Welcome to Club Cobra! The World's largest
non biased Shelby Cobra related site!
- » Representation from nearly all
Cobra/Daytona/GT40 manufacturers
- » Help from all over the world for your
questions
- » Build logs for you and all members
- » Blogs
- » Image Gallery
- » Many thousands of members and nearly 1
million posts!
YES! I want to register an account for free right now!
p.s.: For registered members this ad will NOT show
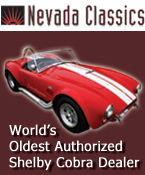 
Main Menu
|
Nevada Classics
|
Advertise at CC
|
January 2025
|
S |
M |
T |
W |
T |
F |
S |
|
|
|
1 |
2 |
3 |
4 |
5 |
6 |
7 |
8 |
9 |
10 |
11 |
12 |
13 |
14 |
15 |
16 |
17 |
18 |
19 |
20 |
21 |
22 |
23 |
24 |
25 |
26 |
27 |
28 |
29 |
30 |
31 |
|
|
CC Advertisers
|
|
1Likes
-
1
Post By 750hp

07-10-2013, 02:28 AM
|
 |
CC Member
|
|
|
Join Date: Jun 2009
Location: Sydney,
NSW
Cobra Make, Engine: RCM, Jag front and rear, LS3
Posts: 1,640
|
|
Not Ranked
AL tig welding setup q's
A question for the ac tig welders.
I'm finally getting an acdc tig!
What tungsten do you use for aluminium with AC tig? I have read articles that all contradict each other. Some say straight tungsten (apparently not good with inverter), some say ceriated, some say thoriated, some say lantharated and also zirconiated (so pretty much all). Whilst saying that they say not to use the others.
I will be mostly welding sheet and flat bar. 1.5mm to 6mm.
I have thoriated so would like to use those, but some articles say they crack.
Looking for real world advise!
|
-
Advertising

07-10-2013, 04:40 AM
|
 |
CC Member
|
|
|
Join Date: Jun 2009
Location: Sydney,
NSW
Cobra Make, Engine: RCM, Jag front and rear, LS3
Posts: 1,640
|
|
Not Ranked
Yes, i have read that. But like i said, it says one thing and other sites say another. Lincoln says Zirconiated or pure tungsten.
Aluminum Welding FAQs
This recommends Thoriated.
TIG welding Aluminum
When i read forum posts it is the same. Old school welders say pure tungsten others say different.
Interested to know what people on here use.
|

07-10-2013, 05:25 AM
|
 |
Senior Club Cobra Member
|
|
|
Join Date: Sep 2000
Location: Holderness, NH, US of A,
NH
Cobra Make, Engine: CSX 4772 old iron FE
Posts: 5,499
|
|
Not Ranked
I use pure but I have an old machine.
|

07-10-2013, 05:33 AM
|
 |
CC Member
|
|
|
Join Date: Jun 2009
Location: Sydney,
NSW
Cobra Make, Engine: RCM, Jag front and rear, LS3
Posts: 1,640
|
|
Not Ranked
Quote:
Originally Posted by mickmate
I use pure but I have an old machine.
|
Thanks, any thoughts on what works with inverter?
I am thinking i will try the thoriated first since i already have them, and then go from there. My only concern is that i have never used AC tig before (only DC) and i want to know the set up works so i can focus on technique.
|

07-10-2013, 05:38 AM
|
 |
CC Member
|
|
|
Join Date: Jan 2001
Location: Sunbury,
VIC
Cobra Make, Engine: Rat Rod Racer, LS1 & T56
Posts: 5,391
|
|
Not Ranked
Bear in mind I'm no expert here, this is just what I've found.
I used 2% Thoriated (Red) for steel and stainless and sharpen them to a needle point. They seem to give good results.
On Aluminium I used to use Zirconated (White). You use the plain electrode on a bit of scrap before you start and it will form a ball on the end. They worked OK.
More recently I've switched to Ceriated (Grey) for Aluminium. I sharpen them to a pencil point, a bit flattened on the end. I find they give a more concentrated arc that is easier to control.
Cheers
__________________
Mike Murphy
Melbourne Australia
|

07-10-2013, 06:13 AM
|
 |
CC Member
|
|
|
Join Date: Jun 2009
Location: Sydney,
NSW
Cobra Make, Engine: RCM, Jag front and rear, LS3
Posts: 1,640
|
|
Not Ranked
Thanks mike exactly the info I wanted.
Out of interest have you tried thoriated on aluminium?
|

