at 07:21 AM..
Reason: Oops
|

01-02-2020, 09:18 AM
|
CC Member
|
|
|
Join Date: May 2015
Posts: 626
|
|
Not Ranked
Thanks for the very informative responses
My concern (and my conclusion) is that the intake is actually bit harder by the heads as the motor heats up. I did measure the gaps as kindly described to me on this and other forums with square results.
I’ve reassembled using liberal application of permatex aviation gasket maker. So good so far, oil level seems to be holding and she seems to be running crisper (no more two stroke fuel?)...
Thanks again gentlemen for your help!
Steve H
1764
__________________
Superformance 1764
Ford Racing 427 SB
|

01-02-2020, 09:34 AM
|
 |
CC Member
|
|
|
Join Date: Feb 2006
Location: Gilroy,
CA
Cobra Make, Engine: SPF 2291, Whipple Blown & Injected 4V ModMotor
Posts: 2,731
|
|
Not Ranked
Glad you've found a working solution, Steve. Even with the dissimilar growth rates of the different materials, if the gasket air gap that Tottuga was encouraging you to measure was square top to bottom the differences in growth would not be enough to expose an intake port.
That said, repeated heating and cooling cycles could possibly deteriorate the quality of the seal the gasket had with either or both the head and manifold. On heads and manifolds that have been port matched you will have reduced margin around each port for sealing which will provide increased opportunity for a gasket sealing failure. The easiest fix for this problem is to glue the gasket to both surfaces at assembly. I believe Brent Lykins suggested this in another thread. It does make disassembly a messier event but it also makes for a reliable gasket seal.
Ed
__________________
Help them do what they would have done if they had known what they could do.
|
Posting Rules
|
You may not post new threads
You may not post replies
You may not post attachments
You may not edit your posts
HTML code is Off
|
|
|
All times are GMT -7. The time now is 09:27 AM.
Links monetized by VigLink
|