07-10-2013, 06:19 AM
|
 |
CC Member
|
|
|
Join Date: Jan 2001
Location: Sunbury,
VIC
Cobra Make, Engine: Rat Rod Racer, LS1 & T56
Posts: 5,391
|
|
Not Ranked
Quote:
Originally Posted by Zedn
Thanks mike exactly the info I wanted.
Out of interest have you tried thoriated on aluminium?
|
I think I did ages back when I was still trying to learn how to weld aluminium. So that'll be no gauge as to how well they perform
Cheers
__________________
Mike Murphy
Melbourne Australia
|

07-10-2013, 06:32 AM
|
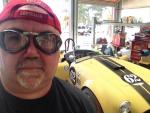 |
CC Member
|
|
|
Join Date: Feb 2002
Location: Alice Springs, central Australia,
NT
Cobra Make, Engine: Classic revival kit (CR3181), gen III engine, T56 6 speed box, AU XR8 lsd diff
Posts: 5,699
|
|
Not Ranked
Mike beat me.
I was going to say pointy red tip on steel, rounded white tip on ally
__________________
Cruising in 5th

---------------------------------------------
Never be afraid to do something new, Remember, Amateurs built the Ark: Professionals built the Titanic.
|

07-10-2013, 06:40 AM
|
 |
CC Member
|
|
|
Join Date: Nov 1999
Location: Brisbane, Australia,
Q
Cobra Make, Engine: Contemporary CCX3117 427FE
Posts: 4,381
|
|
Not Ranked
The two best welders I've seen for automotive art were sharing and comparing their styles a couple of years back on this thread http://www.yellowbullet.com/forum/sh...ad.php?t=97936 I've copied and pasted bits from their posts.
Aaron from 6061 6061.com Intake elbows (site currently down): I usually use 5052 sheet because it is strong and it can be bent/formed without it wanting to crack like 6061. 3003 sheet is soft and easier to form into shapes, but not as rigid.
I use 5356 filler rod despite what some articles say. Most say the 4043 gives a better weld appearance. For me, 5356 seems to shine better. 4043 seems to work better (for me) when welding on cast intakes. I also noticed that hammer-forming a part after welding with 4043, it seemed to want to crack easier.
On my welder, I keep the balance in the 65-68% area, and adjust the positive amperage about 25% lower than the negative. On most welders, adjusting the positive and negative amperage independently isn't an option.
There are also waveform adjustments on the dynasty 350... I leave mine on soft squarewave.
Hertz anywhere above 300. When welding most of my parts, I can get the tip to stay sharp and not ball up with the ceriated tungsten. The high hertz adjustment and adjusting the positive/negative amperage values independently keeps the heat off the tungsten.
Here's an example of his work
John Marcella Marcella Manifolds Home Page : The newer style machines w/ an inverter have a hertz adjustment and with running more hertz it has a tendency to narrow the arc. If all your doing is looking to minimize the white fuzz on the side of the weld you can achieve it by running more negative balance and a higher hertz adjustment. However this is not of any importance when dialing in the correct settings. As far as machine settings it is very difficult to give advise because even though material thickness may be the same the size of the panel and even the thickness of the medal on the table you are welding on all greatly effect how fast the heat is dissipated. I almost never use the pulser, but lately I have been playing around with it and have had pretty good results. (the pulser does not change the look of the weld it just limits the amount of heat that gets put into the part). I personally rarely use 5052, I usually use 4043.
I prefer a different tungsten on different machines because the machine basically preferred different tungsten. On the sincrowaves the green was ok, but if I could get away with it I would use the red. I tried the ceriated that Aaron says he uses but I didn't like it, I ground the rest of the box and used them as scribs. On the aerowave it really likes the lanthenaited, however my dynasty hates it. What I use on my dynasty is the 2% thoraited (red). All the different types of machines will react differently. I use ceriated (orange or grey band) or thoriated (red). I don't really prefer one over the other. I never use green anymore... it seems to get contaminated too easy and the tip doesn't stay as sharp.
John's LS manifold
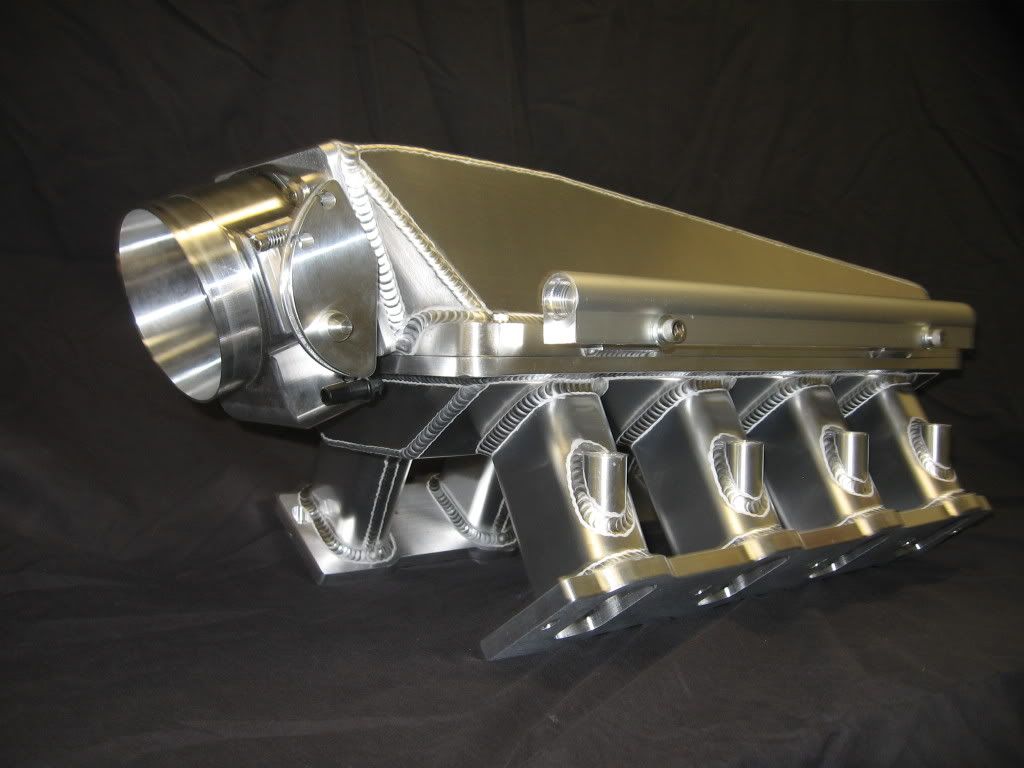
__________________
Craig
|

07-10-2013, 02:10 PM
|
 |
CC Member
|
|
|
Join Date: Jun 2009
Location: Sydney,
NSW
Cobra Make, Engine: RCM, Jag front and rear, LS3
Posts: 1,640
|
|
Not Ranked
Wow. That is some nice fabrication! Thanks for posting that.
Those posts sum it up completely. Everyone likes something different.
Looks to be all about trial and error to come up with what works best for the user and machine.
|

07-10-2013, 02:45 PM
|
 |
Senior Club Cobra Member
|
|
|
Join Date: Sep 2000
Location: Holderness, NH, US of A,
NH
Cobra Make, Engine: CSX 4772 old iron FE
Posts: 5,499
|
|
Not Ranked
I can't weld like that but have worked with a couple of guys that can. They told me not to hold the filler rod right in the joint but to feed it in in a regular rhythm as needed and use it to control the temperature of the weld pool. That would be as well as the pedal of course. It's a trick to get going as there's a lot of noise, magnesium alloys burning etc all going on. The trick I found is to use the amp per thou rule and get right into it with full heat to start the melt of both parts to be welded and then use the filler wire to help control the puddle heat. Also play on some scrap to get your AC balance so it's getting penetration without getting sooty or peppery.
|

07-10-2013, 04:39 PM
|
 |
CC Member
|
|
|
Join Date: Apr 2010
Location: Hobart,
TAS
Cobra Make, Engine: ?????
Posts: 494
|
|
Not Ranked
My TIG notes from night school...
Edit: PM sent, will email better
Last edited by Tonus72; 07-10-2013 at 04:40 PM..
Reason: File too small
|

07-10-2013, 07:47 PM
|
 |
CC Member
|
|
|
Join Date: Jan 2001
Location: Sunbury,
VIC
Cobra Make, Engine: Rat Rod Racer, LS1 & T56
Posts: 5,391
|
|
Not Ranked
That AC balance I've found is an important setting. It controls the offset between negative and positive in the AC current flow. The positive current flow is what does the cleaning action. It blows the oxide off the surface of the material. The negative current flow provides the heat for weld penetration.
It's also sometimes called "Clean Width" on the dial. You can experiment with it on some scrap material running beads back and forth and see what difference it makes. The more positive you set it you will see the bands at the sides of the weld widen as more of the aluminium is "cleaned". You'll want to set it so you get a nice neat weld with not too much discolouration at the sides from the cleaning action.
Edit* Another thing to remember/observe is the Positive current flow puts more heat into your electrode than the Negative. You will find your electrode will ball up quicker with more positive offset. With some trial and error you will a find a happy medium that works for you.
Cheers
__________________
Mike Murphy
Melbourne Australia
Last edited by Aussie Mike; 07-10-2013 at 07:50 PM..
|

07-11-2013, 04:14 AM
|
 |
CC Member
|
|
|
Join Date: Jun 2009
Location: Sydney,
NSW
Cobra Make, Engine: RCM, Jag front and rear, LS3
Posts: 1,640
|
|
Not Ranked
Picked up some stuff today. The guy at the shop said most people but zirconiated and 5356 rod. I just got 1 tungsten so will try both.
Should I ball the zirconiated on dc first or use it sharp?
I think I will go to ceriated eventually but they didn't have any.
|

07-11-2013, 04:18 AM
|
 |
CC Member
|
|
|
Join Date: Jun 2009
Location: Sydney,
NSW
Cobra Make, Engine: RCM, Jag front and rear, LS3
Posts: 1,640
|
|
Not Ranked
Also, I have seen a lot of people talking about frequency adjustment 60hz to 300hz. Is this the frequency of alternating current or the pulse frequency.
There is no option to adjust ac frequency on my machine.
Edit: I just looked at some more expensive machines and i see AC frequency is adjustable on these. My machine doesnt have this, does that mean it is 50Hz based on Australia AC supply? Can you still achieve reasonable results without this adjustment?
Last edited by Zedn; 07-11-2013 at 04:52 AM..
|

07-11-2013, 08:05 AM
|
 |
CC Member
|
|
|
Join Date: Jan 2001
Location: Sunbury,
VIC
Cobra Make, Engine: Rat Rod Racer, LS1 & T56
Posts: 5,391
|
|
Not Ranked
Mine has pulse. I use this function a bit. I sometimes dial it back to about 0.5 Hz and use the pulse function like pulsing the foot pedal. You can sync feeding the filler rod in with the high amp cycle of the pulse and make quite a neat looking weld.
Using high freq makes for a more controllable arc. Jodie on welding tips and tricks has a few vids on it.
Cheers
__________________
Mike Murphy
Melbourne Australia
|

07-11-2013, 08:11 AM
|
 |
CC Member
|
|
|
Join Date: Mar 2006
Location: Perth,
WA
Cobra Make, Engine: G-Force MkII, Ford 429, Tremec TKO, Jag Suspension, Sequential LPG Injection, On The Road.
Posts: 35
|
|
Not Ranked
Hi Zedn,
I use 2% Lanthanated Tungsten (blue tip), it works well on both AC and DC.
A sharp (with a very small flat spot) 2.4mm 2% lanthanated tungsten works well for me with the following settings: AC Freq: 120 Hz ; AC Balance: 30% + ; by this I mean the machine is DCEN (Negative) 70% of the time and DCEP (Positive) 30% of the time. This is the balance that Mike is referring to.
Frequency adjustment can also help, 60 Hz gives you a wider arc (and can work well on thicker material), 120 Hz gives you a more focused arc, 250 Hz (what my machine is capable of) just gives me a headache from the noise and I don't see much change in the weld bead !
I started out on an old transformer with fixed 60 Hz and 50/50 balance, it will give you more than reasonable results once you get your eye in.
Foot pedal control will be important to you.
__________________
Andrew
Last edited by Andrew429; 07-11-2013 at 08:14 AM..
|

07-13-2013, 12:39 AM
|
 |
CC Member
|
|
|
Join Date: Jul 2008
Cobra Make, Engine: BBF 545 Stroker Alloy Heads Roller Cam Aluminium Flywheel Twin plate Clutch TKO600 9inch Independent Rear 335x17 Rear 315x17 Front 1140kg
Posts: 292
|
|
Not Ranked
I do it every day of the week...
If you are using AC the best is Zirconiated it has a white end as Boxhead suggested.... grind a small shamfer on the electrode...
only small 1/3 of diameter of electrode ...not a point
Use straight Argon Gas
|

07-14-2013, 02:08 AM
|
 |
CC Member
|
|
|
Join Date: Jun 2009
Location: Sydney,
NSW
Cobra Make, Engine: RCM, Jag front and rear, LS3
Posts: 1,640
|
|
Not Ranked
Well it was very short lived.
To start with i found the tungsten kept burning up. I was thinking maybe it was too much current or the AC balance was wrong. After about three times with the tungsten burning up, the welder then wouldn't shut of. I tried both foot pedal and torch switch and both did the same thing. Plus it leaked gas inside. Switched to DC and it did the same thing.
Dont know whats wrong with it, but its not working. Its like it is just works at full current or something.
Organising to send it back now. Im going to get my money back and buy a better one.
|
Posting Rules
|
You may not post new threads
You may not post replies
You may not post attachments
You may not edit your posts
HTML code is Off
|
|
|
All times are GMT -7. The time now is 11:40 PM.
|
|